Till Cottage Kaiwaka
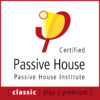
Project Team
Architecture & Passive House Design Energy Architecture NZ Ltd - energyarchitecture.nz
Structural Engineering Groove Design
Builder Till Schlimme
Certifier Sustainable Engineering Ltd – sustainableengineering.co.nz
This small Passive House north of Auckland is unassuming at first glance but is in fact a project of enormous significance. It is a retrofit, which is unusual enough, but it succeeds in reaching the full Passive House level of performance rather than the more flexible EnerPHit standard for retrofits.
The Passive House designer is proud of the fact that the before and after photos of the project are so similar. Till Cottage is definitely a retrofit focused on robust thermal improvements to a good design. That stands in contrast to a wholesale renovation where often so little of the original structure is retained or unaffected that the project may as well have started from scratch.
The cottage was built about 15 years ago and stands in a peaceful eco-village on Kaipara Harbour. It was a well-intentioned build, with better-than-Code levels of insulation and double-glazed windows and built with attractive natural materials like earth plaster and cypress cladding. However thermal performance was poor due to aluminium window frames without thermal breaks and high timber fractions in walls. The current owner moved in five years ago and immediately noticed how draughty the house was. It also overheated badly in summer, while winters were cold and damp. A lack of ventilation saw mould in the bathroom despite a cast iron wood-burning stove running hot.
But there was a lot to love about the layout, outlook and aspect. Its owner is a master cabinetmaker with deep experience in restoring historic buildings in Europe, including using modern, technical materials like airtight membranes and tapes. So he knew far better performance and comfort was possible. This was confirmed by Sustainable Engineering’s Jason Quinn, who offered initial advice.
The project took a European deep retrofit approach, affecting changes to airtightness, insulation and mitigation of thermal bridging from the exterior. This meant the owner could keep living in the house throughout the patient renovation and also ruled out any weathertightness or condensation issues being introduced. The wall build up was increased by 125mm, consisting of insulation and cavity battens. High-performance windows made in New Zealand were carefully positioned and fitted.
The project is noteworthy for the care and attention to detail (detailing around critical junctions was exceptionally well done) and a commitment to reusing existing materials. The owner carefully removed the board and batten exterior cladding that had been nailed directly to the nogs. The Lawson cypress had weathered but was in good condition. The odd board that split or was otherwise damaged was painstakingly glued and eventually refixed.
Wood fibre insulation board was used over specialist retrofit airtight membranes. This was a novel assembly and Sustainable Engineering carried out hygrothermal modelling to test how the materials would interact. Wood fibre is an uncommon insulation choice in New Zealand but expect this to change rapidly in the next couple of years as large mainstream players start specifying it in their own developments. It has worked very well here, used in both the ceiling and walls. The existing concrete slab lacked edge insulation, so this was remedied.
Making room for ventilation ducting is a big challenge in any retrofit. It didn’t cause headaches here. The location of the MVHR unit was changed once it arrived on site, as it fits perfectly at the back of a long walk-in pantry. The home’s simple open plan layout simplified the duct runs, which were routed from the pantry through kitchen cupboards and built-in wardrobes. The duct run in the main bedroom is still exposed, at least for now. Ductwork is also visible in the winter garden, a conservatory created to bring the new flushing toilet inside the house’s thermal envelope. This is connected to a vermicast-based black- and greywater system, replacing a long drop toilet a few steps outside the back door.
The owner was determined to enjoy the view into the garden from generous west-facing windows in the main bedroom. Overheating concerns were allayed in part by the shade from mature trees nearby (emphasising the importance of site specific energy modelling). External shutters have been very recently installed and the owner expects even greater comfort during next summer’s temperature extremes.
His favourite thing about the new version of his house is how warm and inviting it is. He spends a lot of time working outside on the land. He also feels the cold (“thin-skinned”, he jokes) and it’s an everyday pleasure right now to come from crisp autumn temperatures outside into a cosy house which is warm everywhere.
As for seeking certification, the owner appreciated having a measurable goal to work toward, rather than an outcome that was only assumed. He appreciated the rigour of the modelling done at design stage and liked the feedback from the blower door tests, which helped him identify tiny leaks in the thermal envelope that he could remedy. He also appreciates that the clearly defined Passive House standard has been proven in practice for decades and believes certification will add value and appeal in the future when it is time to sell the house. “If more people would know what is possible with regard to achieving a good, nice, healthy living environment, I think more people would opt for these things,” he reflects.
