Sustainable Engineering now offers clients a schematic-level review at the early design stage that estimates embodied and operational carbon, using a modelling tool we’ve developed in-house. It gives project owners and designers hard numbers that highlight the carbon implications of different construction materials. Having that data in the early design stage enables clearly informed decision making. You can read an example report here.
In the past couple of years, international Passive House conversation has shifted markedly. Once, it was all about energy efficiency. Increasingly, the urgent discussion is around how Passive House methodology mitigates climate change. Buildings account for 20% of New Zealand’s carbon emissions. Passive House buildings use so little energy for heating and cooling that they are necessarily also efficient with regard to operational carbon emissions. But we also urgently need to measure—and reduce—the embodied carbon in the built environment.
Design principles for reducing carbon emissions
Our research highlights high-level design principles that can be used on any project to reduce both embodied and operational carbon. While not necessarily enough to meet the current BRANZ target of 35,000 kg CO2 eq, these principles lower the operational emissions to the same level as embodied carbon. This is the crucial point: in Code-minimum buildings, operational emissions dwarf the emissions from embodied carbon. Slashing operational carbon emissions has to be the first priority—and Passive House provides the methodology and the tools to do just that.
Spoiler alert: a concrete slab has a huge impact on embodied carbon numbers.
Reducing embodied carbon
- Minimise use of aluminum, steel and concrete. Specify a timber floor on piles rather than a concrete slab wherever possible.
- Use FSC-certified timber construction to maximise carbon storage.
- Timber-framed windows are the best option (even if aluminum clad), followed by uPVC and aluminum (solid or thermally broken).
- The impact of refrigerants has been included in our modelling. Currently the lowest impact options are CO2 refrigerants for DHW heat pumps (models include Apricus or EcoDan) and R32 refrigerants for heating and cooling. This technical article has more detail.
- Reduce construction waste.
Reducing operational carbon
- Reduce heating demand by increasing the performance of the thermal envelope:
- more floor, wall and ceiling insulation; and
- better performing doors and windows and glazing.
- Use electricity not gas for heating, cooking and domestic hot water. Ideally, use heat pumps for domestic hot water and heating given their efficiency.
- Reduce plug loads with energy-efficient appliances and devices (practically, this will need national policy to require more efficient units).
These principles are effective on both levels
- Consider the feasibility of shrinking and simplifying the footprint. Smaller buildings automatically reduce total heating demand and use less materials. Less complicated forms (buildings with a lower form factor) are also more efficient.
- Use durable construction systems: think of designing for 90 years, not just the minimum Building Code requirement of 50 years.
- Design flexible spaces that occupants can use differently over time to order to increase the building’s life span.
Embodied energy decision choices, ranked
- There is one single materials choice that significantly impacts the embodied energy result. If the building sits on a concrete foundation, that slab alone will account for more than half the embodied energy in the total thermal envelope.
- The second largest impact is the additional embodied energy in the aluminium window frames or standard thermally broken aluminium frames over uPVC or timber with an aluminium cladding.
- Upgrading from single, to double and then triple-glazing also increases the embodied energy—even as it improves thermal efficiency. Understanding the trade-off between embodied carbon and thermal performance is important.
Comparing variations
In testing the tool, I compared six different variations for the same building, a modestly-sized single-family home with a timber frame on a concrete slab. The first two variants are based on the actual building, constructed in 1976. I then modelled four variants with increasing levels of performance, as follows.
- Existing 1976 shape with Code loads and Code-minimum insulation: 90 mm timber walls, a truss roof with 140 mm fibreglass insulation and a concrete slab with no insulation, plus single-glazed aluminium windows and numbers from the Building Code for lighting, plug loads and domestic hot water (DHW).
- Existing 1976 with Passive House loads: the same construction as above but with Passive House loads for lighting, plug loads and DHW. It also used a split-unit heat pump for heating and an all-in-one unit for DHW (each has a COP of 3).
- Better thermal envelope: To (1) above, I added 50mm EPS underneath the concrete slab, more wall and ceiling insulation, thermally-broken aluminium windows and standard double-glazing. The same Passive House loads and heat pump as per (2).
