Whakatū Passivhaus Nelson
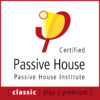
Whakatū Passivhaus deserves close investigation. It’s the first for its builder and architect/Passive House designer and the first to be certified in Nelson City (the nearby Orr Residence is located in the adjoining Tasman District.) There’s a lot more going on here than the simple form suggests.
Passive House performance is the gold standard for operational carbon efficiency. This project has also been intrinsically shaped by a staunch commitment to minimising embodied carbon as well, in order to mitigate climate change. On a material level, Whakatū Passivhaus diverges not just from Code-minimum design but also typical Passive House design in New Zealand.
A concrete foundation is notably absent. The design strove to reach the carbon budget required to meet net zero carbon by 2050, as modelled in the BRANZ LCAQuick tool. The designer notes a slab foundation alone typically gobbles up 80% of a home’s embodied carbon budget. Therefore, this house sits on piles despite challenging ground conditions and a hillside location.
The designer wanted to incorporate as much prefabrication as possible to minimise material waste. He also wanted to minimise the distance materials travelled to his site. Nelson’s distance from New Zealand’s two SIP manufacturers was an issue for this reason. The designer had already worked with Potius Building Systems, a local engineering and construction firm, on commercial projects. The panelised products it could supply met all the design requirements. The roof, internal and external walls, midfloor and floor were all made in a local factory, with the timber being harvested within a 100 km radius.
The panels are a double stud construction: 190mm top and bottom plates with offset 90mm studs at 600mm centres. The weather control layer was fitted in the factory and an average of 80mm of PUR foam sprayed into the cavity. PUR delivers excellent insulation performance but there’s a limit to how thick a single coat can be applied. Fibreglass insulation was blown in on-site to fill the remaining cavities after the air control layer was installed.
The fully-timber fabric meant no thermal bridges. Side benefit: no need for thermal bridge modelling in PHPP! A decision was also made to avoid services in the external walls. This was achieved, bar a single powerpoint. It typifies the ‘keep it simple’ philosophy of this project.
The simple footprint reflects this too. The two-storey, rectangular form has an excellent form factor. The house was designed to maximise solar gain in winter and the effect can be seen in the low heating demand figures. Cross-ventilation, night-purging and experimenting with the bypass function on the MVHR will be used as summer approaches to prevent overheating.
The rigour of the owners’ research, plus their sincere commitment to the best possible environmental outcomes, shines through here. Their determination has produced a home that delights them with its purity of form and effective function.
Project Team
Architecture & Passive House Design Nathan Edmondston
Builder Basham Building Limited - bashambuilding.co.nz
Certifier Sustainable Engineering Ltd – sustainableengineering.co.nz
Passive House Metrics
- Heating Demand10.0 kWh/m2/year
- Heating Load9.5 W/m2
- Frequency of overheating9.5%
- TFA106.8m2
- Form Factor3.3
- Air leakage @ 50Pa0.3 ACH/hour
- PER demand44.4kWh/m2/year
Passive House Database - TBA
Construction Details Average Values
- U-value External Walls 0.21 W/(m2K)(R4.7)
- Two 90mm Timber Walls with minimum 40mm Heatlok PUR spray foam and Jet Stream Max insulation
- U-value Floor0.21W/(m2K)(R4.9)
- 190mm Timber Joists with minimum 50mm Heatlok PUR spray foam and Jet Stream Max insulation
- U-value Roof 0.20W/(m2K)(R5.1)
- 190mm Timber Joists with minimum 50mm Heatlok PUR spray foam and Jet Stream Max insulation
- U-value Glass0.55 W/(m2K)(R1.8)
- Gealan Glass 4/18Ar/4/18Ar/4
- U-Windows1.0 W/(m2K)(R1.1)
- Gealan S9000
- Ventilation Efficiency 80%
- ComfoAir Q350