Slashing total carbon emissions driving goal of LowCO pilot project Auckland
Carefully evaluating both operational and embodied carbon emissions distinguishes Fletcher Living’s innovative LowCO homes.
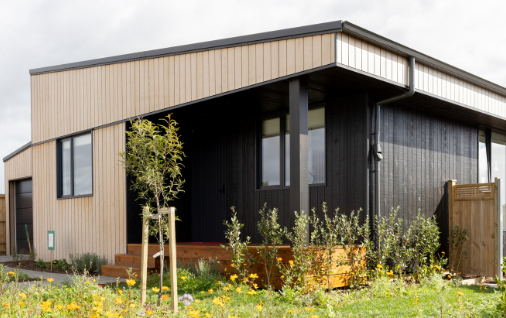
The LowCO detached family home
The Fletcher Living LowCO project establishes a new high-water mark for high-performance homes from a volume home builder. A three-bedroom house and three terrace homes have now been completed in South Auckland, with every decision about their design and construction considered through the lens of total carbon.
This project is significant, not just for the outstanding result but because of the process used to get there, says Jason Quinn, principal of Sustainable Engineering. “It has the potential to catalyse a significant shift in how residential homes are built in New Zealand. The design and material choices were driven by building physics. The wide-ranging modelling uncovered carbon emissions hiding in unexpected places and the team found innovative ways to address it. Material choices had to work at scale, so that lessons learned here could be replicated more widely. Fletcher Living’s decision to publicly release all their IP means its learnings are available to any builder or homeowner in New Zealand.”
Sustainable Engineering has worked on this project from start to finish. As well as extensive initial modelling that set the direction for the project, its team prepared the submission for HomeStar rating for the stand-alone home. While much has been published about this project, this in-depth technical case study goes into new detail about the modelling that underpins design and material choices.
“Without aiming for either certification, the LowCO home has gained 10 Homestar and, but for the windows, could have achieved Passive House certification.”
—Jason Quinn
Genesis
New Zealand has committed to reaching net-zero carbon emissions by 2050. The built environment accounts for 20% of the country’s emissions. Reducing carbon emissions can’t be achieved without a significant shift in the way developers and builders design, source materials and build.
LowCO was driven by Nicola Tagiston, head of sustainability at Fletcher Living, who was galvanised by a 2020 report from BRANZ and Massey University*. The first study of its kind to calculate a carbon budget for standalone New Zealand homes, it found housing must shrink its carbon footprint by 80 percent if we are to stay within two degrees of global warming.
Researchers took New Zealand’s carbon budget, divided it between different sectors and assigned a share to a newly built detached house: 39 tonnes CO2 equivalent over a 90-year expected life. Typical new detached housing is over budget by five to seven times.
The vast majority of new homes in New Zealand are built by volume home builders and Fletcher Living is among the largest. It is an end-to-end developer, creating entire communities in Auckland and Christchurch. Nicola Tagiston wanted to know: could Fletcher Living build a commercially viable home that emitted no more than its fair share of carbon emissions?
Typical new detached housing in NZ exceeds its carbon budget by five to seven times.
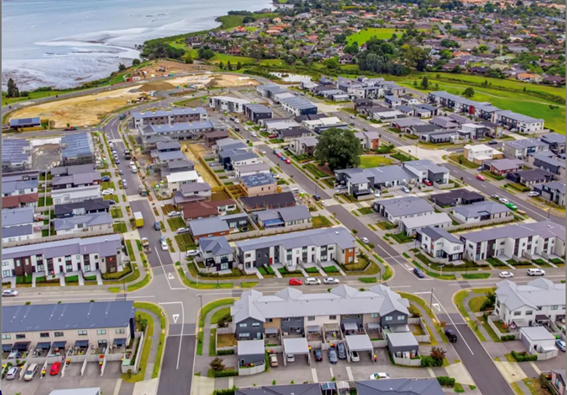
A Fletcher Living development in Auckland
Total carbon modelling
Nicola Tagiston reached out to Jason Quinn in December 2020 and his team went on to play a leading consulting role. Sustainable Engineering modelled both embodied and operational carbon, using PHPP, in-house tools and LCAQuick to gauge the impact of different designs, materials and construction methods. One result of this unrelenting focus on carbon was a Passive House model before buildings were even designed. “LowCO was not aiming for Passive House certification but Passive House provided essential tools and methodologies that helped achieve the total carbon goal the project was striving for. Passive House systems and software were enabling tools,” explains Jason Quinn.
