Weathertightness is critical. But if buildings don’t leak rain but mould and rot from interior moisture, that’s still a failure. We must get weathertightness right but we must also consider thermal performance or else we’re still stuck with crappy buildings. Thermal performance is critical because …. say it with me: “cold spots equal mould spots!”
The standard New Zealand way of installing windows is to hang them out of the building, like a drunk uni student mooning his classmates. If (when) the windows leak, the moisture has an external escape path. Unfortunately it also means the frame is not surrounded by insulation and is often cold enough to create condensation on the frame, leading to mould. Thermally-broken aluminium (and uPVC or timber) window frames can help with this but even with a very good frame, sticking it out of the wall causes additional heat loss. We don’t just specify high-performing windows in a Passive House; they are designed differently to avoid just this problem.[1]
I’ve lifted some drawings and numbers (below) from the forthcoming High-Performance Construction Details Handbook to illustrate what better windows mean for your project. We can see that the window installation improves from 0.18 to 0.04 W/(mK). That matters a lot in high performance buildings and especially when building in the colder parts of New Zealand.
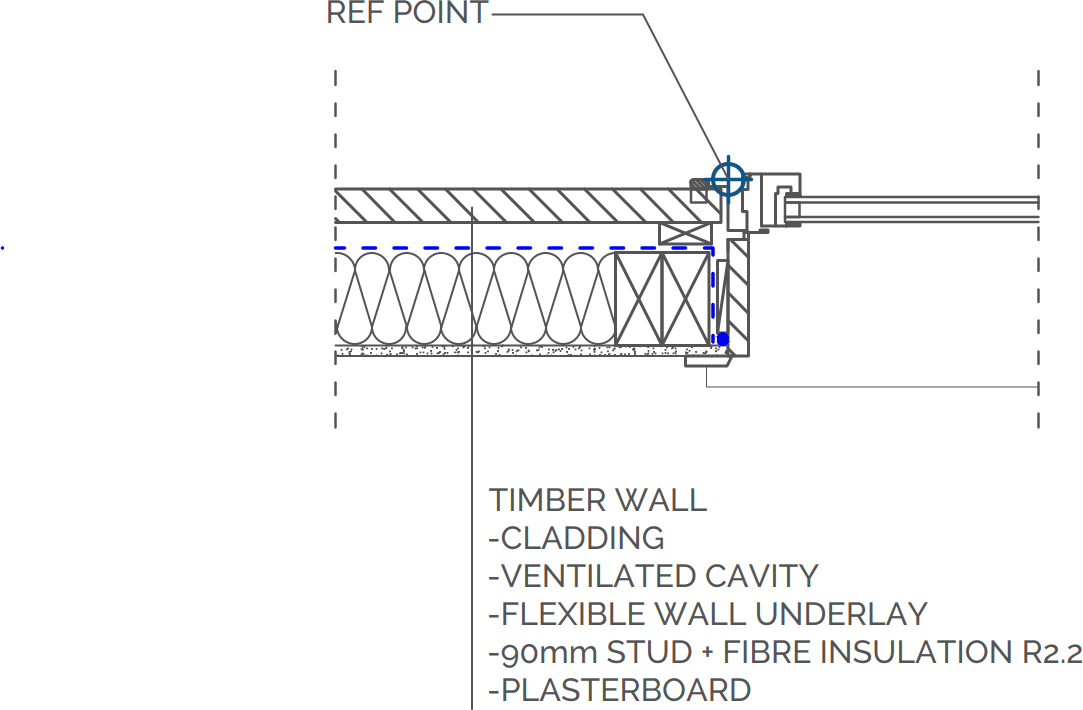
Figure 1: Standard Code-minimum aluminium window installed hanging out of the building. Even with the ventilated cladding, PSI=0.116 W/(mK).
