Kahika Tōtara Christchurch
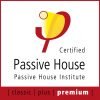
Project Team
Architecture & Passive House Design Meta Architects - www.metaarchitects.co.nz
Builder Ethos Homes - www.ethoshomes.co.nz
Certifier Sustainable Engineering Ltd – sustainableengineering.co.nz
A third Passive House home has been certified at Bushland Park in Christchurch, delivered on time and under budget to very happy homeowners. This project has achieved Passive House Premium status.
The experienced Passive House builders employ a deliberate strategy of working with the same suppliers and sub-trades as much as possible and building with prefab panels constructed in their own factory. They’ve made material choices based on their own assessment of quality, durability and suitability combined with customer preferences and requirements. This streamlines both the design and build phases, reduces risk and complexity and assists with managing construction costs and timelines.
For example, the same individual sub-contractor has installed Terra Lana wool insulation on their last six Passive House projects. The install quality is exceptional thanks to clear expectations, the subbie’s experience and the supplier’s willingness to provide custom-length rolls for the long runs.
The builders were very involved in the design of the homes envisaged for the Bushland Park subdivision. The landowner/developer also had a number of requirements. This house plan was revised following market feedback and now features a 30m2 attached garage (used here as a workshop and storeroom) in addition to a double carport. The flexible use attic space is accessed via a full staircase and an office is included downstairs. As all bedrooms are on the first floor, a lift has been installed to provide for ageing-in-place.
The lift and the client’s requirement for a direct extraction rangehood in the kitchen together had a material impact on heating load and heating demand. The lift reduces the treated floor area (TFA), the basis for all heating/cooling calculations. The project was modelled using PHPP9, before PHI’s helpful lift tool was released. The area of the lift footprint must be excluded from TFA on all levels, not just the ground level, so it has an multiplied effect.
Direct extraction in the kitchen requires make-up supply air, provided here via a 200mm diameter duct with an airtight non-mechanical backdraft damper. This supply air is not connected to the MVHR system but is wired to the rangehood. PHPP assumes the rangehood is being used for 30 minutes a day so during the cold winter months, that volume of cold outside air entering the house has a noticeable impact on heating predictions.
Despite the impact of the lift and direct extraction, the project met certification targets thanks to the build quality, which translates to an excellent airtightness result. The builder’s track record of consistently low airtightness results gives the designer confidence to model projects on the basis of 0.4ACH. Typically, modelling is done on the basis of a more conservative 0.6ACH result. The final result was 0.19ACH*.
Summers in Canterbury are hot and long. This house is shaded on the west side by remote controlled, rain-sensing louvres. Mechanical cooling and heating is provided by a fully-ducted air-conditioning unit with zone control. This is independent from the ducted ventilation system (here’s why integrating the two is not a good idea).
The homeowners didn’t know much about the benefits of Passive House when they signed the contract. Their carpenter son was part of the building team and they took his word for it that Passive House performance was worth having. They’ve been surprised and thoroughly delighted by their experience (and they still have their first winter to look forward to).
*PHI records this data to one decimal place, ie in this case 0.2
Passive House Metrics
- Heating Demand15.5 kWh/m2/year
- Heating Load10.0 W/m2
- TFA174.5m2
- Form Factor2.8
- Air leakage @ 50Pa0.2 ACH/hour
- PER demand87.0kWh/m2/year
Passive House Database - TBA
Construction Details Average Values
- U-value External Walls 0.22 W/(m2K)(R4.50)
- 140mm timber framed wall with R3.6 TerraLana wall batts, Intello air control layer, 45mm service cavity with R1.2 TerraLana batts.
- U-value Floor0.23W/(m2K)(R4.42)
- Concrete slab on grade with hollow pocket waffle pod system and 100mm XPS insulation.
- U-value Roof 0.13W/(m2K)(R7.91)
- Timber skillion roof with TerraLana R6.2 insulation, Intello air control layer and 90mm service cavity insulated with R1.2 TerraLana batts.