- MVHR and uPVC double glazing: as per (3) above, but with a MVHR system and uPVC windows with better double-glazing.
- Passive House: the same construction and loads as (4) but with Passive House airtightness performance, slightly more slab insulation and triple-glazed uPVC windows.
- Passive House Low Carbon: the same construction and loads as (5) but with a timber floor on piles (equivalent thermal performance to the insulated concrete slab), aluminium-clad timber windows and a CO2 heat pump for DHW.
The results are startling. As Fig 1. (below) makes clear, the vast majority of carbon emitted by our example home is operational. To make the biggest and most immediate difference, heating and cooling loads need to be fixed first. It is quite simply stupid to focus on the embodied carbon in new buildings without also slashing the operational carbon emissions.
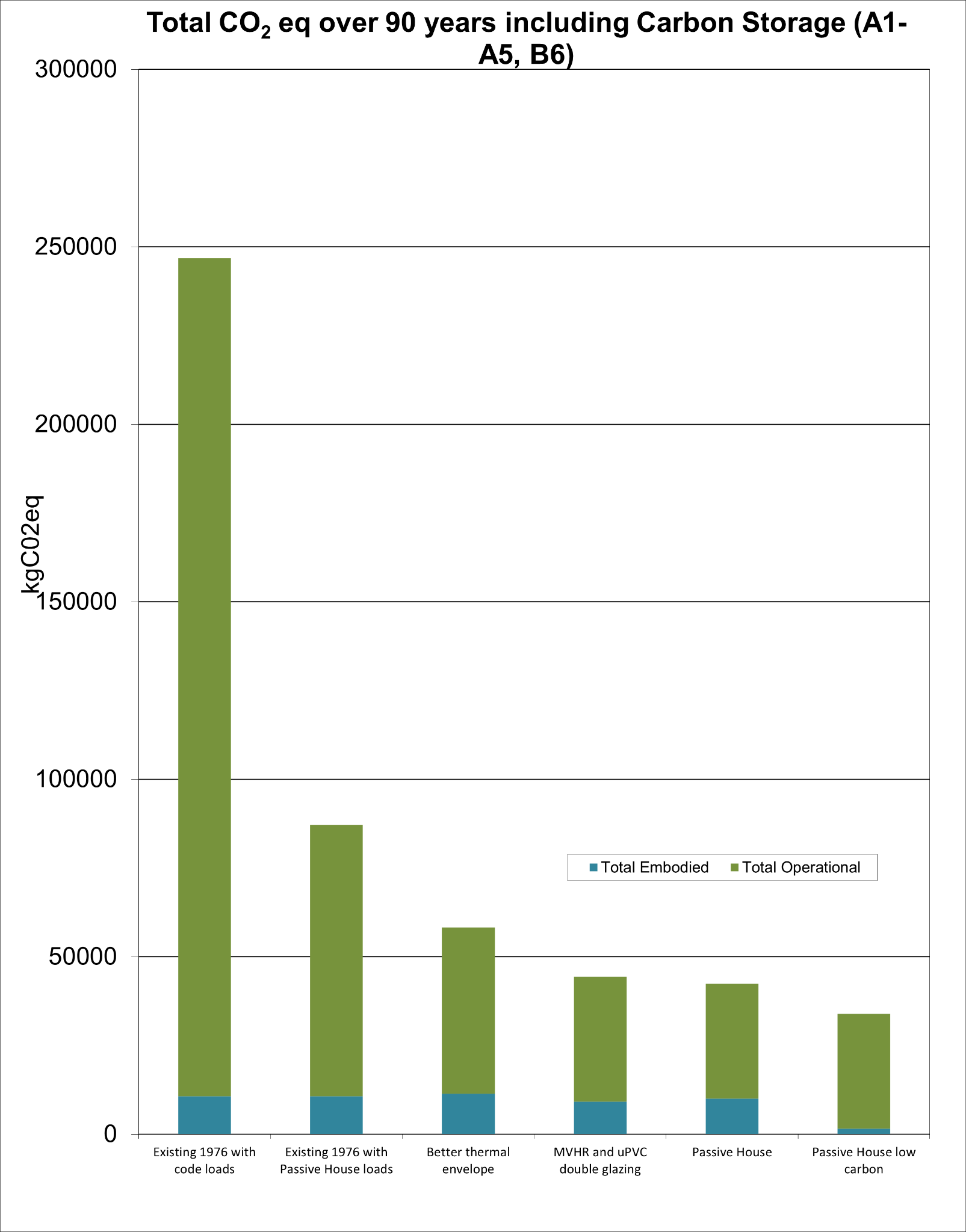
Fig. 1 Sustainable Engineering Ltd
