Prefab builder scores 6 Homestar rating for affordable high-performance homes
Fast, cheap, good: pick two. Everyone in construction has heard that saying. But it’s challenged by the prefab building manufacturer Manor Build’s achievement of a volumetric 6 Homestar version 5 (v5) rating for three different home designs.
A volumetric rating is a bit like pre-approval for a mortgage. Any home built to these designs, in any of the North Island climate zones Manor Build supplies to and regardless of the building’s orientation or onsite shading, is already verified as meeting the Homestar target and 90% of the submission for each home built is already complete. This is a really significant achievement, not least because it proves that higher-performance, markedly healthier homes can be built to a modest budget.
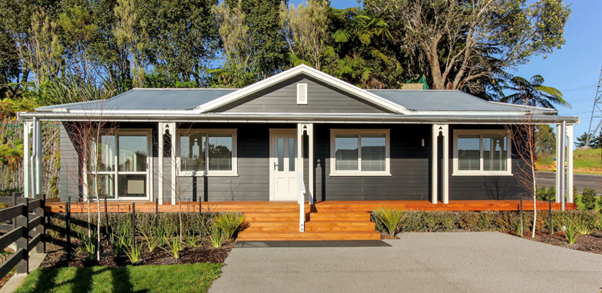
This built example from the standard Manor Build suite will probably mess with your assumptions about how prefab homes look. © 2024 Manor Build
Manor Build 6 Homestar v5 designs at a glance
- Three designs: 2-bedroom (70m2 conditioned floor area), 3-bedroom (102m2) and 4-bedroom (119m2), each with a single bathroom
- Factory built and transported to site, delivered in seven months from date of contract
- Actual build time 8-10 weeks
- Metra Panel construction reduces thermal bridges and serves as an air and vapour control layer for the roof and floor
- Sustainable, durable sheet cladding product over cavity, no need to paint
- Targets airtightness test result of 3.0 ACH
Choosing performance
There are different ways to achieve Homestar points and two homes achieving the same rating may have very different features and levels of thermal performance. The very nature of a volumetric rating application means none of the Homestar credits that can be earned for site-specific features could be accessed.
Manor Build have chosen what Jason Quinn from Sustainable Engineering Ltd approvingly calls “the engineer’s route”, focused on those improvements that can be controlled and standardised in a factory and which improve the efficiency of the house and the comfort of its occupants.
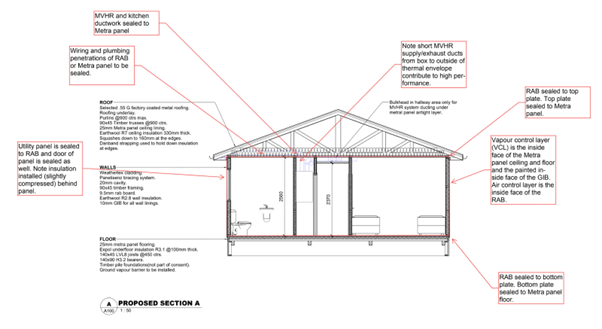
An example of the Sustainable Engineering marks ups on construction drawings provided to NZGBC in support of the 6 Homestar application.
The result are remarkably high thermal performance homes that confound stereotypes about prefab buildings. While short of certified Passive House targets, the Manor Home 6 Homestar designs are all vastly superior to the Building Code minimums and use practices and components instantly recognisable to a Passive House designer: a full MVHR system, quality thermally broken joinery, high-tech glass coatings, a continuous air control layer and an absence of thermal bridging. The design also meets Kāinga Ora requirements for universal accessibility.
This rating is proof that higher-performance, markedly healthier homes can be built to a tight budget.
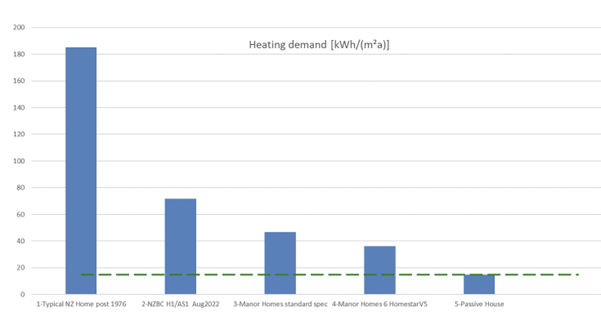
As this graph illustrates, even Manor Build’s standard spec has much better thermal performance than a Code-minimum house built to current H1 standards.