A total carbon goal, at scale
The Passive House system is world-leading with regard to reducing operational carbon emissions because buildings certified to this standard need such tiny amounts of energy to heat and cool to comfortable, healthy levels. It’s proven in New Zealand conditions and provided a obvious process for delivering operational carbon emission savings.
However Passive House is ‘material agnostic’, leaving those decisions to the discretion of clients and designers. Certification doesn’t mean such buildings are necessarily equally low in embodied carbon. LowCO decisions about materials, methods and design were all carefully weighed against embodied carbon as well as operational carbon: a total carbon emissions perspective.
“If we consider high-performance housing that slashes operational carbon—that is, certified to the international Passive House standard—New Zealand has 156 of them right now. Almost all are residential,” says Jason Quinn.
“The majority of those projects are bespoke single-family homes. They produce a great outcome for those families that live in them but they are not replicable at scale. LowCO’s systematic analysis at design stage and the data that will be gathered from three years of post-construction monitoring, combined with Fletcher Living’s scale of operation, means LowCO could represent a turning point in New Zealand construction.
“Industry regulation and government leadership is crucially important. I applaud Fletcher Living for getting ahead of minimum regulatory standards on this project and hope many elements of LowCO will find their way into Fletcher Living’s standard offerings,” says Jason Quinn.
The experienced Passive House design team at Architype undertook architectural design for the LowCO terrace homes, plus detailed design for the LowCO detached house. Full PHPP models were developed in order to ensure operational carbon emissions were minimised.
Modelling the embodied carbon was a big undertaking, especially because it was shaping design decisions. It was quite a different process compared to tallying the footprint of a finished design.
Sustainable Engineering developed an in-house tool capable of running the numbers for energy modelling and embodied carbon models at the same time
“It meant we could readily answer lots of interesting questions,” says Jason Quinn. “What if we change the cladding, wall linings, foundation, insulation systems? All at once, we could see the whole Life Cycle Assessment implications and zero in on the optimal choices. “We then modelled the designs in LCAQuick, a very useful tool from BRANZ. That provided solid evidence that proved the value of the chosen solutions.
Post-construction review confirmed that both the terraces and home emitted less than 39 tonnes CO2 equivalent over a 90-year expected life. They perform to a similar level when compared variously per unit, occupant, or treated floor area.
Operational carbon accounts for the greatest share of emissions. The main operational factor is electrical plug loads, because of Passive House measures that reduce heating and cooling loads. Hot water heating is typically the largest consumer of energy but its share was massively reduced by specifying a heat pump hot water heater.
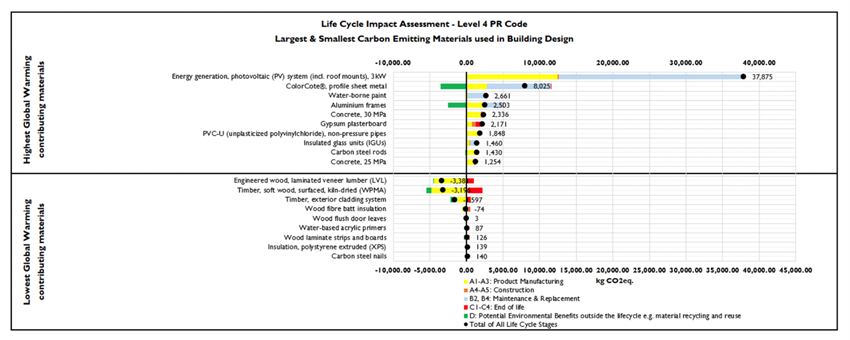
Source: LowCO House and Terrace: LCA Quick Carbon Report – Post Construction, Sustainable Engineering Ltd, October 2023
The embodied carbon emissions are primarily found in metal (roofing, windows, reinforcing); concrete (slab for the terraces); and items with multiple replacement cycles (paint and photo voltaics). Typical high-embodied materials such as carpet or cladding requiring regular repainting, are deliberately absent.