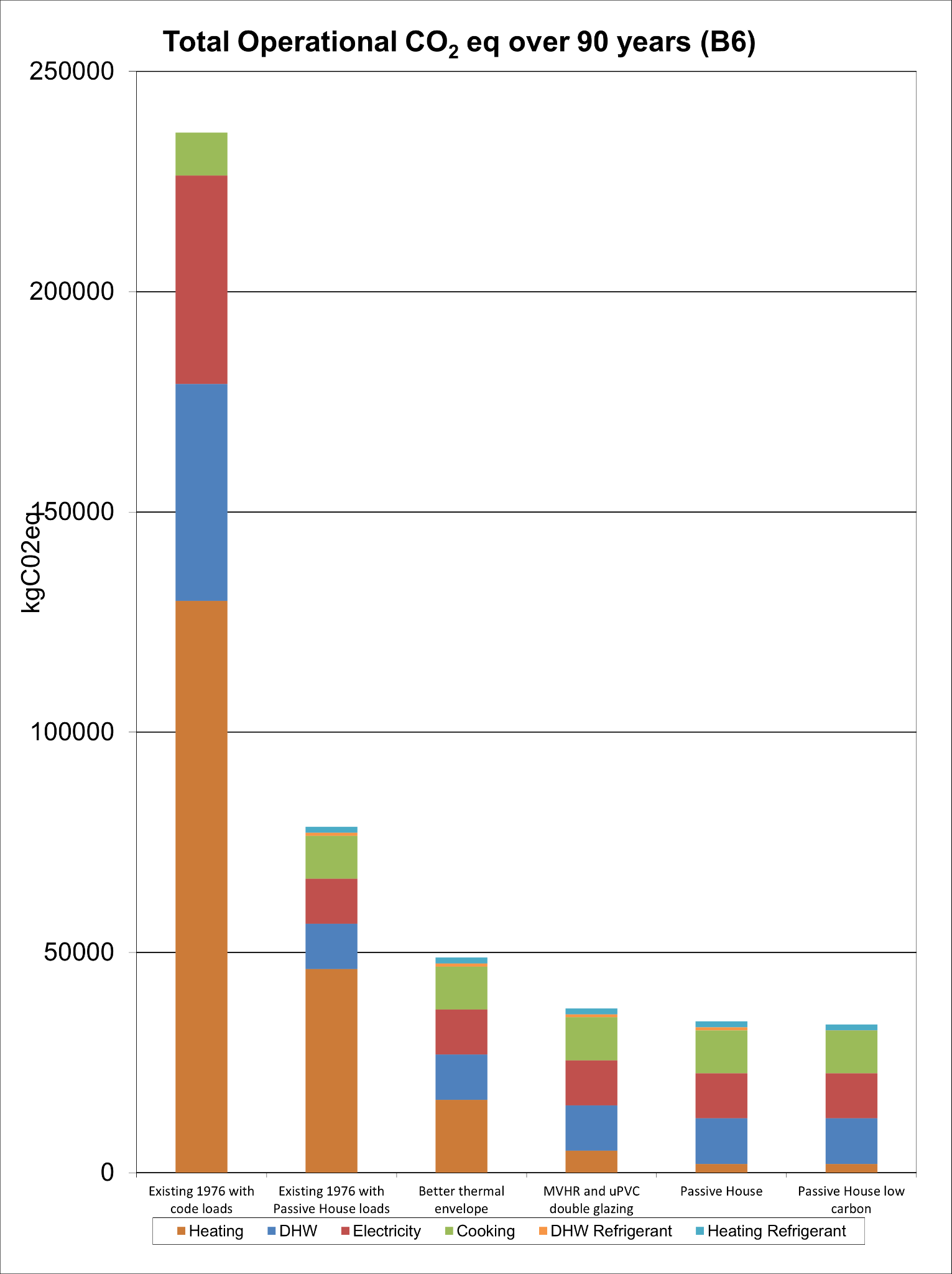
Fig. 2 Sustainable Engineering Ltd
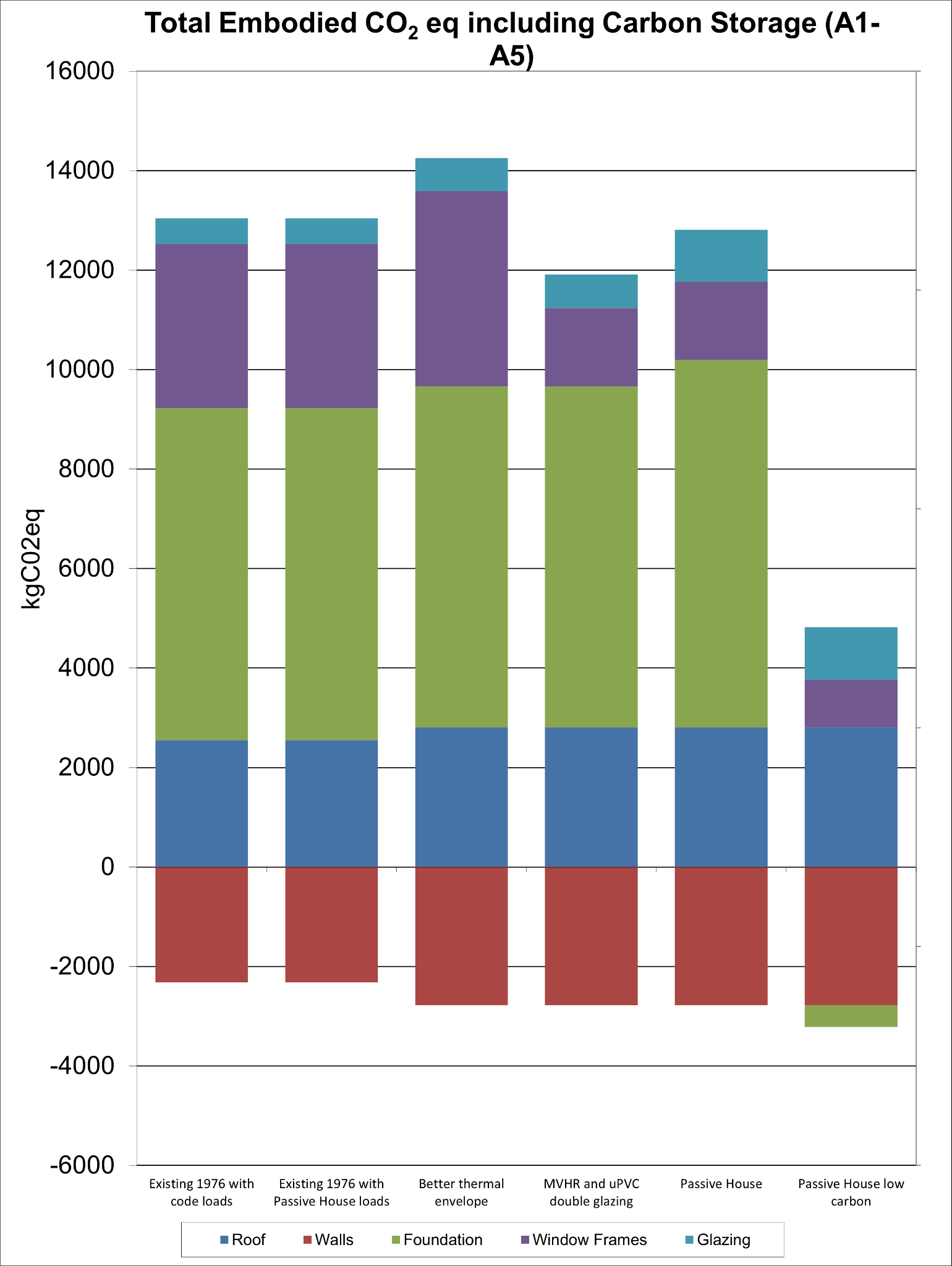
Fig. 3 Sustainable Engineering Ltd
A note on assumptions
The methodology for calculating embodied and operational carbon is still new and still being refined. It’s important to note that operational carbon is heavily impacted by the assumptions made about how a building will be used and what is included or excluded from the model.
