Finch Residence Waikuku
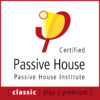
The Finch Residence will be very familiar to many readers as, under the Waikuku Beach Passive House moniker, its progress was meticulously documented on social media. Paul Finch is both its owner and mastermind. As an experienced project manager, Paul was supremely qualified and he was hands-on at every step of the way. The family’s goal was achieved: a modest, low-carbon, perfectly functioning home with the Passive House certification to prove it. Paul is also very proud of the tiny amount of waste generated by the build, a marked contrast to business-as-usual construction sites.
The owner involvement started with the floor plan. Paul and his wife began with what they liked (and didn’t) about the 1890s villa where they lived at the time and handed over a bullet point wishlist with a direction to fit it into a thermally efficient and affordable rectangle form. The draughtsman ably developed a full set of drawings according to the Finchs’ directions.
Some key material choices fundamentally shaped the project from the outset and were influenced from the years Paul has spent managing post-earthquake building projects. He’d come across the Surefoot footings on a project in Christchurch and was very impressed. The components and driven poles create a foundation that can be completely relevelled, with each pile able to be adjusted in all dimensions with just hand tools. It significantly contributed to a fast programme, with the house being built in just a year. Suspended floors are still a rarity among New Zealand Passive House builds but this project proves again that it’s a viable design strategy for a high-performance home—and that piles needn’t be treated posts.
Paul says he was completely focused on keeping Fletchers out of his life. That was achieved in part by specifying saveBOARD as a wall lining, a product new to the New Zealand market that can substitute for GIB-brand wallboard or plywood. Its availability meant Paul’s programme wasn’t impacted by the GIB supply crisis in 2023.
Paul managed the whole build through his consulting business. He appointed and managed subcontractors and ordered materials, including directly importing the windows from M-Sora in Slovenia, a company experienced in producing PHI-certified units. He made his decision after investigating joinery options from 10 different window suppliers around the world. They arrived on time, there were no difficulties and Paul is very pleased with the result.
The subfloor cassettes, internal and external walls are prefab timber panels supplied and installed by Ethos Homes, an experienced Passive House building company in Christchurch. These were very quickly stood up on site, contributing to the fast progress. So fast in fact, that the council’s building inspectors had trouble keeping up with the requests for inspections. Multiple milestones were sometimes reached on the same day.
Paul spent weekends meticulously taping every junction and penetration; when combined with the panelised construction and an efficient design, the outstanding blower door test result was no surprise. Having been so hands-on means he’ll be better equipped to monitor and guide contractors carrying out these tasks on future client builds, Paul observes.
While Passive House-level builds drive down operational carbon emissions to the bare minimum, Paul was also concerned with embodied carbon reduction. This was modelled by VIA architecture, who also suggested the home’s inclusion in the BRANZ HEEP2 study. The house is now fitted with extensive monitors and the data they collect will contribute to BRANZ’s research into how, when and why New Zealand households use energy in the home.
The findings aren’t visible to the Finchs during the 12-month project, but they don’t need the data to tell them how supremely comfortable their new home is. A 1kW reverse-cycle heat pump was installed for cooling when necessary but it’s only been turned on once and that was to check it worked. Modest amounts of night ventilation are effectively moderating summer spikes in temperature. Heating would be provided by two heated towel rails, but so far people and plug load have been enough to keep toasty inside when temperatures plunge outside.
Project Team
Architecture Construct Drafting Services Ltd - constructdrafting.co.nz
Passive House Design VIA architecture Ltd - via-architecture.net
Main Contractor Finbo Ltd. - finbo.org
Builder Ethos Homes Ltd. - ethoshomes.co.nz
Mechanical Engineer - Dynamic Air and Electrical Ltd - dynamicair.co.nz
Certifier Sustainable Engineering Ltd – sustainableengineering.co.nz
Passive House Metrics
- Heating Demand12.3 kWh/m2/year
- Heating Load9.6 W/m2
- TFA136.8m2
- Form Factor3.5
- Air leakage @ 50Pa0.2 ACH/hour
- PER demand26.7kWh/m2/year
Passive House Database - 7402
Construction Details Average Values
- U-value External Walls 0.21 W/(m2K)(R4.81)
- Cladding / EcoPly / 140 Timber Wall with fibre Insulation / Intello / 45mm Service cavity with fibreInsulation / Saveboard
- U-value Floor0.18W/(m2K)(R5.55)
- Timber Floor on Surefoot Piles / 240mm Joists with fibre insulation / Strandboard / Flooring
- U-value Roof 0.13W/(m2K)(R7.79)
- Truss Roof with 300mm fibre insulation / intello / service cavity / Saveboard
- U-value Glass0.53 W/(m2K)(R1.89)
- Saint-Gobain - Ertl Glas Steklo Triple Glazing
- U-Windows1.0 W/(m2K)(R1.0)
- M-Sora Comfort Optimo XLS
- Ventilation Efficiency 78%
- Stiebel Eltron GmbH & Co. KG - LWZ 280 Balance