- U-value Glass0.65 W/(m2K)(R1.54)
- Metro - Xcel (ClimaGuard Premium 2) (4:/14/4:/14/4 90% Ar)
- U-Windows1.1 W/(m2K)(R0.9)
- Weathershield Warmcore
- Ventilation Efficiency 83%
- Zehnder ComfoAir Q450 HRV
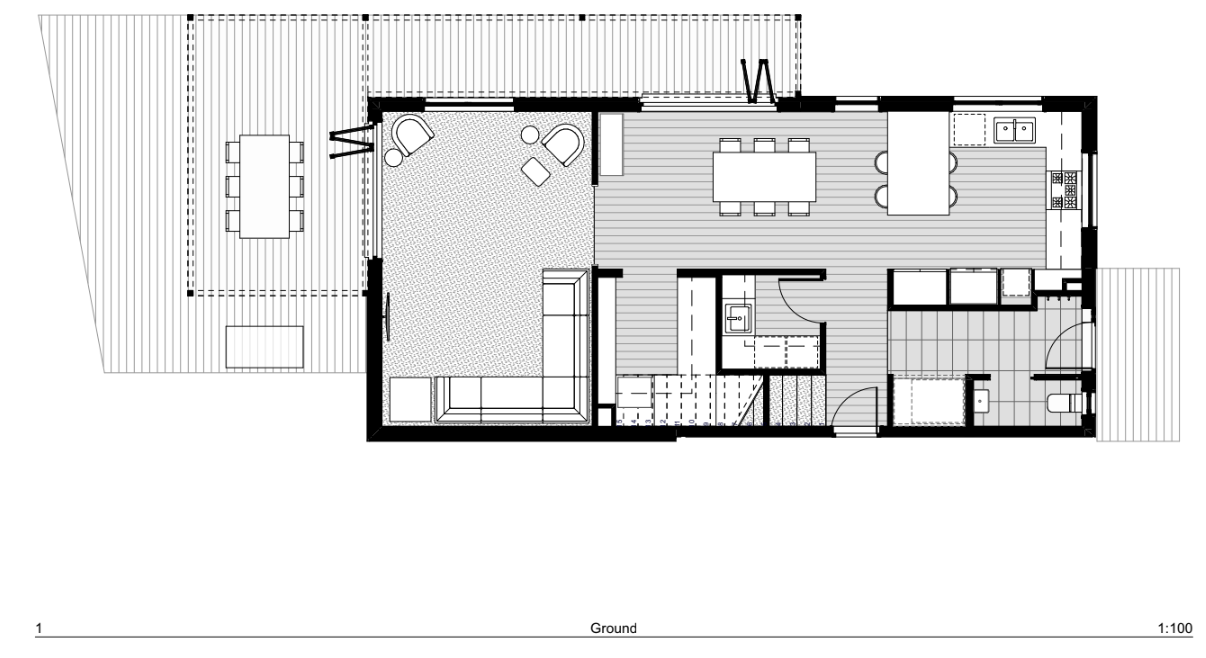
Ground floor
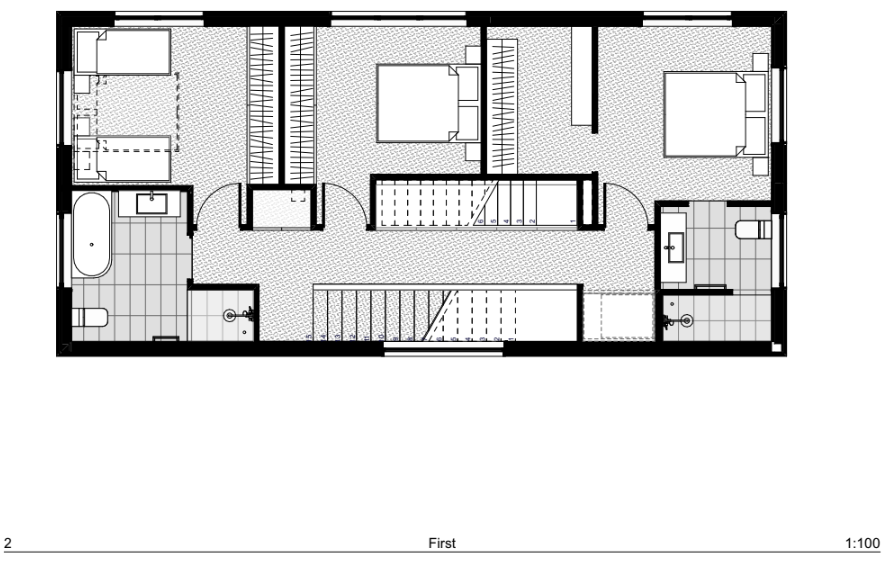
First floor
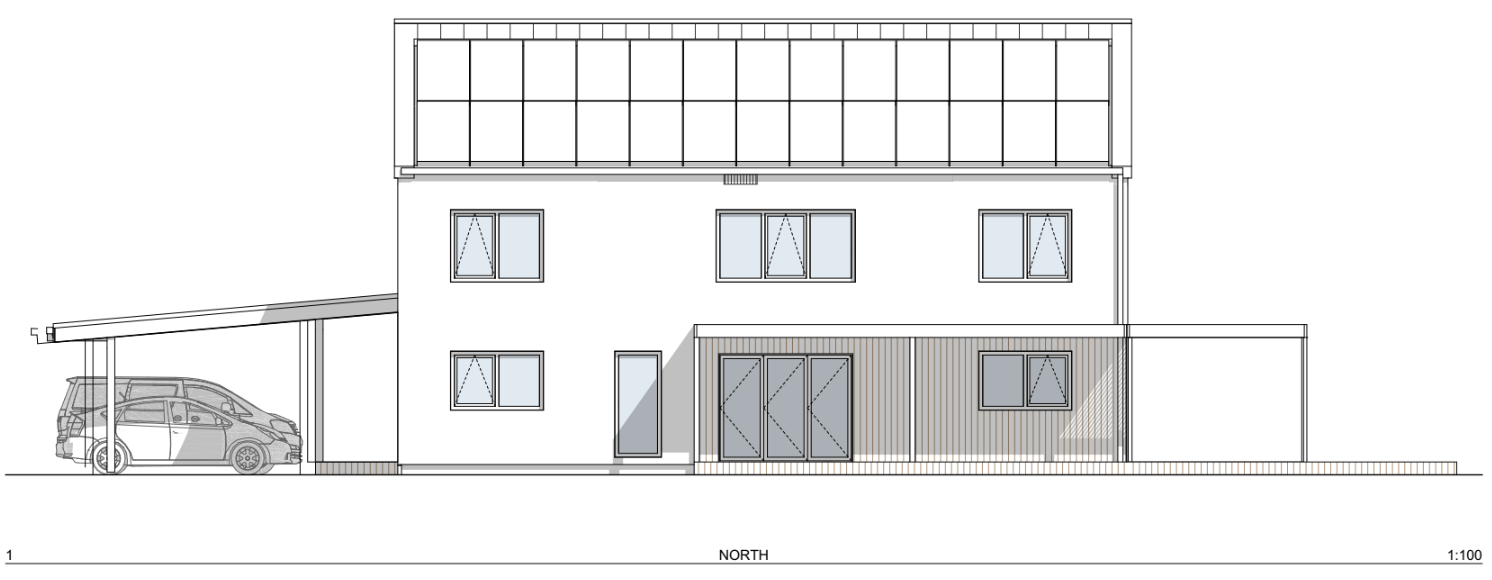
North elevation 1:100

West elevation 1:100