There is a big obstacle to improving the performance of New Zealand buildings and the health and comfort of people who live in them. Nobody wants to talk about it and fixing it is politically embarrassing. A solution is also disagreeable to that part of the construction industry that likes business-as-usual and which exercises considerable lobbying clout.
The problem in a nutshell: the NZ Building Code H1 Energy Efficiency Acceptable Solutions (and Verification Methods) allows for very wrong inputs into the thermal calculations and models that are used to show Code compliance. The worst example is how the timber fraction in walls is calculated. The fraction is the percentage of the wall area that is timber; the more timber, the less insulation in that area of wall. The way this percentage is calculated is considerably over-simplified and it produces results that are inaccurate by a very large margin.
The very mechanism that establishes the minimum quality one is legally allowed to build itself provides direction that ensures results are far from reality. This results in several pressing problems. Walls built by conventional methods following Building Code guidance comply with the regulations even though they do not in reality provide the wall insulation performance stated. They underperform not just by a little bit, but a lot. The actual heat loss from a 90mm timber stud wall with an average timber fraction would be 25% more than the value used for Code compliance.
If that’s not bad enough, assuming incorrect timber fractions in Code-minimum constructions distorts the comparison with alternative wall systems or build-ups that perform much better. I’ll discuss this more below, but it is a kick in the guts to local manufacturers who are supplying higher performance building components.
The problem
The New Zealand Building Code H1/AS1 (fifth edition) sets out what timber content to count and what to disregard. Following this direction produces a timber fraction of 16% in a 90mm stud wall with studs on 600mm centres. Last year, Beacon Pathway produced an extensive research report which found the as-built average percentage of timber framing in that same wall was actually 34%. That’s not a rounding error.
1 Thermal Bridging in External Walls: Stage Two. Report Wall/4 by Beacon Pathway “Measurements [by Beacon Pathway] made of 47 newly constructed houses in Auckland, Hamilton, Wellington and Christchurch found the average percentage of timber framing compared to wall area was 34%.”
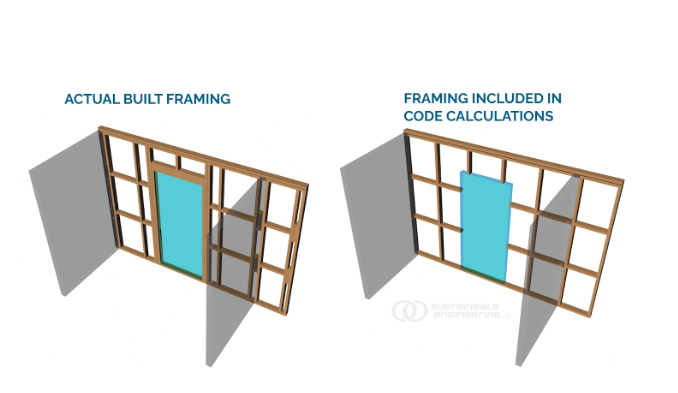
Figure 1: The actual timber content in the wall is shown in the left image, totalling 43% of the wall area (door area is excluded). The definition of timber content contained in H1/AS1 5th edition counts only the timber shown in the image on the right (timber content 16%).
The real world timber fraction means that timber stud walls as typically built won’t perform to R2.0 in reality. It wouldn’t even meet the superseded requirement (R1.9 in most of New Zealand). Actual performance is more like R1.6. Continuing to neglect much of the timber in the wall is misleading, even if legal.
The roadblock to better building
Various local manufacturers and importers of building components and systems are offering choices with better thermal performance [see disclaimer, below]. It makes sense that they compare their superior products etc with the alternatives that only comply with Building Code minimums for insulative performance.
However, the fictional timber fractions allowed for in the Code totally distort this comparison. It creates misleading inaccuracies and undermines those intent on improving New Zealand’s poor state of housing.
Let’s take a case in point that is particularly distorted. Consider the comparison between a wall that uses a higher-performing wall insulation (closed-cell spray foam (CCSF)) between an optimised timber stud layout and a fictitious reference 90mm stud wall whose timber fraction is calculated per the Code H1 Acceptable Solution. The high-performance building has been modelled accurately in absolute terms. But the reference building wasn’t and is based on flawed assumptions. The result is misleading (and wrong): the higher performance wall appears as if it’s only just better than the standard alternative.
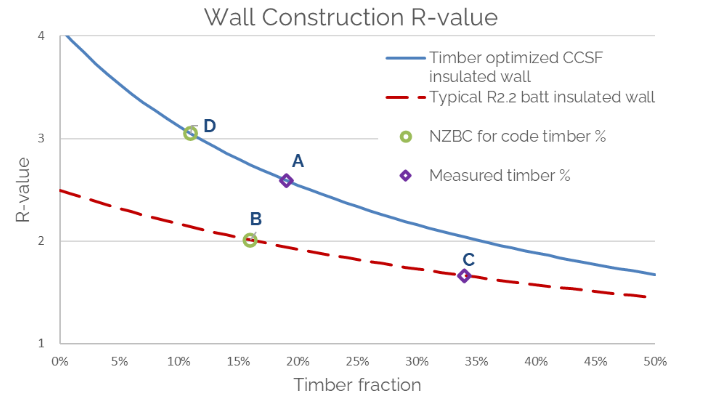
Figure 1: The overall wall construction R-value as a function of the timber percentage for a 90mm stud wall with gypsum lining and ventilated cavity for the two different insulations: R2.2 fibre insulation and R3.7 Closed Cell Spray Foam (CCSF).
