A construction detail can be widely used and have been in use for a long time and yet still be a bad idea. This month, we’ll look at some common details that we’d prefer to see consigned to history, plus outline some better alternatives.
Our team sees scores and scores of high-performance projects each year. There are all the Passive House buildings we certify, as well as those where we carry out the Passive House design, plus many high-performance new builds, remediations and renovations that we consult on. It gives us a particularly broad perspective about what’s working and what isn’t.
When we see risky details in a project we are certifying, we will raise this at the pre-construction review. But unfortunately, it’s not uncommon for the build to be underway by the time the documentation is provided to us. Then we’re into remediation territory. Where Sustainable Engineering has been engaged to consult on a project, such as providing Initial or Detailed Design Services, there’s more time to fix things on paper. That’s always a better outcome. Cheaper, too.
Risky business
I want to single out some details that introduce significant risk from moisture build-up. Just because a detail worked in the past or everybody uses it, doesn’t mean it’s not causing problems now. New buildings have more insulation and are often poorly ventilated. These combine to create more risk of damage from moisture buildup in the building structure.
The second point is that the risk of a particular detail also depends on the pattern of occupancy. Relevant factors are occupant density, degree of heating, climate and the extent and consistency of ventilation. Aside from climate, affluence by-and-large functions as a proxy for risk. Two people living in a big, big house in Queenstown that has continuous mechanical ventilation and central heating? Low risk scenario. A two-bedroom unit in muggy Auckland with multiple people sharing each bedroom, no budget for heating and windows tightly closed for security and privacy is at the other end of the risk scale. That’s when architects really need to focus on bulletproof assemblies and details.
Here are some familiar details that use common materials, but which we say are best avoided in a modern context. They create problems by shifting the dew point further inside a wall or roof assembly. When moisture or high humidity is trapped against the building structure, it will very likely produce mould and possibly lead to rot or corrosion.
Public enemy #1: Steel penetrations
Steel solves so many structural problems but its use is the cardinal sin when it comes to high-performance building problems. (It’s also problematic in terms of embodied carbon.) It’s a difficult material from the point of view of heat losses and moisture.
The best solution is to design using other structural elements, like laminated timber. Or, design in such a way that the steel is all warm or all cold—that is, either totally outside or inside the building’s thermal envelope. Passive House designers are used to thinking about thermal bridges in terms of heat loss problems, but that is not the end of it.
Take a look at the viper’s nest uncovered during a renovation in Wellington on which Energy Architecture consulted. This architecturally-designed 1990s home on a hillside had a spiderweb of steel breaching the thermal envelope, compounding the problems caused by direct-fix cladding. The high humidity levels in the timber next to the steel (below) had significant structural impact, as shown in the before-and-after photos below. Alarmingly, this steel runs through an external wall to support a balcony.
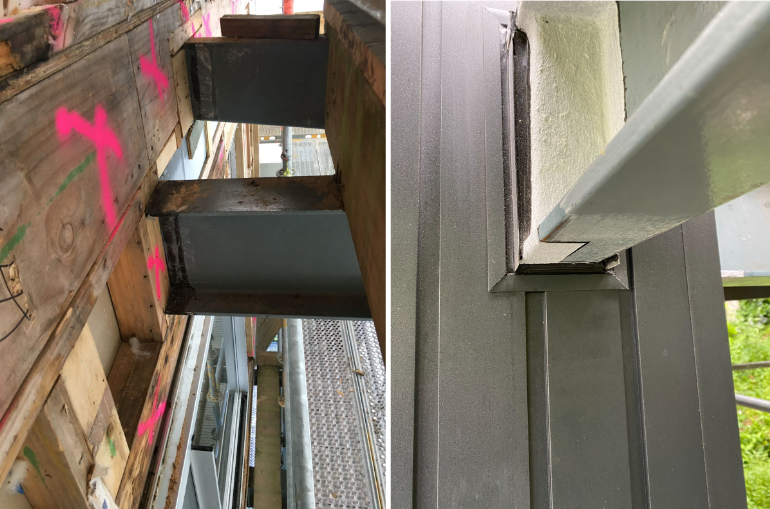
Photos by Energy Architecture, used with permission.
In the photo above (left) Xs mark degraded timber that needed to be replaced. To the right, is the solution, with additional external insulation, vented cavity cladding and proper flashings. We wouldn’t expect to see this detail in a new build but it works and was a good choice in the context of this tricky retrofit.
In terms of how the building was used, this was a low-risk scenario (thankfully—it could have been much worse). It’s in a cooler climate compared to Auckland plus Wellington winds boost uncontrolled ventilation rates. Just two people live in this big house, which was heated during the cold months.
Lesson to learn: don’t design steel that penetrates the thermal envelope. Or at least, minimise it and ensure those thermal bridges are broken.
Public enemy #2: Concrete + internal fibre insulation
Concrete lined with fibre insulation on the interior side is a bad combination. This type of insulation is open to moisture; it passes right through the fibre only to hit the concrete surface. High relative humidity develops. Concrete doesn’t mould as readily as timber because it’s so alkaline, but it can still happen—especially when the perfect environment has been created.
New Zealand’s first certified EnerPHit project in Piha, West Auckland is a good example of what can go wrong. Context: Situated in the more humid Auckland climate makes it higher risk, but that ameliorated by being a large house with a lot of uncontrolled ventilation (all those louvre windows!) and low occupancy, that was heated adequately.