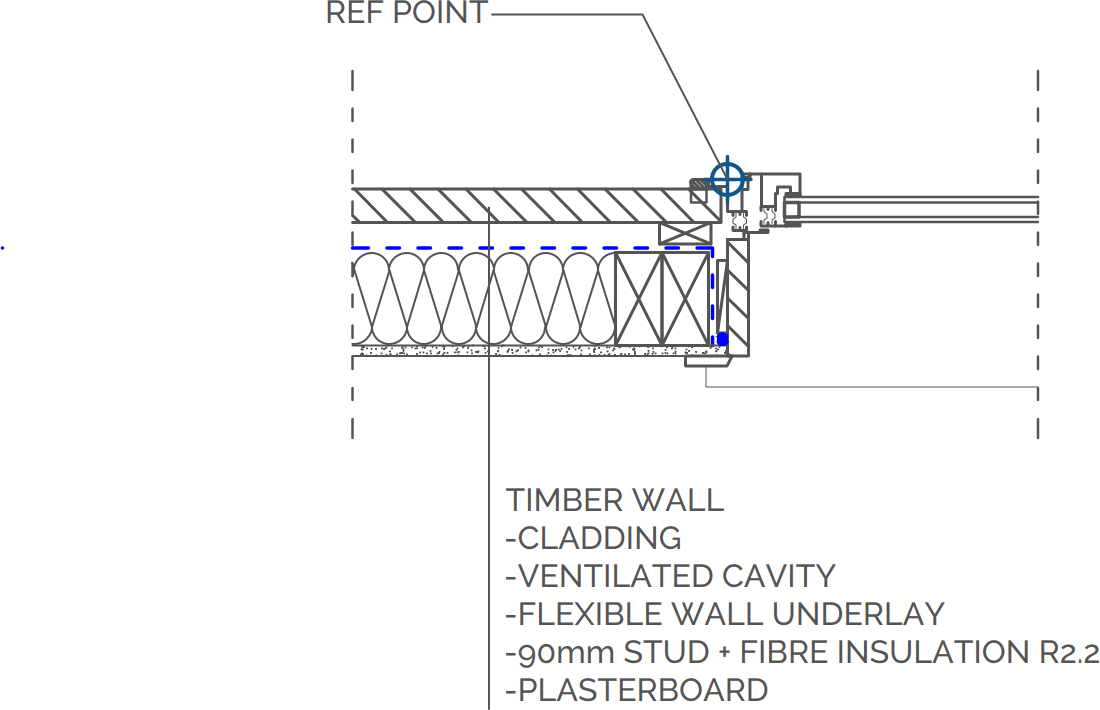
Figure 2: Better-than-Code thermally-broken aluminium window installed hanging out of the building, PSI=0.173 W/(mK). The additional heat loss at the edge is higher, because the frame is better, but even so the window with a thermally-broken frame has improved overall performance.
For a Code-minimum home, changing the window installation from PSI 0.04 to 0.17 W/(mK) while making no other improvements, is noticeable in regard to overall heat loss but not huge. It’s a 5% increase in heat loss, the same in Auckland or Queenstown.
But changing the same detail in a Certified Passive House level building has a much higher impact, increasing heat loss by 27% in Auckland and 46% in Queenstown.
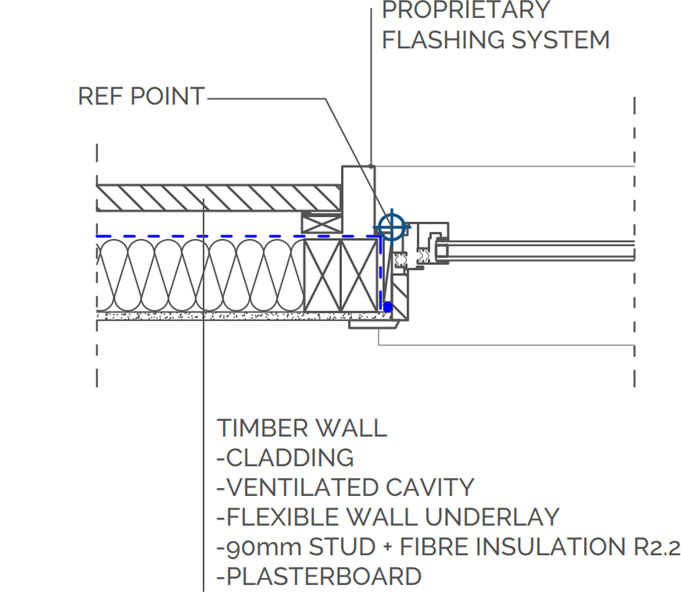
Figure 3: Better-than-Code thermally-broken aluminium window installed flush with the insulated part of the wall. It needs a flashing system but performs better thermally PSI=0.084 W/(mK). Note moving it more into the wall with only an insulated 90mm stud wall is not much better (not shown).
