Watterson Residence Featherston
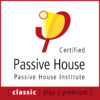
The Watterson residence is already famous, being that Passive House build in Featherston that featured on Grand Designs in November 2022. The home is an outstanding example of meticulous planning and through project management, easily hitting all Passive House metrics with plenty of margin. It also notably proved that this level of performance is possible on an average budget—and without sacrificing functionality or aesthetics.
This home is the first Passive House project for the architect and Passive House designer and the builder. It was also documented for a TV series that gently but resolutely looks for drama. A bit of pressure, then?
In what may have been a problem for Grand Designs producers, there was no drama on this building site. The Passive House design was approached in an exemplary way, very logical and structured, according to certifier Jason Quinn.
The designer sought advice from the Sustainable Engineering certification team early on about the windows she wanted to specify, which performed well but weren’t Passive House certified. She had her design peer-reviewed and then went through a pre-submission review with the certifier. This gave her confidence to add skylights to the design and conservative values were used to avoid the need for extensive energy modelling. (The TV show was incorrect to suggest the skylights were only added after construction began.)
Notably, the pre-construction review was carried out before construction began: best practice but far from universal. Windows were ordered immediately the project cleared the pre-construction review, before the project was consented. This was a small and carefully managed risk with considerable upside, as it meant windows could be sourced from overseas before prices rose, and were available on site right on schedule.
The certifier also notes it may be easier to manage costs when the same person is doing architectural and energy design. This proved important in this case when the budget was put under pressure by banks changing lending criteria once the project had already begun.
This logical, methodical approach extended to appointing and managing contractors. A handful of local contractors were considered but a tender process wasn’t an option given the demand for tradespeople at that time. Instead, the builder was selected on the basis of their experience in installing airtight membranes and blower door testing a previous project—and because they offered a clear strategy on pricing and were willing to sign up to an open book contract.
The owner and designer managed the subtrades (with support from the main contractor around managing invoices). She ensured all subtrades were very clear about their responsibilities with regard to airtightness. A note in the drawings specified that approval was needed before any penetrations were made. She briefed each subtrade on site and they decided together, before work began, on exactly where each penetration would go and how it would be sealed.
Here the scrutiny of being on camera worked in the project’s favour, as no-one wanted to be the guy responsible for the home failing its blower door test. In the end, everyone involved got to celebrate an outstanding preliminary blower door test, which was captured on film. It improved even further, from 0.3 to 0.2 air changes per hour, when the A test was done at project completion.
Using SIP construction would have assisted this result but again, so did meticulous preparation. The designer says she approached the drawings just as she’d been taught in her Passive House designer training, for example lots of cross sections and colour coded drawings for ease of reference for tradespeople. She also used a technique the certifier recommends, tracing a pencil line around the perimeter of the drawing, a mechanical check that the airtight layer is continuous.
The project benefited from being designed with margin on the basis on 0.6ACH. For instance, heating demand was 13.5kWh/m2/year at 0.6ACH, enough to avoid having to energy model every component. When the airtightness result was so much better, the heating demand and load figures dropped even further [see Passive House metrics, below].
This was a textbook approach that is all the more impressive for being the designer’s first Passive House project. It is extra sweet when it is her own family benefitting from her professional accomplishments. The family of four are loving living in their new home and say the space is being put to good use. Both adults work from home and they also host community children’s classes. Will it feel too big when the kids grow up and move out? The cost of housing makes their mother muse they may never leave home.
Somewhat recovered now from the months of hands-on building work she also contributed at the end of the build, Josefine is looking forward to providing Passive House design for other people’s new homes in the future. She’ll do this through her own business Thrive Architecture, while continuing to work on commercial developments in her part-time role with a major architectural firm.
Project Team
Architecture & Passive House Design Josefine Watterson - thrivearchitecture.co.nz
Builder Maple Build Ltd - maplebuild.co.nz
Certifier Sustainable Engineering Ltd – sustainableengineering.co.nz
Passive House Metrics
- Heating Demand12.2 kWh/m2/year
- Heating Load12.9 W/m2
- TFA177.3m2
- Form Factor3.6
- Air leakage @ 50Pa0.2 ACH/hour
- PER demand37.0kWh/m2/year
Passive House Database - TBA
Construction Details Average Values
- U-value External Walls 0.22 W/(m2K)(R4.6)
- 140mm insulated Timber Wall / Intello / 45mm insulated service cavity / plasterboard
- U-value Floor0.19W/(m2K)(R5.1)
- 100mm Concrete Slab / 200mm EPS insulation
- U-value Roof 0.13W/(m2K)(R7.6)
- Skillion Roof with 190 or 240 Timber Joists / Intello / 90mm Insulated service cavity / Plasterboard
- U-value Glass0.64 W/(m2K)(R1.7)
- Neuffer Triple Glazing
- U-Windows1.0 W/(m2K)(R1.0)
- Neuffer IDEALU 78 - Timber Aluminium Clad
- Ventilation Efficiency 87%
- ComfoAir Q350 HRV, Comfort Vent Q350