The key assumptions that underpin our modelling are as follows.
- In all cases, the heat pumps for heating and DHW have a COP of 3 and the impact of refrigerant leakage has been included (assuming R32 for heating and R134a for DHW), except in the case of variant (6), which uses CO2 as the refrigerant.
- All the variants use electricity for cooking.
- The buildings’ operational and embodied carbon are compared over the 90-year lifespan, with a minimum interior temperature of 18 degrees.
- All the results include the impact of biogenic carbon (carbon storage).
- The timber calculations require FSC-certified timber. Carbon storage of timber in door and window frames (if present) is not calculated.
- The use of any onsite renewables is not included.
Final notes
We went to considerable effort to ensure our methodology is consistent with BRANZ’s carbon budget work and the data in the forthcoming High-Performance Construction Details Handbook. There was a lot of discussion, plus we reverse engineered the results from BRANZ’s carbon budget paper and the technical paper that preceded it. Our work has been discussed with technical staff at BRANZ and NZGBC. Our model is the best available at this time but remains a work in progress.
What does it mean when we describe this service as a schematic-level review? Life cycle analysis is based on 18 stages across four groups see Fig. 4). The schematic review encompasses the product and construction stages (A1-A5) and operational energy (B6) only. The potentially large impacts of maintenance, replacement, water use and end-of-life stages are not included.
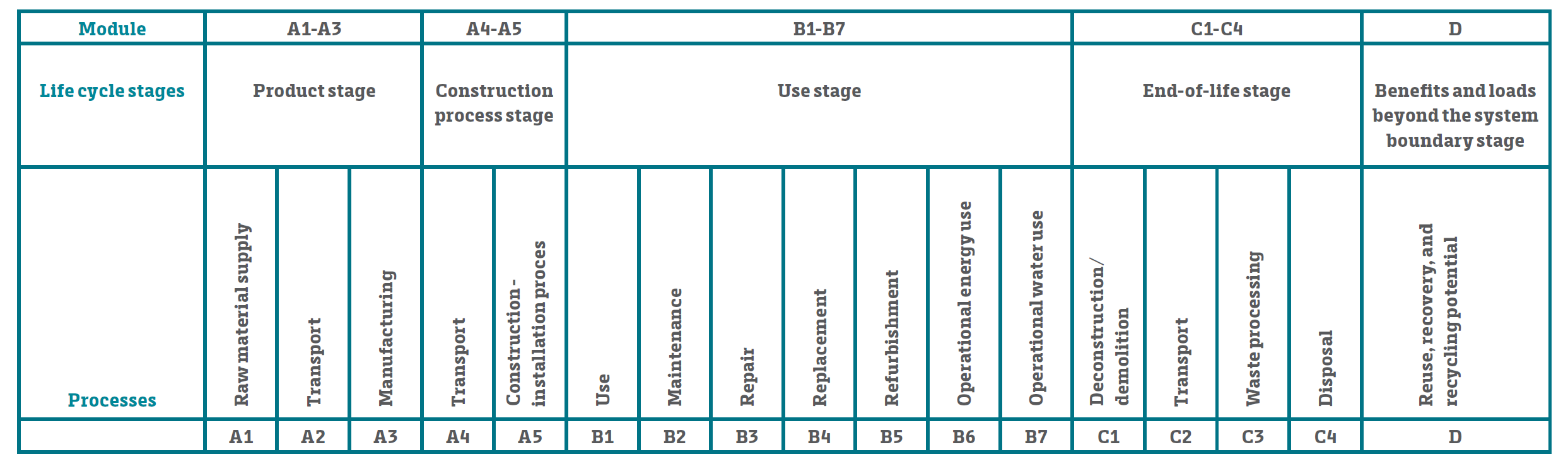
Fig 4. Life cycle stages as defined in the European standard EN 15978:2011 from “Introduction to LCA of Buildings”, Danish Transport and Construction Agency, 2016.