Heartland city Palmerston North now has its very first certified Passive House project, Hokowhitu Passivhaus. It’s notable for a highly-engaged homeowner, a skilled registered architect and a conscientious building team. None of them had prior experience with Passive House but they did choose a very experienced Passive House designer and altogether it went very smoothly. Read on to admire the optimisation of the timber fraction* in the 90-mm thick walls. We want to see more like this!
Passive House design for this project was in the capable hands of Elrond Burrell. We grilled him for some details. (Also see the project profile for data on the products used and U-values achieved etc.)
Sustainable Engineering Ltd (SELtd): You’ve told us the 90mm wall assembly was an aim from the outset, why was that?
Elrond Burrell: This was the first Passive House project for the architects and the builder so a 90mm timber framed wall meant one less novel aspect to the project. The second benefit was keeping the construction as close to typical as possible so it was easier and more accurate to first cost the job (it went out to tender) and then build it to budget. I should point out there is a 50mm insulated services cavity on the inside of the walls, so total wall insulation is 140mm.
SELtd: How did you approach it?
Elrond: We worked with 90mm framing in PHPP from the start so we could identify if the performance of any other components needed to increase. But as it turned out, other insulation values were not very different from our other projects:
- 300mm fibre insulation in the ceiling
- 250mm standard EPS under the concrete slab (it’s a raft slab—the continuous insulation is more energy efficient than waffle pods)
- the triple glazed windows with cedar frames are fairly typical performance for windows used on Passive House projects. The cedar frames are around 5% more thermally efficient than some aluminium-clad timber frames, so there was a little gain there. The glass is triple glazing from domestic supplier Metro.
SELtd: What were the factors in favour of 90mm wall framing?
Elrond: For a start, the climate in Palmerston North is relatively mild, so that helped [Ed. but it’s not balmy either: the mean daily minimum in winter months is -1.6°C!]. But efficient design was largely responsible and it helped in a number of ways. The architect, Mike Tate-Davis from E3 Architects, created a good compact design, with a form factor of 3.9. It has flat ceilings throughout. Yes, double height spaces and sloping ceilings are nice to have but they do impact on the efficiency by increasing overall internal volume and heat loss surface area. This is a modest project and the clients were happy with that trade-off.
Second, the house had a good orientation, wasn’t particularly impacted by shading and it wasn’t over-glazed, with a window-to-wall ratio of 16%. Lastly, the ventilation system was located next to the thermal envelope which meant short duct runs to the fresh air and exhaust air terminals.
While there were a number of factors in our favour, really it was Mike’s efficient design and clear detailing that made this wall assembly possible. He also put in a lot of effort to optimise the timber fraction in the walls. His careful documentation avoided additional timber in corners and other junctions and minimised dwangs. They were specified only when needed for fixing the plywood on the outside of the framing. My guess is that framing optimisation also saved money, but I don’t have any hard analysis that quantifies that.
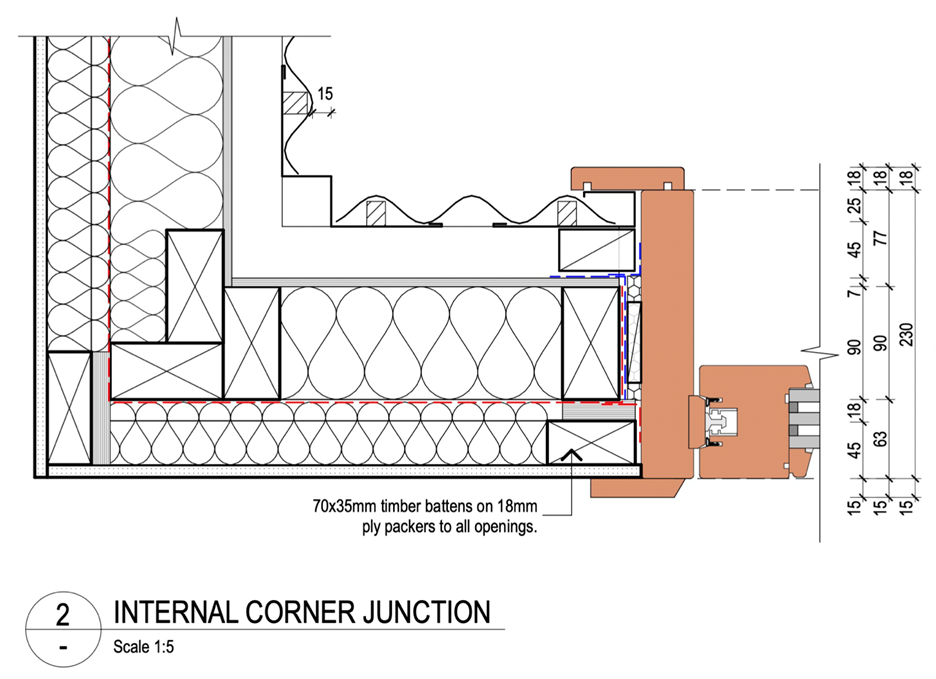
Examples of careful detailing: red line denotes the Pro Clima internal air barrier, blue line denotes the external weather barrier seal (Pro Clima Contega EXO) Details © 2024 E3 Architects
SELtd: Hit any snags?
