Luggate Memorial Centre – Whare Mahana Wanaka
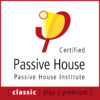
Luggate’s new $5.56m community hall has been certified to the Passive House standard, the first community facility in Aotearoa to do so. It’s a notable achievement but its significance goes far beyond this milestone. Multiple challenges had to be overcome at design and construction stages. (See also this blog post, discussing insights into the process from the design team.)
The challenges, in brief
The Queenstown Lakes District Council provided a usefully descriptive yet intimidating brief. An integrated commercial kitchen was mandatory, despite this never having been done in a New Zealand Passive House project before. A hugely variable occupancy rate went with the territory of a well-used community gathering place. Together, these two things demanded careful and necessarily complex mechanical engineering.
But that’s not all. The original hall (pictured here) was built in 1954 and was much loved by its community. In particular, it had wonderful acoustic properties and locals wanted this to be a feature of the new hall too. Acoustic engineering analysis dictated a minimum height to width ratio, which created a very large internal air volume. This added further complexity to the ventilation requirements.
Further, there was a specification change after design work had started, requiring the use of prefabricated components.
Other challenges were not unique to this project but nevertheless added to the complexity. Councils are by definition cost-sensitive clients so the budget was tight. Covid wreaked various degrees of havoc on every build underway during 2020-22 and this project was not spared. Lastly, the windows originally specified were very high-performance. When the manufacturer went under, the replacement windows available couldn’t match the original specifications. This also affected the completion date.
The solutions, in detail
The design team’s first response to the budget pressure was to make the form factor as simple as possible but still elements of the design were pruned away as the project progressed. The architect successfully made the case for retaining the entrance canopy and the external shutters.
The shutters play a vital functional role because the temperature range is wide here, between seasons and within a single day. The shutters are key to reducing the cooling load and are closed for the warmest half of the year. (This can be changed by people hiring the hall, but they must be returned to the default position at the end of the hire period.) The hottest days will also coincide with times of peak occupancy, creating some worst case scenarios that the energy modelling needed to take into account.
However, it was heating demand that proved the critical metric for this build. Getting under the line here was difficult because of the internal air volume, coupled with fluctuating occupancy. The commercial kitchen required extract ventilation, tricky in a Passive House airtight envelope, and needing make-up air. Fire regulations demanded the kitchen have its own dedicated ventilation system; it couldn’t share the MVHR ductwork. The combined effect of ventilation and infiltration losses hammered the heating demand, already under pressure because of the change to the window performance. Plus the locally built prefabricated panels, although offering many benefits, by their nature double up studs at every panel junction, increasing thermal bridging.
The heating demand allowance shaped mechanical engineering decisions too. Make-up air for the kitchen extraction ventilation had to be thermally tempered so it didn’t impact on thermal comfort. A heat exchanger is the first response, boosted when needed by a duct mounted heating coil. This is refrigerant-based, the most energy-efficient option.
The HVAC system was designed to operate under two distinct occupancy scenarios. The most frequent use of the hall involves groups of up to 40 people but sometimes there will be over two hundred guests. This required two parallel ventilation systems, as a single system could not cover both scenarios. The first system runs ventilation in background mode, while heating is provided by high-level radiant panel heaters powered by an air source heat pump. When the hall is full of people, a central HVAC system kicks in to deliver heating or air conditioning and ventilation. Shifting between systems is as simple as flicking a switch.
However the biggest challenge for mechanical engineering was fitting all the plant required into the building’s compact footprint. The commercial kitchen shares a wall with the plant room, which minimised the duct runs.
The design team reduced the impact of commercial kitchen ventilation while also improving functionality for hall users. A bar was anyway required and so this space was made dual-purpose by including a simple domestic-style kitchen for making hot drinks and reheating and serving food.
Extremely high levels of insulation was the key compensatory mechanism for meeting heating demand requirements. The walls, constructed with woodfibre board and OSB, have 190mm of insulation plus an insulated service cavity while the floor features 350/380mm of expanded polystyrene under the slab. As for the roof: is this the most highly insulated roof space in New Zealand? The U-value is 0.08 (R 11.86)!
And then, Covid. Construction began in July 2021 and that very tricky virus threw many a spanner in the works. Many design variations were required at very short notice. For instance, the prefab panel manufacturer needed timber I-beams for the roof panels, but Auckland was locked down and the I-beams were stuck there. Engineers stepped in to design a bespoke box beam as a replacement. There were many incredible moments of just having to respond to whatever was coming at them, recalls the Passive House designer.
This was always going to be a project subject to extreme levels of scrutiny. The original hall was much loved by its community, despite being freezing cold with tiny windows. There was a great deal of sadness when in 2017 it was discovered to be extremely earthquake prone, leading to the decision to demolish it, salvaging as much as practical.
And yet here in its place, is a new building, envisaged, designed and created by locals, which the community has embraced. The hall’s te reo name, Whare Mahana, was gifted by Kāi Tahu. Its meaning, “warm house”, can be appreciated on several levels.
Project Team
Architecture Salmond Architecture - salmondarchitecture.co.nz
Mechanical Engineer WSP Ltd - wsp.com/en-nz
Passive House Design Hiberna Ltd - hiberna.co.nz
Builder Breen Construction - breen.co.nz
Certifier Sustainable Engineering Ltd – sustainableengineering.co.nz
Passive House Metrics
- Heating Demand10.8 kWh/m2/year
- Heating Load10.5 W/m2
- TFA364.2m2
- Form Factor3.7
- Air leakage @ 50Pa0.5 ACH/hour
- PER demand55.4kWh/m2/year
Passive House Database - TBA
Construction Details Average Values
- U-value External Walls0.15 W/(m2K)(R6.7)
- 35mm woodfibre board / 190mm insulated timber wall / OSB / 45mm insulated service cavity
- U-value Floor0.10W/(m2K)(R10.3)
- 100mm concrete slab / 330mm continuous VH grade EPS
- U-value Roof 0.08W/(m2K)(R11.9)
- 100mm concrete slab / 330mm continuous VH grade EPS
- U-value Glass0.55 W/(m2K)(R1.8)
- Neuffer Planitherm XN Triple Glazing
- U-Windows 0.9 W/m2K)(R1.1)
- Neuffer EcoIdeal
- Ventilation Efficiency71%
- Swegon - GOLD RX 20 and Swegon Gold LP13