Āhuru Raglan
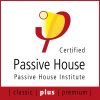
Āhuru nestles into the land above Raglan harbour, a sublime spot for an exquisitely detailed home. It is a product of a seemingly perfect match of values between the architect and homeowners. The architect was in the very first cohort to gain Passive House designer certification in New Zealand, designed this country’s second-ever Passive House and his practice has come to specialise in high-performance and certified Passive House buildings that are infused with a broader environmental sensitivity.
The owners were already set on achieving the Passive House standard when they approached the architect, being familiar with the concept and benefits from time in Canada. They shared a commitment to building for the long-term and that shaped key decisions about materials, such as brick cladding and zinc roofing. These are perfect choices for a coastal rural property in an extra high wind zone, being very long lasting and requiring no maintenance.
To their credit, the clients were willing to wait rather than compromise on the performance they wanted; some years passed between the initial discussions with the architect and when the drawings began. They lived far from this glorious Raglan site but visited regularly and camped, giving them great insight into their land. The architect’s relative proximity meant he was able to visit multiple times also. That was helpful; the careful detailing started with a thorough investigation of site datum levels, figuring out the best contour to place the house with relation to views and other factors.
Sustainable Engineering Ltd’s team provided custom thermal bridge modelling on this project. Steel portals were required due to wind loadings (glulam was investigated but wasn’t feasible in this instance) and there’s also a large pergola that shades the northern and western aspects. Modelling of these thermal bridges informed the way the connections were made back to the building structure. Clever modelling indicated the best way to secure connections for the covered walkway between the detached garage and the house. Some tricky sill details were also modelled and valued advice offered on how to mitigate the thermal implications of a skylight above the entrance that brings light deep into the home.
The energy model predicted little risk of overheating and this has been proven in practice. After 13 years of using PHPP and learning about overheating challenges, the architect has the experience to quickly identify and mitigate risks early in the design stage. The pergola is key, fitted with a shade cloth that can be manually moved. This is a permanent residence not a holiday home and the clients work remotely, so they can easily respond to changing weather.
The clients were rapt that Passive House Plus certification was achieved. It wasn’t the original target but as the design process was worked through, the architect could see how little extra was required to meet the Plus standard. The project already specified PV for grid-tied electricity generation and adding just four extra panels was sufficient to hit Passive House Plus targets.
The excellent airtightness result meant heat losses were minimised and this efficiency kept the size of the PV array down. It’s a ground-mounted system, which the architect prefers. “I’ve owned PV in my homes too, I’ve seen the mould that can build up underneath the panels. That needs to be cleaned off regularly, especially if you’re harvesting drinking water off the roof. We will ground mount PV arrays on client projects where ever possible. They’re not just easier to clean—which maximises efficient generation—it protects the roof. Roof mounted PV arrays require multiple penetrations through the roof. The zinc roof on this house, we were not going near that with PV arrays!”
The clients are professionals in the design sector and it shows in the thoroughly considered fit-out. The exposed concrete slab throughout the living areas contains specially selected local aggregates under a white oxide finish. There is extensive timber panelling and custom joinery, carried out by a master craftsman who regularly works on Tawa Architecture projects. The kitchen ceiling is astonishingly intricate. However, sitting as it does below the airtight layer and service cavity, it has no implications for thermal performance.
The treated floor area is a respectably modest 143m2 for three bedrooms and two bathrooms. It’s been designed to perfectly suit the owners but with an eye to future use. “We take a very long term view of homes,” says the architect. “I want to design homes that will last a hundred years, where many people can fall in love with them over the life of the house. The internal fitout can be changed or adapted to suit different needs over time. This really suits our fabric-first approach to Passive House.”
It was a perspective the clients were entirely on-board with; they already had a preference for brick cladding for instance, and they sourced the unique bricks from a New Zealand supplier. It’s a marked contrast to the cedar claddings so ubiquitous on modern architecturally designed builds that the architect doubts would survive even 50 years in these challenging conditions.
Construction was carried out by a Waikato firm experienced in Passive House construction. Their team knew what they were doing and got on with it; the clients greatly valued having contractors with a demonstrated track record.
Other sustainable features of the house include a vermiculture-based wastewater treatment system, the use of permeable paving wherever possible, rainwater harvesting and the use of new timber products that remove the need for toxic CCA-treated timber.
Āhuru is a verb meaning to be warm, comfortable, cosy, comfy … and this special home is that, and much more.
Project Team
Architecture & Passive House Design TAWA Architecture Ltd - tawaarch.co.nz
Interior Design Kim Salt
Builder Brown Construction - brownconstructionltd.co.nz
Interior Joiner Rik Ball - tracymcewendesign.co.nz
Certifier Sustainable Engineering Ltd – sustainableengineering.co.nz
Passive House Metrics
- Heating Demand14.6kWh/m2/year
- Heating Load12.2W/m2
- TFA143.1m2
- Form Factor3.9
- Air leakage @ 50Pa0.3 ACH/hour
- PER demand30.8kWh/m2/year
Passive House Database - TBA
Construction Details Average Values
- U-value External Walls 0.18 W/(m2K)(R5.49)
- Cladding / Ply RAB / 140 Timber Wall with fibre Insulation / SIGA Majpell / 45mm Service cavity with fibreInsulation / Plasterboard. Several walls 140 service cavity insulated.
- U-value Floor0.24W/(m2K)(R4.16)
- Concrete slab MaxRaft 250 insulated floor with brick edge
- U-value Roof 0.16W/(m2K)(R6.33)
- Truss Roof with 150mm fibre insulation / SIGA Majpell / 135 fibre insulated service cavity / plasterboard
- U-value Glass0.64 W/(m2K)(R1.56)
- PlaniTherm XN (4:/18/4/18/:4 90% Ar)
- U-Windows1.1 W/(m2K)(R0.9)
- EcoWindows Premium 78mm profile
- Ventilation Efficiency 76%
- Zehnder - ComfoAirQ450