Elrond: Well the 50mm insulation we specified went out of production. Most suppliers now offer a 45mm product that suits typical timber battens. We found a replacement, but there was some hunting around.
SELtd: Smart move on the client’s part to bring in a very experienced Passive House designer given it was the first rodeo for the builder too. How did they do?
Elrond: Sam Rosoman and his team from Optimum Build NZ brought a really good attitude to the project. I briefed the crew before they got underway on what was critical for achieving Passive House performance and their role in achieving it. They asked lots of questions (a good sign) and once underway they would come back for any clarification well ahead of when things were due to happen. They took advantage of Pro Clima’s training too. The team took a lot of pride in their work. The client was in regular touch with the builders, visited the site often and he schooled himself up about Passive House as well.
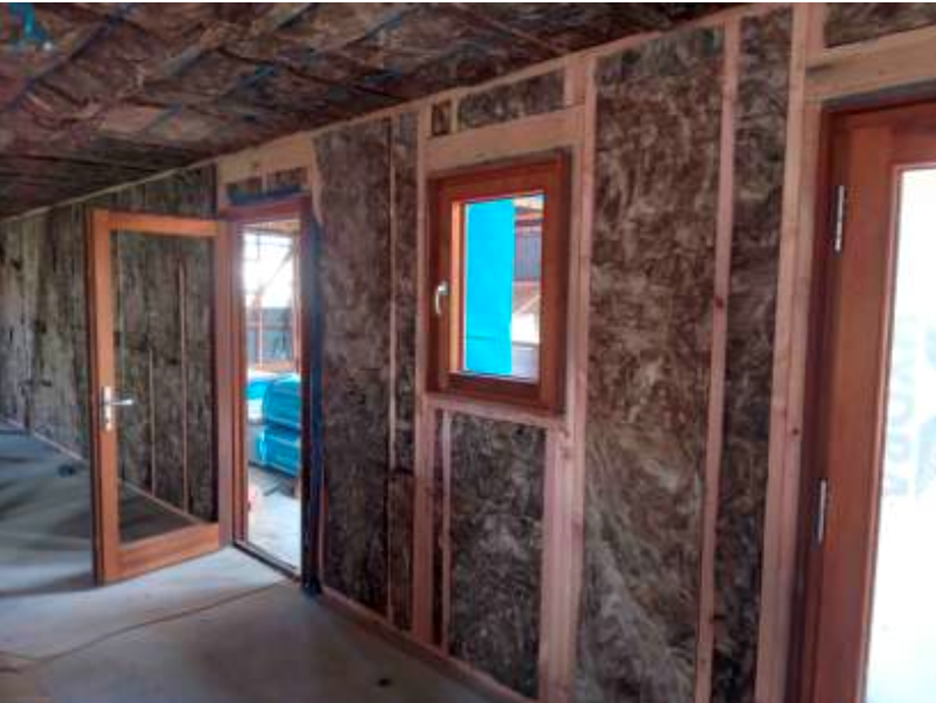
Very neat insulation installation, always great to see.
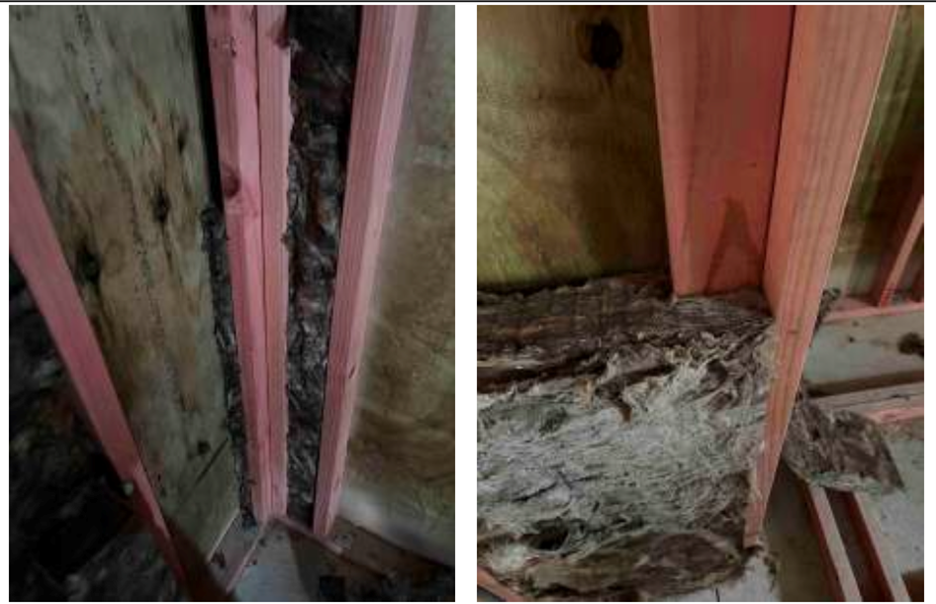
Insulation carefully cut around stud framing in order to achieve full depth insulation in corners.