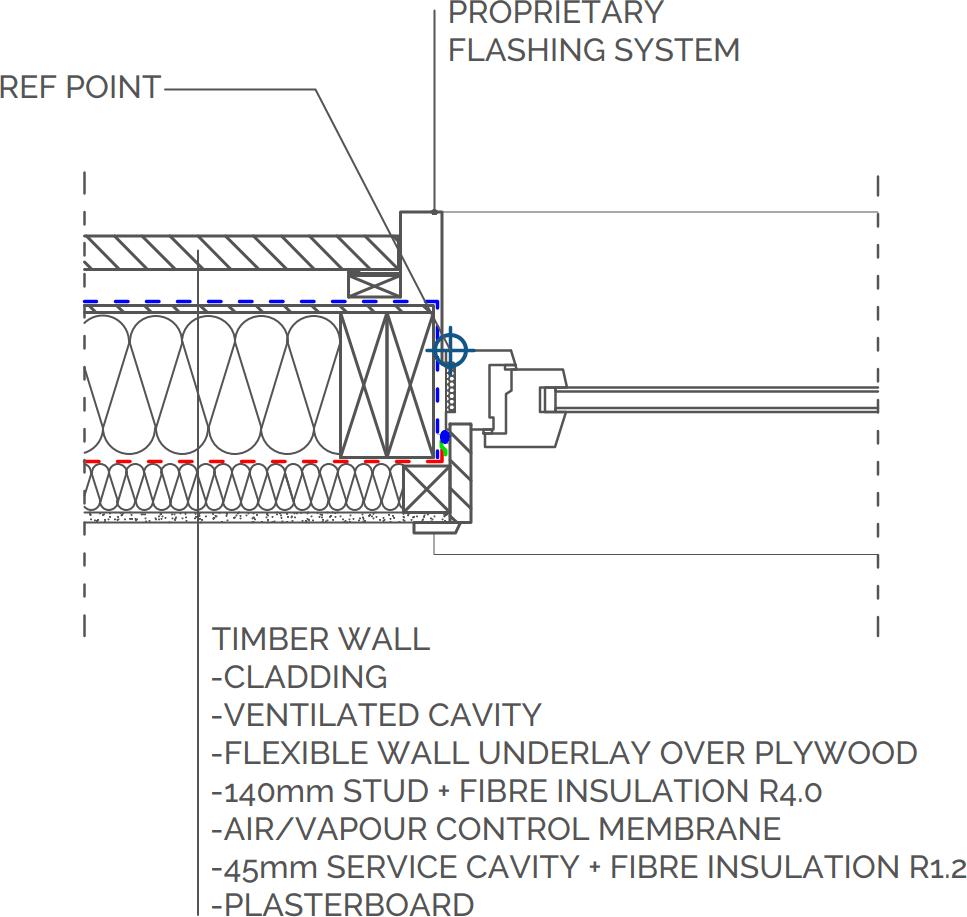
Figure 4: uPVC installed to centre of a higher performance wall PSI=0.04 W/(mK). To do much better than this would require over-insulation of the frame or not considering the additional timber in the wall near the window as part of the window.
Surface temperature factor (fRSI)
But thermal bridging and its subsequent heat losses and energy inefficiency is only half the story when we focus on preventing internal moisture problems. Surface temperature factor (fRSI) must be taken into account. It’s a criterion for the risk of condensation and ensuing mould growth at the thermal bridge and here’s where the big challenges lie. I am sticking with the conservative PHI approach of fRSI calculated with Rsi=0.25 m2K/W[2].
