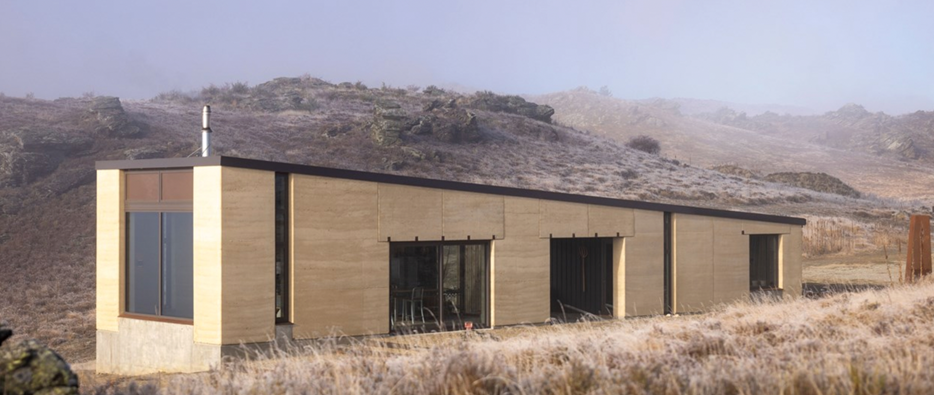
Ophir House by C Nott Architects Ltd. Credit: NZIA
The improvements introduced in 2023 to the H1 Energy Efficiency requirements of the New Zealand Building Code have implications for those wishing to build their homes from some natural building materials, in particular rammed earth. Rammed earth has featured in some high-profile architectural builds in recent years, like the NZIA 2023 award winner in Otago pictured above.
Rammed earth has very high thermal mass, but that must not be confused with thermal insulation. Jessica Eyers is very well-placed to explain this distinction and what H1 means for specifying natural building materials. She has designed multiple strawbale and natural plaster homes that have achieved or are on track for Passive House certification. She’s a former architectural designer now consulting at Sustainable Engineering. Jessica authored an in-depth paper for EBANZ on this topic recently, which we summarise in part below.
“Requiring better insulation is a good thing and there’s no basis in fact for thinking traditional thermally massive building materials should be exempt,” writes Jessica. “More insulation means it is easier to keep indoor temperatures within an acceptable range—increasingly there’s an issue with avoiding summer overheating, it’s not just about staying warm in winter. It’s about comfort but also human health and climate health.
“Traditional earth building materials are all, to some extent or another, thermally massive. The more dense a particular material, the higher its specific heat capacity, the technical term for measuring thermal mass. Thermal mass in walls and floors acts like a battery, absorbing heat and releasing it as the air temperature drops (the opposite is true in summer). This is a core tenet of passive solar design.
“But it does not follow that a thermally massive building element is a good thermal insulator. Thermal mass tracks density and there’s an inverse relationship between density and insulation performance. Rammed earth is the densest of the traditional building materials, which is why it is falling short of the new insulation requirements. Lighter materials, like strawbale or LEM [Light Earth Method, a mixture of fibre and clay], are able to comply. Their lower density and better thermal performance is thanks to the air pockets trapped inside the material.”
H1 changes are having the greatest impact on wall material and construction for earth buildings. Walls must now be a minimum of R2.0. “Some materials are unaffected,” notes Jessica. “Strawbale walls will easily meet this requirement given typical bale dimensions. Straw panel walls over 150mm thick will pass so long as the timber fraction isn’t unreasonable.”
But an R-value of 2 is out of reach for rammed earth: it would have to be two metres thick to reach that level of insulative performance! “We are already hearing indications that H1 is having a chilling effect on specifying external rammed earth walls. Upcoming projects are using rammed earth for internal walls or walls outside the thermal envelope.”
There are options and alternatives for homeowners who have their hearts set on incorporating rammed earth. Rammed earth can be adapted to meet the new thermal performance minimums but this will add to cost and complexity. For instance, the proprietary SIREwall system sandwiches a layer of insulating foam in the middle of the wall.
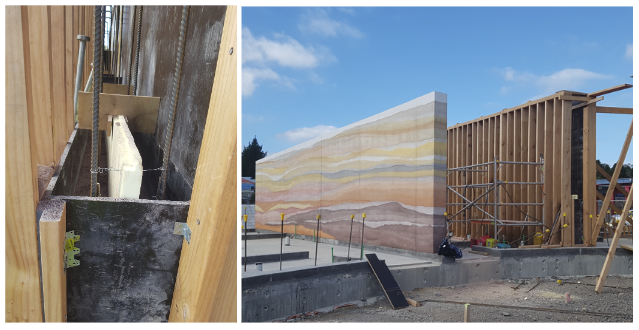
Rammed earth external wall with insulation sandwiched in the middle. Te Hononga at Hundertwasser Memorial Park, Kawakawa. Photo © 2019 Sustainable Engineering Ltd.
“Another option is to add “outsulation” (an external insulating layer—wood fibre board would be my pick here) and an exterior cladding,” writes Jessica. “Cladding adds a lot of cost but would protect the earth from weathering. In turn that could make it feasible to reduce the amount of cement added to the mix, a benefit for embodied carbon totals.
“Another option that mimics the monolithic appearance of a rammed earth wall is to apply an earth plaster or earth bricks as an external facade over timber-framed insulated walls.”
Jessica Eyer’s full paper is available here.
Comments 1
What absolute garbage. NZ has completely lost the plot. It’s a regulatory hellscape like no other. If you are generating your own energy from the sun to fully manage heat and electricity requirements of your own home then the govt can get stuffed. When you fully take into account the sustainability benefits of rammed earth over the life of a building it is untouchable. Requiring R2 for rammed earth is utter nonsense.