“If you asked people to nominate materials with large embodied carbon emissions, few people would bring up carpet,” says Jason Quinn. “Concrete and steel are far more obvious. The LCA models are based on office use and predict frequent replacement of carpet. That can tip the comparison between different flooring materials. In many cases, a longer-lasting, more durable material is a better option over its life, even if it has a higher embodied carbon associated with its manufacture only.”
The homes all have grid-tied solar panel arrays on their roofs, which account for a big reduction in operational carbon. The panels are weighty with embodied carbon but this is outweighed by the operational benefits over their lifetime.
The report also reviewed the figures over a 50-year lifespan, consistent with the MBIE guidelines. This reduces overall carbon totals because of fewer replacement cycles for materials.
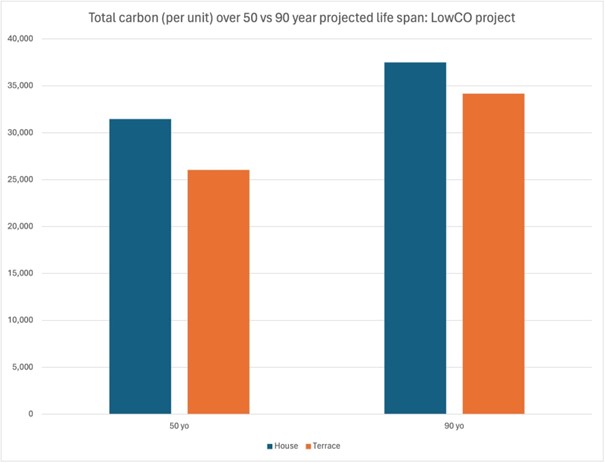
Source: LowCO House and Terrace: LCA Quick Carbon Report – Post Construction, Sustainable Engineering Ltd, October 2023
Independent verification
Having a target for total carbon emissions directed choice after choice that was compatible with the Passive House system. “The stand alone home meets all Passive House targets bar one,” explains Jason Quinn. “Airtightness performance is right on the maximum, likely because it was the construction team’s first experience but they succeeded in meeting the standard. It hits the PER target. The only miss is fSRI, specifically with regard to the surface temperature of the aluminium window frames.
Homestar certification was only considered after the project’s completion. The NZ Green Building Council had been following the LowCO project with interest and raised the possibility of HomeStar certification with Fletcher Living. Sustainable Engineering completed the submission and this was aided by Jason Quinn having previously done work for NZGBC on the technical criteria for Homestar V5. Thanks to his intimate knowledge of the criteria, the LowCO house has achieved 10 star certification rather than the 8 stars initially anticipated—and without the use of innovation points. The LowCO house joins only a handful of homes to achieve this top ranking.
Operational carbon savings
In order to reduce operational carbon emissions, LowCO designs incorporate a series of well-understood choices, familiar to any Passive House designer. Thermal bridges are mitigated or avoided, a mechanical ventilation with heat recovery system is installed, airtight construction methods and materials were employed, more insulation was used and windows and doors are higher-performance than Building Code minimums.
None of these changes from business-as-usual were optional in the face of the project’s goal, notes Jason Quinn. “Code-minimum houses perform a bit better following new H1 energy efficiency targets mandating higher R-values, but they are still most often hard and expensive to heat and cool and at risk of damp indoor environments that can create mould and respiratory illnesses. LowCO didn’t need to reinvent the wheel when it came to slashing operational carbon emissions—a well-proven road map already exists in the Passive House methodology.”
On the ground, this means a mechanical ventilation system with heat recovery, an air-tight building envelope, better than usual insulation levels in floor, walls and ceiling, thermal breaks and higher-performing windows and doors. (The most important Passive House principle is energy modelling at design stage, so that the effect of all these on each other and the site can be accurately predicted.)
Materials
Fletcher Living is generously making its IP available for this project—detailed sets of plans for the three-bedroom home and terrace homes are available online for anyone to download. They include a summary sheet showing the details of every item used in the home, down to the toilet roll holder. Products from the Fletchers range feature but not exclusively—for instance, the garage is lined with a Saveboard exposed face wallboard.