This is shown above. The obvious comparison is between A and B, which compares the measured timber fraction (19%) for the optimised CCSF insulated wall with the assumed timber fraction of a standard wall. CCSF has better thermal performance compared to a typical R2.2 batt so even on this basis, it performs better (R2.6 compared to R2.0). But the gap between the performance of the two walls is wrong. It’s more accurate to compare the actual measured timber fractions of both walls, points A and C. That is reality: the optimised CCSF wall insulates 60% better than a typical Code-built wall (R2.6 vs R1.6).
This situation of oversimplified and misleading timber fractions creates multiple levels of distortions. Because no-one acknowledges the gulf between assumed and built timber fractions in standard wall assemblies, manufacturers are forced to distort their comparisons in order to produce a fair comparison (measuring Point D against B).
Timber use in many high-performance wall assemblies, such as structural Insulated Panels, Insulated Concrete Form or even straw bale, is drastically different to a standard 90mm stud wall. There is no accurate way to compare their performance to the H1/AS1 wall R-values without explaining how far from reality the heat loss using the permitted timber fraction is. This creates another barrier to the uptake of superior products.
How this happened
Why is there so much extra timber being added into wall assemblies?
These photos are from houses included in Beacon Pathway’s research that had very high timber fractions in wall framing (left) and corner framing (right). The report’s authors note these areas of walls will be almost completely uninsulated.
The Beacon Pathway report says it is not due to builders adding timber on-site. Although this did happen, it was a very small amount. It went on to claim there are “no indications that frame and truss manufacturers are adding unnecessary timber in the panels they construct”.
I don’t share their conclusion. The experience of my team and of the many high-performance builders we talk to is that it is very difficult to persuade the prenail manufacturers to use plywood for bracing and leave out nogs. It usually requires a few visits from the builder and a call or two from the structural engineer. All this, to remove timber exactly in accordance with NZS3604.
(One client, an independent builder with exacting standards, hand-built his framing on site in order to tightly control the timber fraction. Another experienced Passive House builder prefers to build with his own prefabricated timber panels. This provides multiple benefits, including minimising timber fractions.)
Let’s not overlook either the obvious consequence that unnecessary timber in prenail framing increases costs even as it lowers thermal performance.
Fixing this mess
I hoped the recent NZBC H1 update would fix this longstanding error but I believe lobbying and the political optics prevented it.That is a genuine shame.
There is really only one option to fix this problem: change the Building Code. That wouldn’t require calculating the timber fraction in every panel, although that would be best practice and potentially easily done by prenail frame manufacturers. The alternative is to rely on Beacon Pathway’s research and take the measured average of 34% timber.
I do understand why regulators/government officials and politicians aren’t keen to change this. If the Code were changed to reflect the actual average as-built timber fraction in walls, the insulative performance of a Code-minimum wall would appear to go backwards. Explaining why it isn’t actually a change is not a conversation anyone wants to have with the general public. The time to fix this is when wall performance is increased: the last change in 2007 was the perfect opportunity but it wasn’t taken.
The whole point of having an energy standard is to lower buildings’ real energy use in buildings. Buildings are big contributors to our carbon footprint—yet we already have the knowledge and means to remedy this. Instead at least in part because the Building Code Acceptable Solution tells the industry to use an oversimplified and inaccurate calculation for Code compliance, we’re misallocating resources at both the design and building stage.
The solution is building energy models based on accurate inputs. That’s how we get real energy savings. I’m hopeful that Building for Climate Change (BfCC) means all buildings will in future have to be energy modelled so their actual performance will be documented. BfCC is the opportunity to fix this long-standing fiction about timber fractions. About time, too.
Reference
Ryan, V., Penny, G., Cuming, J. (Part One only), Riley, M. (Part One only). (2021). Thermal Bridging in External Walls: Stage Two. Report Wall/4 by Beacon Pathway.A free download is available from BRANZ: www.branz.co.nz/pubs/research-reports/er53/
Disclaimer: The author carried out performance modelling for the FMI ZERO home, which uses a timber panel with CCSF insulation and optimised timber fraction. This article is his independent technical opinion.
[SIDEBAR]
H1/AS1 (5th ed) 2.1.4.3 (b) “For framed walls, the R-value shall include the effects of studs, dwangs, top plates and bottom plates, but may exclude the effects of lintels, sills, additional studs that support lintels and sills, and additional studs at corners and junctions;” [author’s emphasis]. Note that the wall area is defined as “the area of walls that are part of the thermal envelope, excluding the opaque door area and the glazing area.”