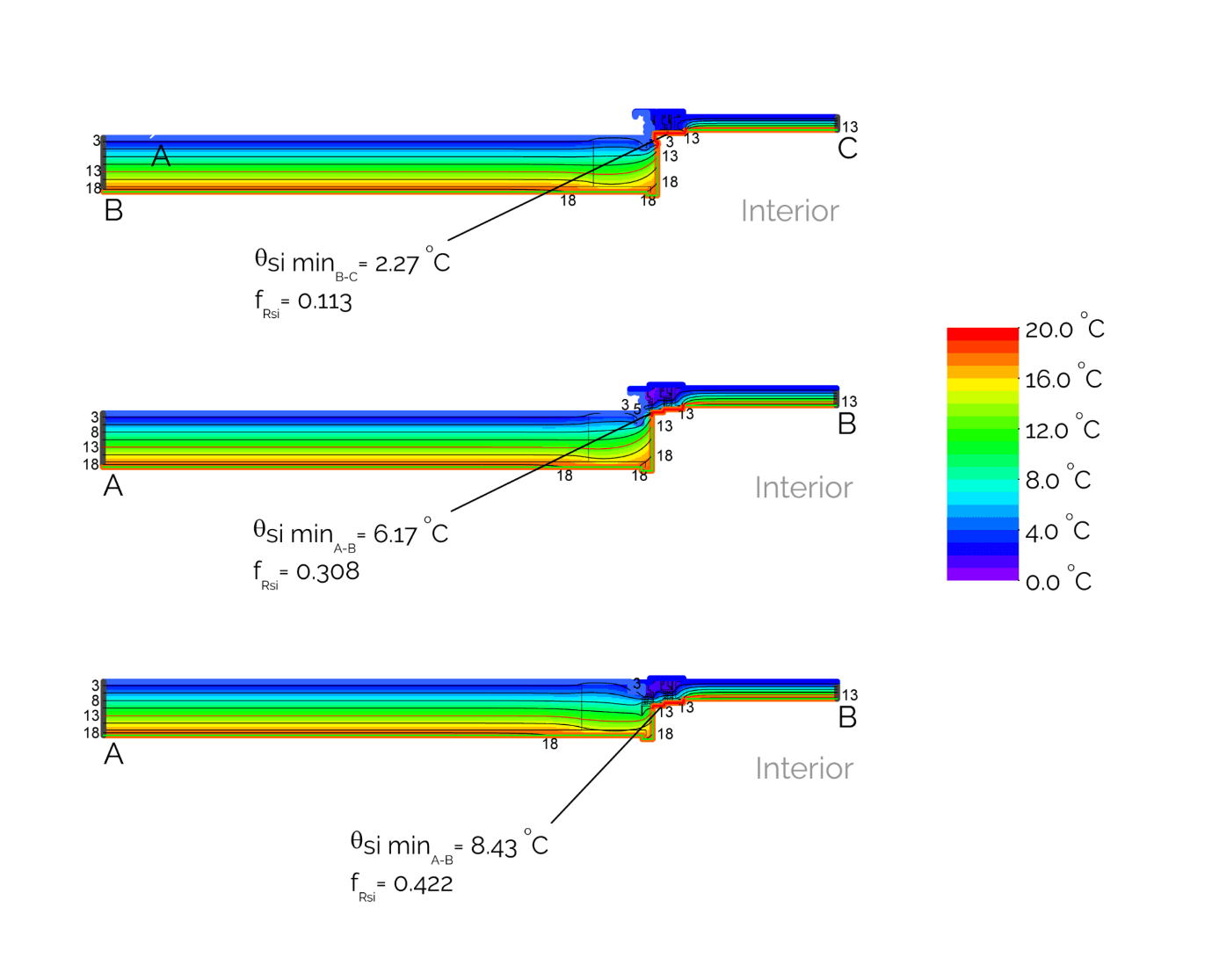
Figure 5: Impact of changing the frame type and location in the wall. Top, solid aluminium standard install. Middle, thermally-broken aluminium standard install. Bottom, thermally-broken installed flush with outside of the insulated studs. Notice the drastic increase in fRSI. This is not the highest performance thermally broken joinery available in New Zealand but is typical.
Switching to thermally-broken aluminium frames and installing the window flush with the outside of the thermally-insulated studs improves the window frame’s thermal performance a lot. But it still doesn’t meet the PHI fRSI recommendations of >0.55—even in Auckland, where it’s easiest to meet the target because of its warmer climate.
Most of the currently available, locally manufactured thermally-broken joinery can’t meet the fRSI criteria, even in Auckland. Of the joinery that does, often it’s not the whole joinery suite; the windows might meet the criteria, but not the doors or a mullion style for instance. There’s only two local manufacturers of Passive House-certified joinery; many PH projects still import a house-lot of joinery.