All product choices were investigated using the total carbon emissions lens, says Nicola Tagiston. “Our preference was locally manufactured products with low associated carbon emissions.”
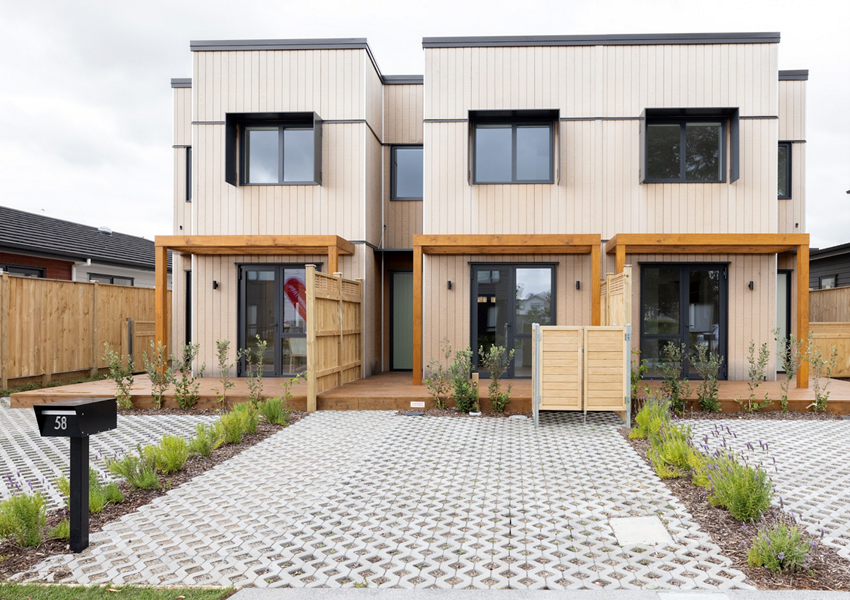
LowCO terrace homes
Cement
When it came to reducing embodied carbon emissions, LowCO started with the easy savings: the detached home is suspended on timber piles rather than concrete slabs, saving 7 tonnes of carbon emissions.
Staff at LowCO, Firth and Auckland Transport (AT) put their heads together and pioneered kerb-crossings using Firth’s EcoMix, a 43% saving of carbon emissions compared to standard cement. AT permitted a Departure from Standard to greenlight this innovation and a practice note is in development that will provide other developers and builders a pathway to use the same material. Instead of a concrete driveway, the LowCO house and terraces have permeable paving. This reduces carbon emissions and increases rainwater infiltration.
Panellisation
The use of timber framing and cladding with batt insulation was sensible given this is the standard construction method for New Zealand housing and familiar to any builder. However LowCO went considerably further by specifying prefabricated panellised construction. Walls, roof and the terrace midfloors were manufactured off site by Clever Core, another Fletcher Building company. There are many advantages to offsite construction but waste minimisation is often overlooked. The savings here were huge: by lockup stage, the LowCO house had produced less than one wheelie bin of waste, compared to an estimated 1 tonne on a typical build, says Nicola Tagiston.
External insulation
The house and terrace walls are constructed with external insulation, a 40mm wood fibre product. “I’m a big fan of this type of product and I’m really pleased to see it used on this project. I want to see it become widely available in New Zealand because it offers a lot of benefits to a wide range of construction projects,” says Jason Quinn. “Ideally, we’ll see a plant set up to manufacture wood fibre insulation here in New Zealand.
“It puts the air control layer on the outside of the building, which makes air tightness really easy. It’s pretty much business as usual for the trades on site. Electricians and plumbers get to work on the inside of the thermal envelope, so there’s no need to plan for penetrations of the airtight layer and ensure they are well sealed. The 90mm stud cavity essentially becomes a service cavity.
“The construction sequence was very familiar to tradespeople, especially the Fletchers’ teams already used to the Clever Core panels. The panels are craned into place, the structure is airtighted, instead of simply weathertighted, but in a similar manner. The wood fibre insulation is fixed, then it’s battens and cladding. The only additional step is fixing an air control membrane in the ceiling.
“Further, because the insulation is continuous, the timber fraction in the wall is much less of an issue. External insulation would even mitigate the impact of steel structural members or steel framing, not that these were present here.”