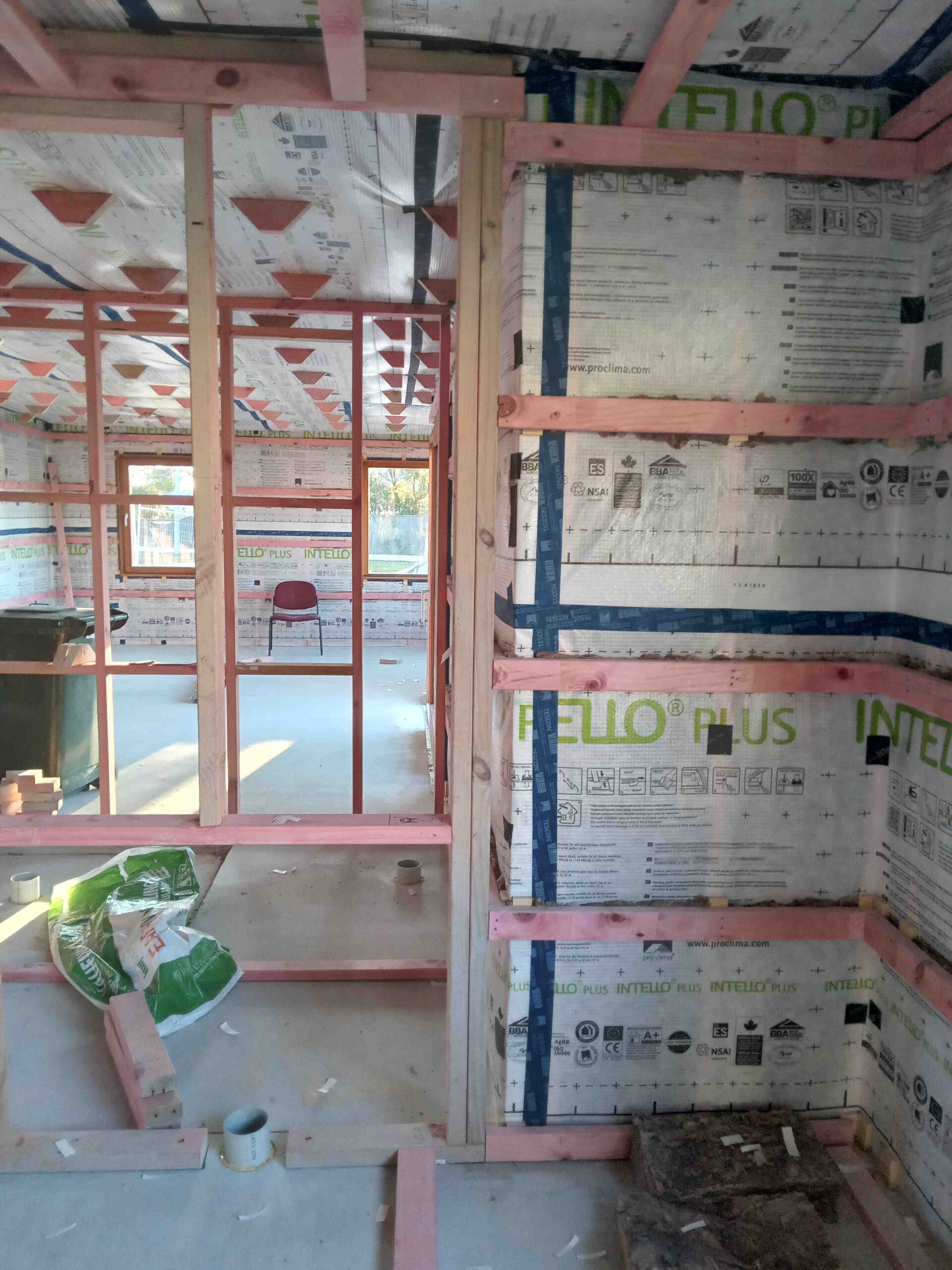
Intello on walls and ceiling has been taped. Wall battens installed for the service cavity and ceiling void blocking in place to accommodate ductwork etc.
*Jason Quinn has previously got technical about timber fractions in walls, why they matter and how inaccurate estimates are distorting the performance of Code-minimum buildings.