As for that woodstove and its wetback, it has been reused too. There is no need for it here (hot water is provided via a solar panel, topped up by a heat pump hot water system) so the woodstove is providing service in another home in the community, at least for now. Perhaps neighbours’ experience of visiting Till’s Cottage will encourage more retrofit activity in this village.
Passive House Metrics
- Heating Demand15.9 kWh/m2/year
- Heating Load9.9 W/m2
- TFA90.6m2
- Form Factor3.9
- Air leakage @ 50Pa0.6 ACH/hour
- PER demand48.9kWh/m2/year
Passive House Database - 7186
Construction Details Average Values
- U-value External Walls0.21 W/(m2K)(R4.7)
- 80mm Gutex Woodfibre insulation / 140mm Timber framed wall insulated with Terralana / GIB
- U-value Floor2.65W/(m2K)(R0.38)
- Existing concrete slab with Cupolex pods and new concrete slab with 200mm continuous EPS all externally insulated with a vertical wing of edge insulation
- U-value Roof 0.14W/(m2K)(R7.1)
- 80mm Gutex Woodfibre insulation / 225mm Terralana in skillion roof / sarking
- U-value Glass1.14 W/(m2K)(R0.88)
- Thermadura Low E argon double glazing 4-18-4
- U-Windows1.4 W/(m2K)(R0.7)
- Thermadura Designline 78 series
- Ventilation Efficiency 81%
- LWZ 180 (Balance)
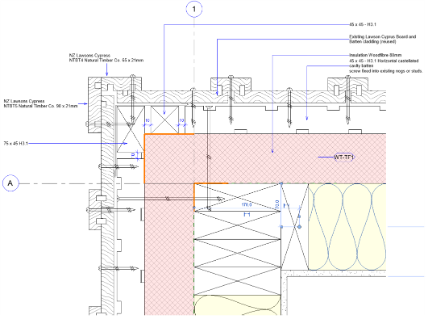
Wall construction detail
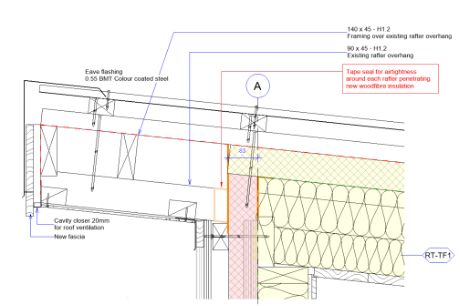
Roof construction detail
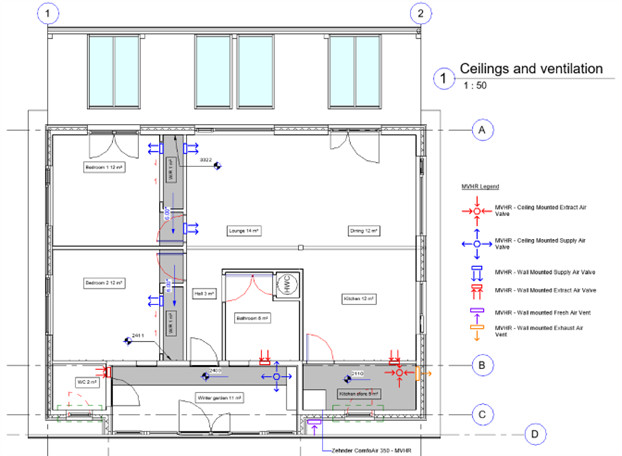
All drawings © 2023 Energy Architecture
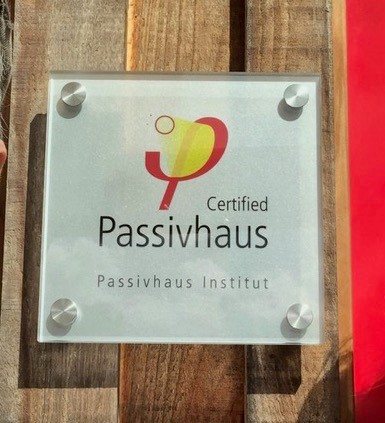
In a thoughtful gesture acknowledging the owner’s country of birth, Sustainable Engineering organised a special “Passivhaus” version of the PHI certification plaque.