Window system
The aluminium window system is Centrafix 44, a locally made, double-glazed product with argon fill and low-e coatings. The highest-performing option in APL’s Centrafix suite is capable of meeting the Passive House standards in Auckland, but the base model was specified for this project. Centrafix is a system: windows and flashings are integrated and it includes a profile for installing these windows in the middle of the wall. “That window placement is important for thermal performance but at odds with E2, which specifies windows installed in line with the external cladding,” says Jason Quinn.
“Small innovations like this have the potential to make a big difference to the scale of uptake of better performing construction details. By offering a complete system, APL has reduced the risk for designers and builders unfamiliar with recessing windows. ”
Recessed placement of windows was new for Clever Core and a test wall was built first. The standard wall panel needed to be wider to accommodate the window placement and additional insulation. French doors were also a first for Clever Core, which uses sliding doors as standard. Energy modelling had shown that French doors would reduce heating demand compared to the less airtight sliding doors on offer.
“Back in 2022, when the LowCO team was making fenestration decisions, there were few options for locally made high-performance windows. Aluminium frames dominated the New Zealand market. The key challenge is finding a window that can perform in line with global thermal standards and is also low carbon and affordable,” says Nicola Tagiston. “Plus durability and customer acceptance have to play a big part in window selection.”
Water
LowCO rigorously considered water usage, setting a goal to meet MBIE’s 2035 water use target of 75L per person per day. This is obviously a laudable outcome that benefits the community but also individual homeowners in Auckland, where residential three waters use is metered and billed at a household level.
Carbon modelling highlighted that the three water connections to a dwelling are carbon intensive, both from an embodied and operational perspective. Disposal of black and grey water is by far the most significant from a carbon perspective. “This is not immediately obvious,” says Jason Quinn. “By making the carbon cost of water visible to developers, and equally showing how to mitigate it, I hope LowCO will have an immediate influence on standard practice.”
The project leaders took multiple steps to mitigate water and thus energy and emissions use, reducing water use by over 80% in the house and by half in the terrace homes. This was achieved through a combination of harvesting and storing water, re-using as much water as possible and overall simply using less. Hot water heating is the single biggest user of electricity in a typical New Zealand home, so heat pump hot water heaters were an obvious choice. (Heat pump efficiency and airtightness also dictated selection of a 10 star heat pump condensing dryer in the laundry.)
WaterCare came on board as a project partner and the learnings already gained from LowCO have spurred many meaningful conversations about demand management and the need for more research to fill data gaps.
Water efficiencies
Water saving fittings were an obvious starting point. Other solutions were more innovative, some breaking entirely new ground.
- A New Zealand-first install of a Hydraloop greywater recycling system treats bath and shower water and lightly contaminated grey water and recycles it to flush toilets, supply a selected washing machine rinse cycle and to irrigate the vegetable garden.
- On-site water treatment of rainwater involves UV and carbon filters, making recycled water safe for all household consumption purposes.
- A connected array of water storage pods fit under the suspended floor of the house (8250L) and within the insulated floor slab of the terrace homes (4500L each).
- Hard and soft landscaping was made more water-friendly. Run off was minimised by reducing impermeable surfaces by 75% and creating a meadow.
- Garden hose connections are supplied by harvested greywater or rainwater and drought hardy plants were selected.
- A digital thermostatic mixer is installed in the showers, reducing hot water wastage and water heating costs.
Internal finishes
Fletcher Living’s team wanted to balance customer preferences and material toxicity with life cycle data about embodied emissions and replacement cycles. Engineered timber flooring has a much longer lifespan than carpet and is familiar and acceptable to homeowners.
Benchtops proved challenging, with many choices to consider and a lot of data to sift. “We looked at engineered stone, native timber, stainless steel, even recycled glass,” says Nicola Tagiston. “In the end, Formica wrapped around a timber core makes for a very durable and time-tested benchtop. Since completion we’ve come across Critical, which is making countertops from recycled plastic. That’s a possibility for splashbacks or benchtops. The technology is moving so fast and new products coming to market offer ever more options.”
Influence
Nicola Tagiston emphasises that this project was never approached as a one-off. “It’s about taking what we learned and figuring out how to push it into the mainstream.”