Genesis
Manor Build and Sustainable Engineering worked closely together since April 2022 to arrive at this solution. However, the project genesis actually goes back four years to when a very well-informed Taupō couple showed up on Manor Build’s doorstep and informed the company that they had the best-performing, healthiest home available in New Zealand in their price range.
“These customers had researched our business and model, they knew more about healthy homes features than we did,” says Rob Foster. He’s the general manager of sales and marketing at Manor Build. “They paid extra for thermally broken joinery, upgraded insulation and a full ventilation system. The result was a home well above Code. Then the customers’ daughter ordered one for herself too. We realised there were people that cared about these things and we wanted to do more.”
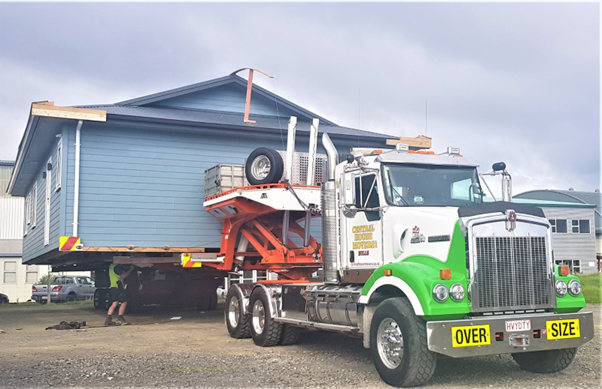
The high-spec home ready to depart for its Taupō site. © 2024 Manor Build
An ideal partnership
That led Manor Build to Sustainable Engineering for some expert advice. The first step was the Initial Design service, the development of a preliminary energy model used in this case to predict the results of increased insulation levels. The opportunity to supply prefab homes to Kāinga Ora saw Manor Build double down on improvements in order to meet the social housing provider’s requirements.
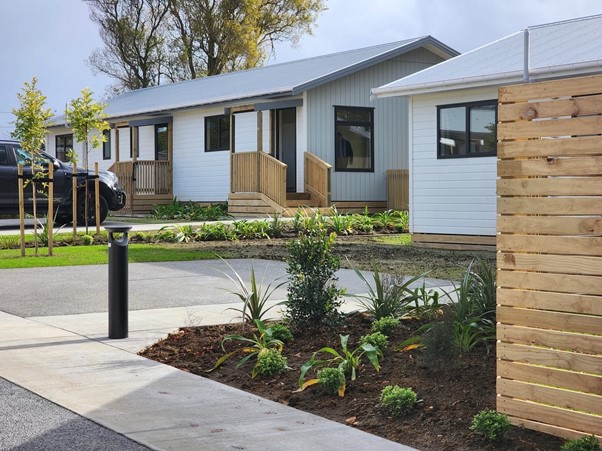
Manor Build paired with a Taranaki developer to supply four homes with custom layouts for Kāinga Ora. An exceptionally short deadline for delivery meant these homes weren’t Homestar rated. © 2024 Manor Build
At the time, Kainga Ora had ambitious new building targets and was requiring greater-than-Code performance. “That decision, by a developer of their scale, was pulling up the whole industry, incentivising suppliers and manufacturers to improve their offerings in various ways,” notes Jason.
V5 improvements to Homestar
Homestar v5 introduces many best practices from the Passive House methodology in a stepped fashion, says Jason. There are three substantial new requirements compared to V4:
- an air control layer and an airtightness target (this varies according to the star rating)
- management of thermal bridges and
- a continuous ventilation system and moisture management
Jason was one of the industry experts that contributed to the v5 changes in Homestar, particularly those relating to energy use that resulted in these three significant changes. Preparing the Manor Build submission prompted useful technical clarifications regarding the way factory-built homes are best evaluated for Homestar.
An ideal client
In Manor Build, Jason found an ideal client, one willing to thoughtfully consider best practice and how they could achieve that through their precise and standardised manufacturing process. “They are an amazing team. Repeatedly, I outlined the options for a particular issue—’here’s the best way to do it, but there’s also this inferior option that is cheaper’. Every time, Rob and his guys chose the best way, starting with achieving 6 Homestar under V.5 requirements [at the time, Kāinga Ora had an exemption from NZGBC allowing its buildings to continue to qualify under V4]. That was so great. It helps that their factory setting means they can optimise construction details, including building jigs to make hard or fiddly things faster, precise and easily repeatable,” Jason says.
The miracle of prefab is that so much extra can be delivered for such little additional cost.
The relationship worked for Manor Build too. “It was a positive process, I liked working with Jason,” says Rob. “He bought into what we wanted, which is to find a single design that would [meet the Homestar requirements] everywhere. Jason was clearly passionate about what we were trying to do and that showed. We liked that, and also the way he challenged us about how to do things.”
