Significant effort and cost goes into creating air control and thermal control layers in any Passive House structure so putting a ceiling hatch through them is clearly problematic. With minimum roof insulation of R6.6 roof now mandated, a poorly insulated hatch is a gaping hole that will leak more heat than the rest of the roof combined. In Code-minimum buildings these hatches are notorious for impacting performance and creating structural risk. Moist air is drawn into the ceiling space, which then condensates against the underside of a cold roof deck, risking rot and mould.
My TLDR; take on this: avoid ceiling hatches where possible as they add complexity and cost. If you can’t avoid them, make sure what you buy or build is fit for purpose. Don’t waste the money your clients have spent on insulation.
Best option (and the other option)
My first choice for an install is to get outside the thermal envelope. Depending on the building’s roof pitch, it may be an option to install the ceiling hatch in a soffit, porch ceiling or even a wall hatch in a gable end or the wall from the (unconditioned) garage. This is perfectly adequate for maintenance checks and trades access.
However, ceiling hatches with fold down stairs are being promoted for opening up storage possibilities and your clients might be keen on ready access to the ceiling space inside the house. Make sure they have realistic notions about how much space is available after the insulation is fitted. Nothing is free up in that space. If they want laddered access to storage, platforms will need to be constructed that don’t compress the insulation and don’t trap moisture in the insulation. If the hatch, with or without stairs, really needs to be inside the house then it must be up for the job. Choose from two options: buy a product that can do the job with regard to insulative and airtightness performance, or build one that is up to scratch.
Don’t do this
Do not use a product like this metal hatch or a panel hatch. These are designed for access to spaces inside the thermal envelope when the ceiling is a fully conditioned service space—as it should be in schools and commercial buildings. These are cheap and do a good job but only in the circumstances they are designed for! They are often misused.
You could try to upgrade a locally stocked ceiling hatch but I’m not certain that the airtightness is sufficient. This one from Vent (below) might work in a high-performance home; but it is not tested for airtightness so would add risk for a certified Passive House project. These are a good choice for a Code-minimum home as they are designed out of non-conductive materials, are insulated with 50mm of XPS and are supposed to be airtight.
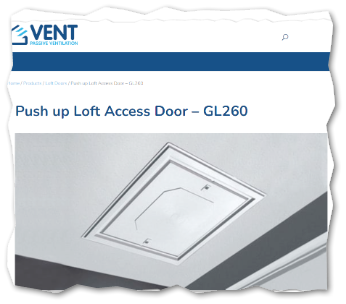
Access hatch supplied by Vent
Buy off-the-shelf
It is much easier now to purchase a product off the shelf that is suitable for a building targeting Passive House certification. See for example these options from specialist distributor 5 Merchants; the top-of-the-line model is illustrated below.
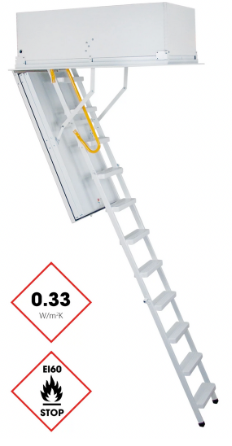
Type 1 Passive Plus Attic Stairs supplied by 5 Merchants
There remains the option to import a suitable product; joinery suppliers like Ecowindows have imported hatches to order before. I recommend you specify a certified Passive House product, especially if you (or the homeowner) choose to import directly without going through a locally based middleman. You’ll be on your own should there be other issues that create incompatibility with New Zealand ways of building.
Count on doing some calculations during energy modelling. Your certifiers can see from the cross section that a hatch is thermally insulated, but air tightness will need to be demonstrated. If the hatch has been certified, the calculations and testing have already been done. Opting for a bespoke or uncertified product means someone on your project has to pay for that work to be done.
Pay close attention to the R-value of the hatch. If the R-value is low, the roof will need significantly more insulation to compensate if you intend to use the schedule or calculation methods to demonstrate compliance with the Building Code. Factor that into the cost and it will make the actual hatch product look cheap. The other option is to ensure the hatch is insulated to the same level as the roof. However, a building targeting Passive House certification will use the modelling method to demonstrate compliance anyway. So include the lower R-value of the hatch (if relevant) in the proposed model but not the reference building.
Make your own hatch
Building a suitable hatch on site is not rocket science. If you’re going to have to hand-calculate an off-the-shelf solution anyway, you could hand the job to your builder to construct. This excellent article from a good hands-on architect, Steve Baczek, is a good explainer. His comments about how to visualise (or draw) the hatch within the red line of the thermal envelope are helpful.
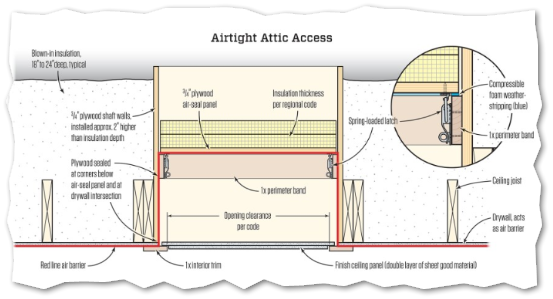
Building your own hatch. Image and guidance from JLC.
There are some useful pointers and explanatory photos in this US article about installing an off-the-shelf hatch, where the author concludes he could have easily built it himself. He also contends with blown-in insulation in the ceiling space (a common product in the US), which required some extra detailing for the hatch. Insulating and airtighting a ceiling hatch is a common DIY project in cold climate US and homeowners can buy compression seals and gaskets for airtighting off the shelf at hardware stores.
Whichever kind of hatch you use, give attention to this junction during both preliminary and final blower door tests to ensure there is no air-leakage.
Why is a ceiling hatch even required in a high-performance home?
The NZ Building Code requires an entrance to all “accessible” roof spaces. My view, shared by some experienced Passive House builders, is that a truss roof with R10 or even R7 batt insulation is no more accessible than a skillion roof. What is the point of getting your head through the hatch? You can’t move around in the ceiling space; insulation extends above the bottom chords of the trusses so you can’t see where to walk. There’s likely no headroom anyway. If access to the ceiling space is required in a skillion-roofed building, tradespeople go through the roof. I think the same approach should apply in the case of inaccessible-for-all-practical-purposes truss roofs. But I don’t write or enforce the Building Code. If anyone does take this argument to their consenting officials, I’d be interested to hear the outcome.
Note that all products are listed purely as a service for readers. The author and Sustainable Engineering Ltd are not endorsing any specific product; there are certainly other suitable products we have not noted here. Sustainable Engineering Ltd does not publish affiliate links.