I caught Joe Lstiburek’s presentation in Wellington last month. It was the same Powerpoint deck I’ve seen before—I did summer school with Joe in Massachusetts in 2014—but it was good to hear it again because his views on how to build better buildings are important. He pulled in big audiences—props to RoofLogic who organised three public talks plus private meetings around the country—from across the building industry, including designers, builders and component manufacturers.
As I expected, Joe focused on water tightness — keeping external moisture out—rather than the need to also remove internal moisture ie continuous mechanical ventilation. Joe has in the past acknowledged that internal moisture is a problem, but says that seeing as we still can’t keep the rain out properly, fix that first.
The main way that moisture gets in from the outside is through exterior openings. Take windows, of which there are two kinds, according to Joe: those that leak and those that will leak. One in 10 leak on installation he reckons, rising to 40% after 10 years. That didn’t matter before wall insulation, because incidental moisture simply dried out in the wall cavity. But incidental water is no longer incidental, because when we make buildings more energy efficient they can’t dry out as well.
Joe didn’t go into to this, but the US industry now fits . It means that when the windows leak, the water has a pathway to drain out of the wall assembly rather than being trapped inside. This works. Instead, the industry here tried to prevent moisture leaking into the wall cavity by pushing the windows out, so the face of the window is in line with the cladding rather than the insulated wall. It solves one problem but creates another. It increases heat loss around the windows and it’s especially problematic if higher-performance windows are fitted in this way. The joinery is no longer thermally broken as the bit inside the thermal break is in contact with the cold exterior air in the ventilation cavity. Thermal bridging equals cold and cold means mould.
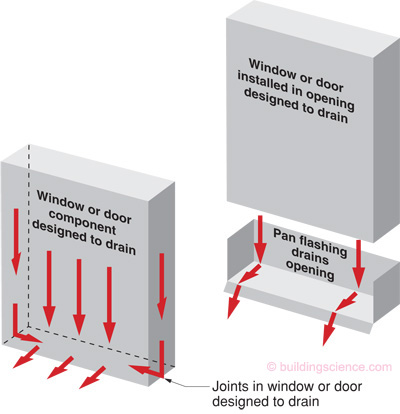
Figure 1: Great introduction to window installation at https://www.buildingscience.com/documents/information-sheets/pan-flashing-for-exterior-wall-openings
Joe pointed out that we’re building with different materials compared to 100 or even 50 years ago and that nothing is as durable as 1000-year old timber. Using different materials demands we build in different ways. “There is a force field around New Zealand not letting new ideas come in. Let ideas in!” he said. “Just don’t use the stupid ones.”
(He also called us “phenomenally interesting” because there is such climatic variation within one small country. Joe claims New Zealand is the only industrialised country in the world that “gets an insane amount of rain everywhere”. Those on the east coasts may disagree with this generalisation but it’s probably still fairly accurate compared to land masses like the US.)
Given our rainfall and humidity, you’d think we’d be better at building to manage it. But we didn’t have to be until comparatively recently because we were so behind at installing proper levels of insulation. That’s why older houses are generally solid. Water gets in, but it can easily dry out. Repeat Joe’s mantra, all together now: “Wetting followed by drying is ok. Wetting not followed by drying is not ok.”
Drying is simply an exchange of energy. Insulation reduces the exchange of energy. Having changed the drying potential, you have to change the wetting potential, says Joe—which takes us back to insufficiently detailed exterior openings and other ways that rain gets in.
As an interesting aside, Joe says it wasn’t “bad wood” (untreated radiata) to blame for the leaky building crisis in the early 2000s, but bad building practices and adding insulation without fully realising the implications and accordingly increasing the drying potential. The homes that leaked used perfect barrier assemblies, which in theory worked absolutely fine. But it’s impossible to build them perfectly. It’s the nature of construction that there will be defects. This design had no allowance for failure. Moisture wasn’t supposed to get in. But it did, and without a plan or a means for it to be dried out, it caused buildings to catastrophically fail.
Joe argued that Canada is not a good place to look for solutions to New Zealand building problems (“Vancouver is screwed but for different reasons”). I’m not convinced by his argument that Auckland is more accurately compared to Memphis than Vancouver: Memphis gets much hotter and colder than Auckland. But his point about the seasonality of our climate is important.
In New Zealand it’s better to have no vapour barrier than have it in the wrong place. In winter, inside the building is warmer inside than outside. That temperature difference means moisture moves toward the cold, ie through the walls to the exterior. In summer the hygrothermal drive switches direction: hopefully it’s cooler inside than outside (and certainly will be if the building is running AC) and so moisture will move in through the walls.
Joe didn’t mention foil-backed gypsum board, but I know he was thinking it. This is no longer used thankfully, as it as a Known Bad Idea, especially in a climate like Auckland. The foil lined the exterior side of the gypsum board, meaning moisture moving from the exterior into the house would be blocked, condense and cause mould.
The short version is never install a vapour barrier in a wall assembly in Auckland—at least without very expert, specialist advice and for very good reason. I’ll go into this in more detail in a future newsletter as it really deserves a month all to itself. Fun facts to leave you with: vinyl wallpaper is a vapour barrier, another reason to avoid it. Large mirrors and artworks also, so back-ventilate them. And make cabinets backless so air can circulate.
If you couldn’t get to Joe’s talks, then settle back with a beverage and watch this presentation to the Berkley lab. It’s classic Dr Joe and unlike the curiously stony-faced Wellington crowd, this audience laughs at all his jokes.