Maria’s Passive House Waikato
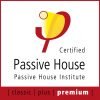
This appealing minor dwelling in the Coromandel bush has achieved Passive House Premium certification—only the third to do so in Aotearoa/New Zealand—and is believed to be this country’s first off-grid Passive House. It is a remarkable achievement. The building’s footprint is a mere 60m2; it’s inherently harder to reach Passive House levels of performance in such a small dwelling because of the surface area to volume ratio. Heating (and cooling) demand, PER and airtightness are all made harder to achieve because the targets are expressed on a per square metre basis.
The building has a large sliding door and two windows, creating a lot of east-facing glass. In winter, solar gain reduces heating demand. It is well-shaded in summer by a louvred pergola that controls overheating.
The large slider made for some significant challenges with blower door testing. The door needed to be closed for the test but there are only two small opening windows and the largest of these is smaller than the smallest blower door fan set up. A customised solution had to be found for the preliminary test. The dwelling’s small volume meant a duct blaster was required but even so the computer program running the test struggled to handle the volume and was wildly fluctuating between rings. There was a heartstopping moment when the air leakage figures were off the charts. Normal respiration resumed once the owner realised the program was sampling in cubic feet but plotting the results on a graph in cubic metres!
This building has a straightforward construction method using familiar materials and methods. In a smart move, all junctions followed those modelled in the High Performance Construction Details Handbook prepared by Jason Quinn at Sustainable Engineering Ltd for PHINZ. This removed the need to individually model any thermal bridges. The owner also credits Auckland’s milder climate with making his design task easier and thinks this significantly benefited them with regard to PER generation targets.
The project hasn’t been modelled for embodied carbon yet, but the owner is interested in doing so. The dwelling sits on driven piles. Concrete was used only in posts for the carport and deck and some pavers for pathways. The long-run steel roofing and PV arrays also contribute to upfront carbon.
The property is nine winding kilometres from the nearest small town and 1200m from a power line. With the estimated cost of hooking to the grid approaching a quarter of a million dollars, being self-sufficient for power was the only feasible option. It’s an all-electric build, with an induction hob (under a recirculating rangehood), a heat pump hot water system and the smallest heat pump that could be specified, with an impressive COP of 5.22.
Solar installers typically advise to minimise electricity use and use bottled gas for water heating and cooking in an off-grid set up. The draw from an induction cooktop is also said to rule out their use in such a project. But this home testifies to the need for more rigorous enquiry. While the induction cooktop energy use numbers looked high, deeper research showed the figure related to all four cooking zones being used on full power all at once, a highly unlikely occurrence in real life!
The owner-designer-builder describes the PER generation here as “off the chart”. In winter, all domestic use for four people is comfortably covered, but there’s not enough generation to also charge the 72kWh electric car. In summer, a clever integrated system slows generation down to a trickle once all batteries are fully charged. The drawn out process of getting the system designed and installed testifies to the inherent challenges of building anything outside of major urban centres—and the wild diversity of approaches to solar generation design. The persistence the owner applied to finding the most suitable solution is commendable.
The solar panels are mounted on the carport roof, taking advantage of its due north orientation (the monopitch roof on the house falls to the west, less than ideal). The carport roof could also accommodate more panels than the house. An insulated shed at the end of the carport houses the batteries and inverters.
Three generations are currently living on site in a variety of small buildings, “shuffling around” as each new building is finished. A 30m2 high-performance studio with outdoor gas cooking facilities and a relocatable cabin with improved insulation provide additional space. Once the main house is built, Maria will move into her home and the studio will become the owner’s office. It’s a superb example of flexible living spaces that can be repurposed as needs change.
It’s not the end of the Passive House action on this site: the large main dwelling is in developed design, awaiting an engineer’s review at time of writing. The owner is quietly confident it too could reach Premium status.
Project Team
Architecture & Passive House Design Build Good Architecture - buildgood.co.nz
Builder Build Good Construction Consultancy - buildgood.co.nz
Certifier Sustainable Engineering Ltd – sustainableengineering.co.nz
Passive House Metrics
- Heating Demand12.4 kWh/m2/year
- Heating Load9.7 W/m2
- TFA52.0m2
- Form Factor4.6
- Air leakage @ 50Pa0.6 ACH/hour
- PER demand44.3kWh/m2/year
Passive House Database - TBA
Construction Details Average Values
- U-value External Walls0.21 W/(m2K)(R4.86)
- 140mm timber framing with 45mm services cavity generally
- U-value Floor0.20W/(m2K)(R5.11)
- 240mm joists
- U-value Roof 0.16W/(m2K)(R6.24)
- 240mm timber rafters and 45mm services cavity
- U-value Glass0.56 W/(m2K)(R1.79)
- Triple glazing
- U-Windows0.9 W/(m2K)(R1.1)
- Eco Windows Gealan S9000
- Ventilation Efficiency78%
- Stiebel Eltron LWZ70