The owner initially came to Sustainable Engineering for some consulting advice. The luxury house with jaw-dropping views over Lion Rock was only 11 years old when our team reviewed the original drawings. We correctly predicted there would be mould behind the bedroom ceilings. This very unwelcome discovery was crucial to the client’s decision to go all the way with a deep retrofit for energy efficiency and health.
The problem started with a concrete midfloor that ran right out of the building to form the deck, with bedrooms occupying the space below. Just like the steel in the Wellington example above, the concrete was a big fat thermal bridge that got very cold and caused humidity on the internal surface to rise.
This was particularly challenging to fix. The best solution would be to install external insulation, creating a warm roof, but there wasn’t enough space to permit this. Instead, internal vapour-tight insulation was fitted instead.
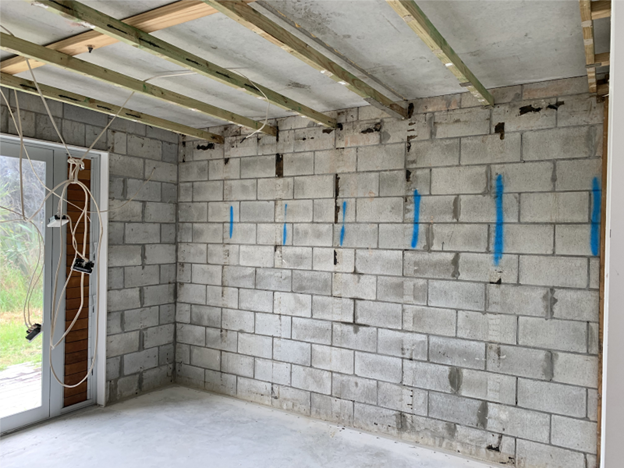
The mould produced on the ceiling underneath the deck.
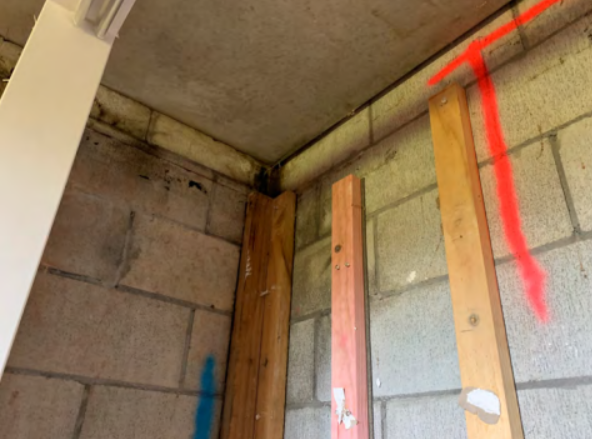
Moisture and mould on the north wall of a bedroom.
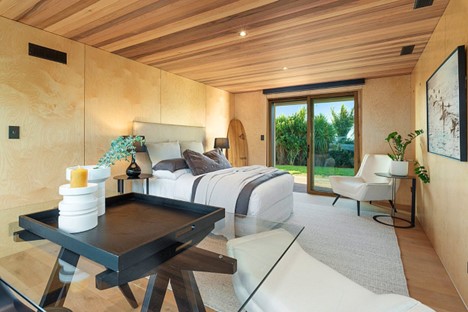
The “after” photo: an unrecognisable bedroom with mould successfully remediated.
Concrete block walls lined internally with fibre insulation—which also featured in the Piha build—is a detail that I’d like to never see again in a new construction. Typically it will be faced with plasterboard, in which holes are made for services. This combination of batt and plasterboard quite effectively stops heat—but allows water vapour to move through readily, creating the same risk conditions for mould as we saw above.
As for solving this, there are multiple alternatives and the best one will depend on the specifics of the project and the performance standard required.
Public enemy #3 Cold membrane roof
Despite a long history of failures, we still see cold membrane roofs show up on drawings. They are a common solution for a low roof pitch. The membrane is typically applied above a plywood layer, which is then insulated below with fibre insulation. This construction has failed so many times in school buildings that the Ministry of Education guidelines for new construction will not permit it.
Instead, we need warm roofs, where the insulation is installed above the plywood, keeping the plywood and associated structure warm. The original design of the Piha home included a cold membrane roof and just as we expected, the timber studs were found to be lined with white mould (below).

Photos by Sang Architects, used with permission.
A final thought to ponder
New Zealand has horribly low expectations of building lifespans, enshrined in our Building Code. Yet buildings take a lot of time, money and resources. There’s also a lot of embodied carbon sunk into their construction and eventual demolition. Building to the Passive House standard ensures better quality and durability of the building envelope and that is a really good thing.
Lesser quality buildings that take much more energy to heat are faced with an unpleasant conundrum. Thermal bridges or other constructions that bleed heat can actually reduce the risk of damage from moisture. Often the more heat pumped into a detail, the better it can dry out. It’s not good practice and it flies in the face of everything this practice recommends with regard to energy efficiency. But occasionally it might be the only practical solution when a full-blown retrofit isn’t possible.
New Zealanders only think about heating in terms of human comfort (and increasingly health), but a warm dry home is also good for the health of the building! Should ensuring long-term building durability trump low operational energy demand?