Jason also helped with ideas about how to talk to customers about the technical improvements in a way that was meaningful to them. “That was good, I enjoyed those discussions and he was helpful,” Rob says.
Modelling
Every Passive House designer with some experience knows that site shading and the building’s orientation are a big deal when it comes to heating demand and overheating risk. So how did Sustainable Engineering and Manor Build solve this challenge, of one design that will work in all North Island climate zones from Auckland south?
It started with Sustainable Engineering’s expertise meeting a lot of computing power. “We ran thousands and thousands of energy models,” Jason explains. “We worked in ECCHO using the variant feature that is hardly used yet.” (Jason wrote the first spreadsheet version of ECCHO; he knows how it works, inside out.) These were whittled down to the 96 models submitted with the Homestar application, a matrix formed by three buildings, four possible orientations, two glazing options and four climate zones.
The modelling illuminated that the main challenge was a delicate balance, preventing overheating while not exceeding the heating demand maximum. Jason could then start problem solving, relying on his in-depth knowledge of individual components. Manor Build’s goal of a single design was achieved, but with a small twist. When building for one of the warmer climate zones, the factory supervisor needs to consult a table that lists the designs by orientation.
In those circumstances where the risk of overheating is highest, the building will be supplied with low solar gain glass. There’s no difference for factory processes but the order to the glazing supplier, Metro Glass, is changed. It’s worth using this only when needed; low solar gain glass adds to glazing costs and increases winter heating demand. Using it everywhere just for the sake of a one hundred percent consistent spec wasn’t a good idea.
The Manor Build factory is in New Plymouth; this area reflects the distances that it is feasible to transport finished buildi
Prefab advantages
The nature of prefab building helped Manor Build achieve the requirements of 6 Homestar v.5. The insulation installation is finely optimised. Using panellised construction for floors, walls and ceilings—30mm strand board in a Metra Panel—provides a dwang-free building structure (less thermal bridging, more room for insulation) and a rigid air barrier. The Homestar-rated units will be blower door tested before they leave the factory. “The requirement is 3.0 ACH for the volumetric rating but they will slam dunk that. By the time those guys have built one or maybe two buildings, they’ll hit 1.0 ACH,” predicts Jason.
The Manor Build team is already highly focused on streamlined processes that are highly repeatable and reduce variables to the minimum. For instance, every building is now built to an extra high wind zone rating and there’s only one type of insulation in the factory store. “We want the guys in the factory doing the same thing every time. The floor plan, that’s customisable. But the systems and how we approach the build are always the same,” says Rob.
“All buildings, all homes, need continuous mechanical ventilation. It’s not just a nice-to-have for a fancy, big-budget Passive House home.”
Ventilation
The Manor Build 6 Homestar designs come with a Steibel-Eltron MVHR, as would be found in a certified Passive House home. Jason is very pleased that Manor Build opted for the best-practice option here (this blog post about trickle vents details the cheap and far less satisfactory option they decided against).
“Adequate ventilation is even more critical in social housing because these homes are typically pretty crowded,” says Jason. “They’re also people that can least afford high power bills—and it’s unrealistic to assume that doors and windows will be regularly opened for sustained periods in order to reduce humidity and ensure fresh air. That will make the house even harder to keep warm. Continuous mechanical ventilation with heat recovery is absolutely what’s needed here.”
Ventilation options had a big impact on heating demand numbers too. A MVHR meant Manor Build could stick with their preferred thermally-broken aluminium window frames from an established supplier. The cheap option—trickle vents and an extract fan—had cascading consequences, the most significant being a need for uPVC windows with higher R-values.
With all that carefully considered, Jason specified a high-performance, PHI-certified mechanical ventilation system with heat recovery, where all the ductwork runs inside the air control layer. This is the same type of unit as would be found in a certified Passive House. The MVHR increased the thermal performance of the home such that these homes could meet the 6 Homestar v5 energy targets, in all the climate zones and all orientations, using the standard thermally-broken aluminium joinery and high performance double glazing.
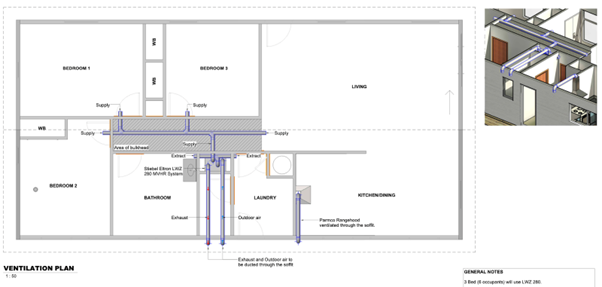
The layout of the MVHR ducting was optimised for efficiency and cost savings.
