Carman Residence Queenstown
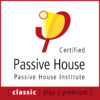
Project Team
Architecture Team Green Architects - teamgreenarchitects.co.nz
Passive House Design Sustainable Engineering Ltd – sustainableengineering.co.nz
Builder Fleck Construction Ltd - fleckconstruction.co.nz
Certifier Passive House Institute
Queenstown has some of the largest temperature ranges in Aotearoa so its buildings need to keep humans warm when it’s below zero outside and cool when it’s over 30 degrees. This ambitious home designed to shelter three generations succeeds beautifully. Its success rests on beautiful aesthetics and careful Passive House design.
The clients were attracted to their architect’s sustainability and performance credentials and wisely involved the design team very early. It was rewarding for the architects to be able to assess potential sites alongside their client and discuss the solar and thermal implications: some were stunning but facing the wrong direction. The chosen site is perfect. It lies between Queenstown and Arrowtown, looking north to Coronet Peak.
As is usual for projects on this scale, the ceilings are high and the brief involves large expanses of glazing and indoor/outdoor living. Carman Residence’s glazing boasts the highest level of thermal performance available and was imported from Germany via Ecowindows. It includes three metre high lift-slide doors on the northern elevation—at the time of specification there was no other option available in these dimensions.
Sustainable Engineering provided Passive House design services to this project and their experience ensured the design process was smooth and efficient. “The architect really understands Passive House design, so we were on the same page when working through details and examining trade offs,” Passive House designer Sara Wareing says.
Thermal bridges created by steel beams were easily broken by way of a HDPE block between cold steel and the column within the thermal envelope. Identifying this solution required three-dimensional thermal modelling, a specialist service carried out by other members of the Sustainable Engineering team. This expertise produced an accurate understanding of the thermal implications, enabling solutions to be precisely identified.
With big windows comes big solar gain. The architect is local and is well familiar with the pressing need to ensure summer comfort. She uses multiple strategies, starting with overhangs but here all windows are fitted with motorised external blinds connected to sensors. Rising internal temperatures trigger deployment of the blinds while a wind detector outside will prompt the blinds to retract to prevent damage.
The blinds and their associated equipment were provided by the window manufacturer and are installed on the window as a complete system. The chosen blinds are remarkably see-through, an important quality given no-one wants to diminish these views. The architect reports the effect is similar to that of a slightly darkened window tint. Nonetheless, the temperature change inside is immediately apparent when the blinds deploy. Specifying this strategy at the outset is important; the architect warns such systems are difficult to retrofit because motorisation requires electrical connections.
The house is large and the form appears complex, although some of the architectural flourishes lie outside the thermal envelope. Its volume helps it achieve heating/cooling requirements. It wasn’t initially intending to seek Passive House certification but it was being modelled in PHPP. The final design needed only a small increase in ceiling insulation to reach Passive House targets, an outcome the client was enthusiastic about.
The architect’s biggest challenge from a detailing perspective was the combination of a warm roof with a large overhang that provides vital protection from summer solar gain to the north while creating an important outdoor living area. One option would have been to connect the timber structure back to the wall insulation, which means the thermal envelope continues all the way around the edge of the overhang. To avoid making the geometry more complex, each rafter was insulated and fully sealed, which required more thermal modelling for certification purposes.
Clever choices at design stage directed the client’s budget to where it would be most effective, namely the ultra-high performance sliding doors. Elsewhere, repetitive window sizes were used plus the roof is a simple design. The single cladding material was cost-effective as well as practical in this environment and aesthetically well suited to the austere environment in which the building sits.
Passive House Metrics
- Heating Demand14.2 kWh/m2/year
- Heating Load13.2 W/m2
- TFA327.9m2
- Form Factor3.9
- Air leakage @ 50Pa0.6 ACH/hour
- PER demand32.4kWh/m2/year
Passive House Database - TBA
Construction Details Average Values
- U-value External Walls 0.21 W/(m2K)(R4.70)
- 140mm stud with R4.1 batts, Intello air control layer and 45mm insulated service cavity
- U-value Floor0.14W/(m2K)(R7.05)
- Slab on grade with 250mm EPS
- U-value Roof 0.09W/(m2K)(R10.61)
- Nuralite PIR warm roof with insulated ceiling service cavity
- U-value Glass0.70 W/(m2K)(R1.43)
- High performance triple glazing (4:/18/4/18/:4)
- U-Windows0.7 W/(m2K)(R1.5)
- ENERsign primus
- Ventilation Efficiency 83%
- Zehnder Q600

North Elevation

South Elevation
\
Find photos of finished construction (exterior and interior) on Team Green’s website.