The fRSI criteria for climates in New Zealand’s south are much more difficult to reach: fRSI>0.65 for most of the South Island and fRSI>0.70 for Queenstown [see Fig. 6 below]. Down there, better installations and frames that can meet these fRSI criteria are needed to ensure that the window frames won’t get cold, condensate and mould.
Takeaway: opt for better joinery and installation. Otherwise, your clients will have to keep drying the inside of their windows each winter’s morning.
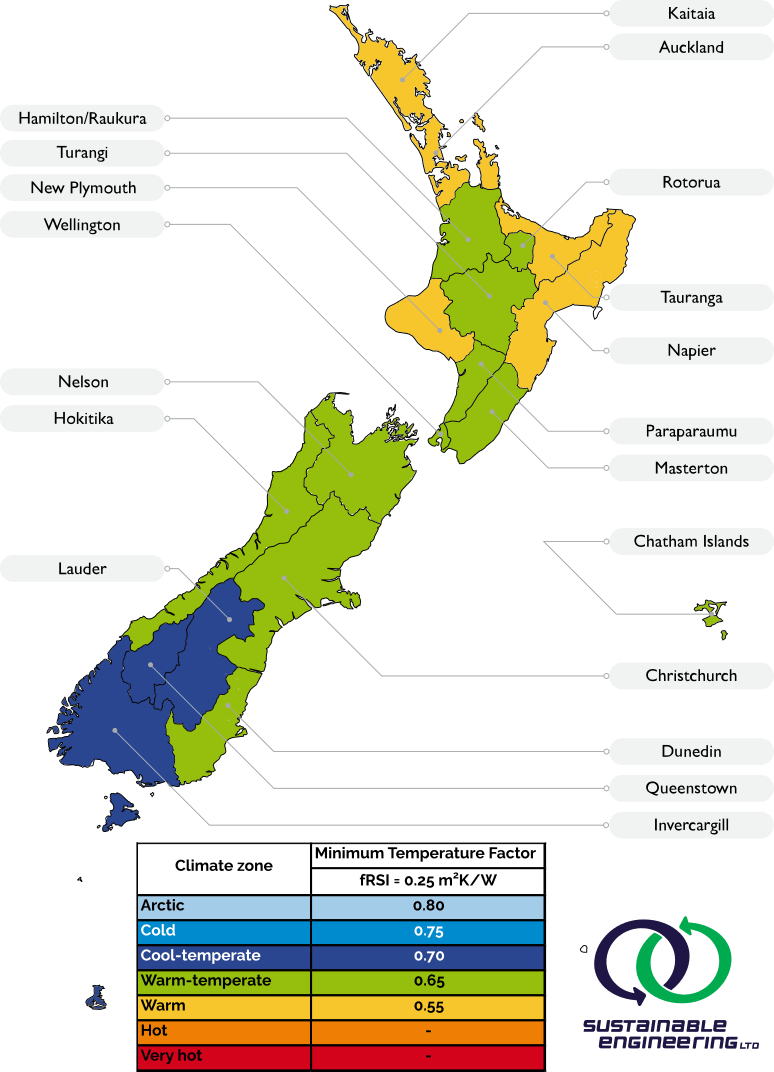
Figure 6: This map shows the three different fRSI zones at the weather station altitudes. The climate zone and thus the fRSI requirements also vary with altitude as the average temperatures typically drop by 0.6C per 100m of elevation gain. In general these zones can be used without considering the elevation change. Illustration: Sustainable Engineering Ltd. fRSI requirements from PHI Passive House Standard Building Criteria.
[1]Unfortunately due to the way our Building Code works, importing really good windows and using excellent weathertightness details can cause delays at building consent stage. It’s different (ie, far superior) to the current Acceptable Solution; therefore it’s an Alternative Solution and that means more paperwork, questions and even sometimes demands for testing. Some consent officials understand your solution is better than the Acceptable Solution. But they are independently audited and need to show they did it ‘by the book’ anyway. The only way to fix this is to rewrite the book.
[2]Yes, PHI’s fRSI requirement may be conservative—at least we can say that in the context of a Passive House building which is continuously well-ventilated (>0.3 ACH) and a comfortable temperature year round. It is still being explored what margin of safety exists in certified Passive Houses and how it may relate to buildings which are neither sufficiently ventilated or heated.