An MVHR adds additional first costs but Manor Build kept it to a minimum by optimising the ventilation ductwork. This also serves to maximise efficiency and minimise noise. All ducting runs above a bulkhead in the hallway only, removing the need for a service cavity spanning the entire ceiling. There’s direct extraction above the kitchen hob, with make up-air delivered via an adjacent window.
Manor Build previously installed positive pressure ventilation systems in their homes. Rob says they understand now this isn’t the best option for ventilation and they are working through what changes they’ll make to their standard build spec. A full MVHR system will remain an upgrade that any customer can opt for.
Connecting suppliers
Manor Build project benefited from the path blazed by bigger, better-resourced projects and Sustainable Engineering’s in-depth knowledge of suppliers and manufacturers of high-performance components. For instance, all Manor Build homes now specify Weathertex cladding, a sustainable sheet cladding product made from reconstituted Australian hardwoods. The cost of the material is offset against considerable savings in the labour to fix it. It also comes pre-coated and requires only minimal future maintenance. That’s attractive to a developer of build-to-rent properties as well as many homeowners. Jason was aware of Weathertex through the work his team did on Fletcher’s Living’s heralded LowCO homes and suggested it as an option.
Manor Build did all this work with the aim of constructing homes for Kāinga Ora. They’re ready to start delivering, only to have the incoming government review the agency’s operation and halt all new housing construction by Kāinga Ora. It has signalled that community housing providers will instead be expected to construct social housing to meet the acute need in the community.
Where to now?
It’s too early to say whether many small community organisations will collectively have the building science knowledge to understand the problems with New Zealand housing and how they can be overcome. Will they value higher performance and the healthier, more comfortable environments such homes offer? It remains to be seen. Meanwhile, Manor Build can offer these improvements to any of its private customers. The marvel of prefab is that so much extra can be delivered for such little additional cost.
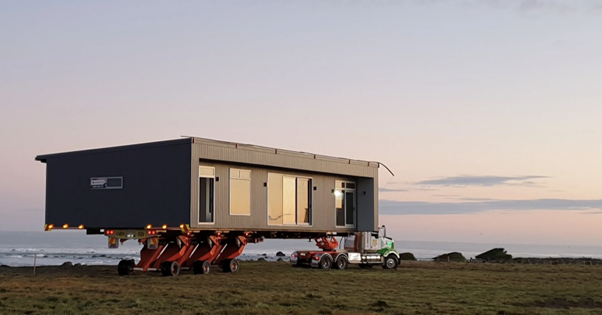
Manor Build delivers to some pretty remote places around the motu. © 2004 Manor Build
Manor Build, in its various iterations, is more than 30 years old. It’s a family affair, now run by the founder’s son and two brothers-in-law, who refocused the company on residential building. Its customers are varied. They build farm accommodation and homes for lifestyle blocks in remote locations where builders are hard or impossible to come by. They supply bachs for homeowners, cabins for holiday parks and build offices. Manor Build does some building for private developers—that’s how they first got involved with Kāinga Ora—and of course sell directly to homeowners. About 20% of their work is commercial.
The company looks to hire people with factory floor experience. “If someone has worked on a slaughterhouse production line for instance, they’re used to being disciplined and accountable. We take a person like that, train them on the job and provide them with an environment that is way more varied and interesting,” says Rob. Production staff work in teams, with each team responsible for a specific part of each build. “After six months, they’ve produced that result 25 times. They know what they’re doing! Then we rotate them to a new task.”
Why has Manor Build been so successful when other prefab manufacturers have launched with fanfare only to crumble into liquidation? It’s a question Rob has reflected on. “People jump on prefab, thinking it’s easy to do but there’s a lot more investment needed compared to a man and a van with his tools.
“I come from a background running a manufacturing operation and that’s crucial. It’s easy to start a prefab operation—it’s not hard to find people to buy them—but it takes a while to get to profitability. It takes financial acumen to make a success of it, you’ve got to run your books properly, keep timely accounts. That’s not a strong point for a lot of general builders. This isn’t an easy model but it works quite well for us. When I look at other crowds that have failed, it looks like a huge amount of borrowed money and that they clearly underestimated the time it would take to turn a profit.”
Manor Build currently employs two dozen staff. There’s 15 people on the floor building, backed up by support staff. The post-Covid construction slowdown made last year a bit quieter and headcount reduced a little but the firm stayed in the black. It’s looking like “a reasonably strong finish” to 2024, reports Rob.