Sustainable Engineering is, at time of writing, preparing an analysis of the carbon-to-cost trades compared to a standard offering. Those numbers will guide Fletcher Living on what to integrate into its standard offering. “We’re driven by data and science”, says Nicola Tagiston. “For every decision, there are three layers to consider: carbon, cost and customers.”
She doesn’t want to prejudge the report findings but thinks hot water heat pumps are a strong contender. “They are 75 per cent more efficient than a standard cylinder. And we know people are becoming more eco-conscious, especially around energy and water use, which they are billed for.” More airtight construction combined with ventilation is important too, given how it reduces heating bills and improves indoor air quality. There’s an upfront cost to those materials and methodologies but operational savings continue to accumulate and Nicola Tagiston is keen to see the results of follow-up monitoring.
“Jason Quinn has taught me so much about thermal efficiency, it’s been incredible working alongside him.”
—Nicola Tagiston
LowCO has had a big impact not just for staff at Fletcher Living but across other Fletcher companies, suppliers and local authorities. It also fostered connections between expert consultants from different disciplines. “Jason Quinn has taught me so much about thermal efficiency, it’s been incredible working alongside him,” says Nicola Tagiston. “LowCO has catalysed a much better understanding of building science across the whole Fletcher Living team. It touched our people in construction, QS, design, even the administrators. It’s made us think again about how we build, about the critical junctions. It’s flowed through to our subtrades, this is the first time they’ve got to handle these new products and systems.”
Nicola Tagiston recalls a particularly gratifying moment when she walked into the LowCO house at pre-line stage. “The carpenters had first worked on the terraces, that was where they got to grips with the airtighting. When I saw the wraps and taping in the house and saw the level of understanding they’d developed … they had nailed it. It was a beautiful thing to watch people’s skills and understanding grow.”
Ongoing research
Neither the house or the terraces are for sale, at least not yet. First, each home will be tenanted to support ongoing research. Occupants will be surveyed every six months about their experience living in the LowCO homes and extensive data will be collected and analysed. This will continue for three years and the results will feed into further development plans. Unsurprisingly, there have been a lot of rental applications from staff in the various Fletchers companies.
“LowCO was a high profile project with a very clear purpose. The sister companies rallied around us. Staff have been following us on this journey for three years. We communicated a lot internally, posting videos and articles to the staff intranet. We even had cameras on site so staff could see real-time progress. Our people are excited by it,” says Nicola Tagiston.
Fletcher Living wanted to take a leadership position, says Nicola Tagiston. “This is where New Zealand needs to head. We wanted to share the plans so that anyone can interrogate them and use them as they see fit.”
“These four homes are great. Now, what can we do for the next 996 we’ll build?”
—Nicola Tagiston
*A science-based approach to setting climate targets for buildings: The case of a New Zealand detached house. Chanjief Chandrakumar et al. https://doi.org/10.1016/j.buildenv.2019.106560
Project Team
Architecture & Passive House Design Architype Limited - architype.co.nz
Builder Fletcher Living - fletcherliving.co.nz
Homestar Assessor Sustainable Engineering Ltd – sustainableengineering.co.nz
Passive House Metrics (Not Certified)
- Heating Demand15.4 kWh/m2/year
- Heating Load10.3 W/m2
- TFA104.4m2
- Form Factor3.7
- Air leakage @ 50Pa0.6 ACH/hour
- PER demand30.2kWh/m2/year
Construction Details Average Values
- U-value External Walls0.34 W/(m2K)(R2.92)
- 90mm CleverCore with 40mm Steico Wood Fibre External Insulation
- U-value Floor0.28W/(m2K)(R3.56)
- 19mm Strandboard on 190mm timber joists with R4 Pink Batts
- U-value Roof 0.15W/(m2K)(R6.89)
- Truss roof with R7 Pink Batts over Intello
- U-value Glass1.12 W/(m2K)(R0.89)
- Metro Excel (4:/16/4 90% Ar)
- U-Windows 2.0 W/(m2K)(R0.5)
- APL Centrafix 44mm suite
- Ventilation Efficiency 90%
- Zehnder Group Nederland B.V. - ComfoAir200, ComfoD250, WHR920