PIHA EnerPHit Piha
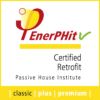
Project Team
Architecture Sang Architects – sangarchitects.com
Mechanical Design Edge Innovation Ltd - edgeinnovation.co.nz
Passive House Design Sustainable Engineering Ltd – sustainableengineering.co.nz
Builder Bruyere Ltd
Certifier PHI Darmstadt Germany – passivehouse.com
This is New Zealand’s first enerPHit project to be certified. This astonishingly ambitious retrofit stripped a large, luxury house built in 2008 back to its shell and rebuilt it to achieve certifiable performance. The result is a testament to the owner’s commitment and the skilled team of professionals that brought the project to fruition over a three year period.
There are two pathways to EnerPHit certification and this project achieved it via the component method. One notable exception required approval and this was obtained from the certifier at the outset of the Passive House design. Due to the structure of the two-storey building, insulation could not be applied above the ground floor slab. Instead, an external insulation skirt was fitted—a solution not without its complications when retrofitted to an existing building. This acted as slab-edge insulation plus the insulation was extended up to 600 mm down into the ground to reduce heat loss. Keeping the edge of the slab warmer prevents the risk of mould developing.
Minimizing the significant thermal bridges of the original design required painstaking modelling and analysis. Among the challenges was a concrete midfloor that ran right out of the building to form the deck, with occupied space below. A height difference needed to be retained in order to keep rainwater out. This required insulation to be fitted to the underside of the concrete deck, which didn’t line up easily at the deck/wall junction as the walls were insulated to the exterior. This thermal bridge was calculated and modelled until a workable option was identified (see image below).
Despite being a comparatively modern build, mould was discovered when the insulation was removed from the ceiling cavity. The original roof was a cold timber membrane construction with fibre insulation and the presence of mould was predicted when the Passive House designer reviewed the original construction design. This greatly concerned the owner and helped spur the decision to proceed with a certifiable retrofit. Once stripped back to the shell, all existing roof timber was sealed in epoxy paint, the best practice for encapsulating mould. A warm roof was installed to prevent the cold/moist issues common with cold timber membrane roofs.
The airtightness result is a credit to the builder’s skill and care. At just under 1.0 ACH at 50Pa, this compares favourably to the 0.6 ACH limit for a certified Passive House. Airtightness was the biggest technical challenge the team encountered during construction. The leakiness of a direct extract kitchen rangehood and the sealed combustion exterior air fireplace together account for a significant fraction of this result.
Concrete walls, slab and midfloor create a building with very heavy thermal mass, which helps keep the temperature stable. Despite this, active cooling was necessary and several concealed individual mini-split reverse-cycle air-conditioning units were installed. Passive House designer Jason Quinn employed every option to reduce summer overheating, including exterior shading and special glazing (low g-value or low SHGC) that reduces solar heat gain. But due to the massive glazed areas looking west over spectacular ocean views, active cooling was nevertheless required. While operable windows help with cooling through cross-ventilation, throwing windows open in mosquito season isn’t appealing.
The owner was delighted with how the house felt after its rebuild. For reasons unrelated to its performance, it was sold this year. The price was not disclosed but there was speculation in the real estate press that it would sell for more than six million dollars, setting a new record for Piha. Its new owners take possession in June and will no doubt be delighted to discover the warmth and comfort the house offers even in the middle of a damp and cold west coast winter.
Passive House Metrics
- Heating Demand27.1kWh/m2/year
- Heating Load17.0W/m22
- Frequency of Overheating 0.0%
- TFA220.6m22
- Form Factor3.7
- Air leakage @ 50Pa1.0ACH/hour
- PER demand59.8kWh/m22/year
Passive House Database - 6185
Construction Details Average Values
- U-value External Walls 0.26 W/(m2K)(R3.8)
- STO THERM+ (100mm of graphite infused EPS outside the concrete block)
- U-value Floor4.58 W/(m2K)(R 0.2)
- Uninsulated slab-on-ground with edge insulation retrofitted. New slab section insulated 50mm XPS.
- U-value Roof 0.16 W/(m2K)(R6.4)
- Nuralite warm roof 170mm of PIR on timber deck. Ceilings to decks insulated internally with 80mm Kingspan Kooltherm K10 board
- U-value Glass1.05 W/(m2K)(R1.0)
- GlassTeamAKL Cool-Lite SKN176 (4:/16/4 90% Ar)
- U-Windows1.1 W/(m2K)(R0.9)
- SmartWin (SEDA)
- Ventilation Efficiency 75%
- Wolf - CWL - 400 Excellent
Photo credits:
Finished building and floorplan used with permission of the client
Construction photos used with permission of Sang Architects