Significant changes are proposed to minimum Code requirements for commercial buildings in Australia and I’ve been particularly interested in measures to mitigate condensation risk in walls. It’s important New Zealand Passive House designers and architects focus on those measures aimed at the parts of Australia with heating-dominated climates similar to ours.
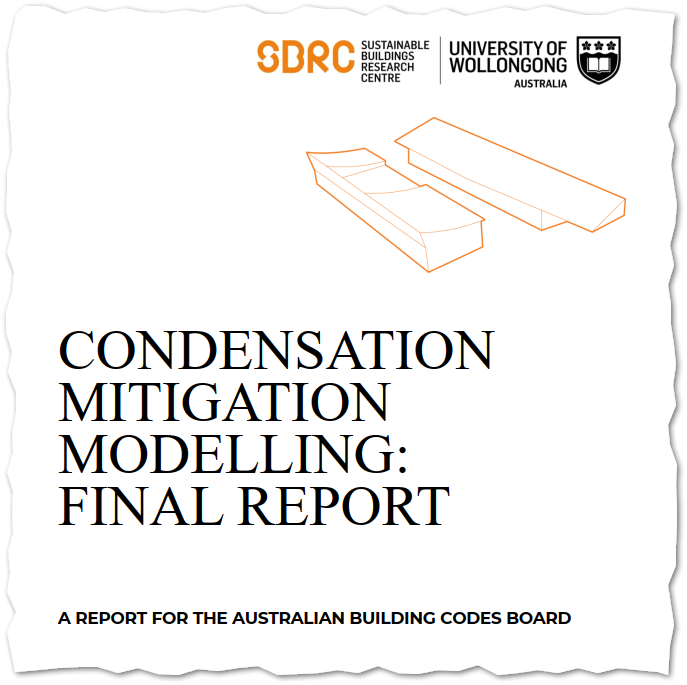
This report from the Sustainable Buildings Research Centre (SBRC) at the University of Wollongong forms the technical basis for the proposed changes to Australia’s National Construction Code (NCC).
The report findings are worth reading, but here’s a summary if you don’t have the time. In heating climates similar to all of New Zealand, the key solutions to reduce the risk of condensation and therefore mould were:
- Select membranes with a high vapour permeance for installation on the outdoor side of the primary insulation layer. (This only applies to heating-dominated climates; it’s flipped for cooling-dominated locations such as Darwin.)
- Ventilate cavities.
- Ventilation. The report says, “adequate levels of ventilation can be extremely effective at mitigating the simulated risk of mould growth, especially when combined with other mitigation measures, such as appropriate membrane selection and ventilated cavities.” In the specific examples modelled, adding approximately 0.33 ACH of continuous mechanical ventilation reduced the risk of mould growth substantially.
The report goes on to say, “a decision would need to be made as to whether natural ventilation should continue to be allowed as an acceptable means of ventilation under the DTS provisions.” (DTS means Deems to Satisfy. We’d say Acceptable Solution.) That’s very mild language but at least it puts a balloon up. I imagine even this would terrify or outrage those few Ministry of Education officials in New Zealand who so strongly cling to “natural” ventilation despite the evidence it doesn’t deliver acceptable indoor air quality in schools.
My view, as previously aired, is that if windows in a building can be closed, then continuous mechanical ventilation should be installed. Of course what I’m really saying is that mechanical ventilation is essential, not a nice-to-have extra. For ALL buildings, whether they are new builds or existing structures.
One thing I really like about the report format is that the results from many hygrothermal models were tabulated graphically. I believe that a more vapour tight internal layer or better internal humidity control will be needed for the colder climates. Looking at the results for a timber stud wall with ventilated cladding only the most vapour open membranes meet the requirements for the mould index. This specifically means that many RAB products would NOT be acceptable without something like Intello on the inside.
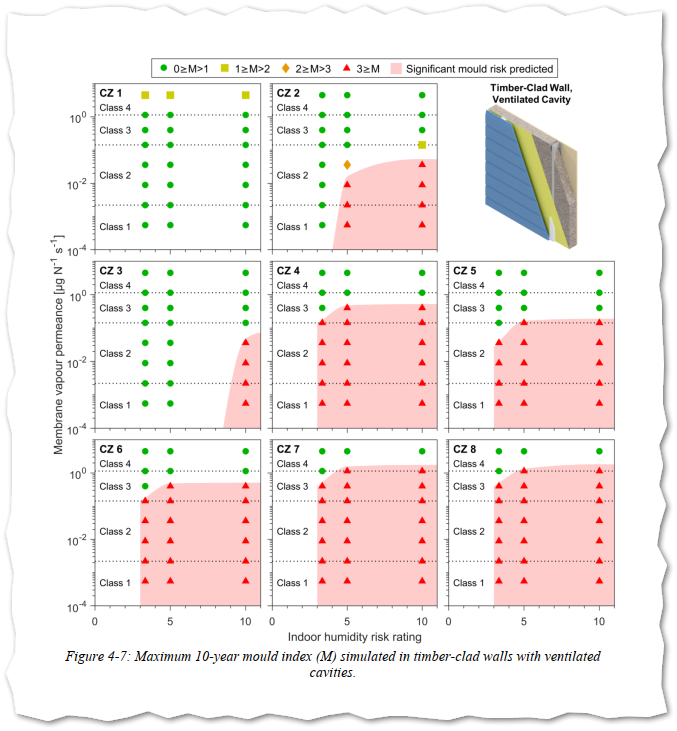
Reference Condensation Mitigation Modelling: Final Report, Alan Green, Steven Beltrame, Georgios Kokogiannakis and Paul Cooper, U. Wollongong, Oct 2023