Internal surface temperatures are a key metric with regard to assessing mould risk. What level of performance is required for acceptably low-risk construction details and components (windows and doors especially)? How does internal surface temperature interact with ventilation, heating, occupancy and climate? This is an important area of study. It is likely in the near future to determine how window joinery is designed, for instance. Manufacturers and designers need to wrap their heads around fRSI and its implications in order to make sure their products and services are compliant.
Preventing thermal bridges, the cold spots they create and the likelihood of mould they bring is important but has been largely overlooked outside of the high-performance building sector. That’s all about to change: MBIE’s technical guidance on operational carbon indicates a minimum fRSI will be included in the NZ Building Code. And that until that time, the building industry should use values established by the Passive House Institute (PHI) or NZ Green Building Council. Note well that PHI fRSI requirements recently changed and more specific calculations are now available.
Sustainable Engineering’s team has been occupied lately with some detailed investigation into this issue, looking at indoor humidity levels and the resulting mould risk across all the different New Zealand climate zones.
How do we prevent surface mould? Understanding fRSI
The answer is ventilation and heating. The exact details and necessary performance of components and details is of course more complicated. We need to start with fRSI. I know this can make some people’s eyes glaze over, but it’s important to understand even the basics of what fRSI is, what the numbers mean and its implications for your designs or components.
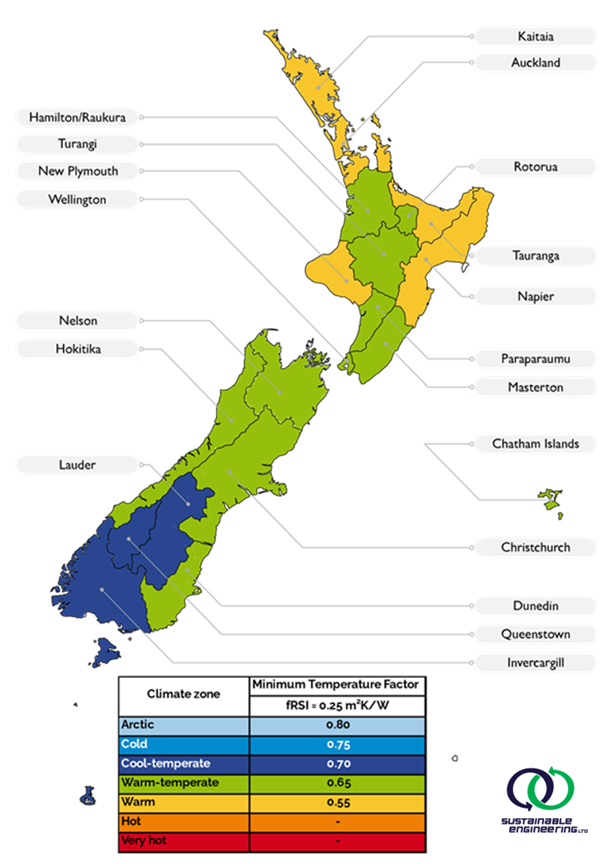
Figure 1: Older Passive House Institute PHPPv9 fRSI criteria based on climates (at the weather station altitude). These are overly conservative for many ventilation rates in our colder regions.
fRSI is a surface temperature factor. It’s to do with how cold a surface is due to the local thermal bridge. By this stage, we all get that thermal bridges are bad and lead to heat loss. But they are also bad because these bridges are the most risky places for mould growth. The temperature at the surface of an internal bridge (say, where a window meets the adjoining wall) will be cooler than the surrounding air. Condensation may develop, mould may follow. Because … say it with me, COLD SPOTS = MOULD SPOTS. Mould is bad for people and long term moisture in timber is bad for the structural integrity of buildings.
If the surface of a thermal bridge is colder than the air in the room, the air right at the surface of the bridge is colder and thus has higher relative humidity. For example, let’s consider this specific example (Junction 62 detail in the High Performance Construction Details Handbook).
- The air inside a New Zealand home in winter is 20°C and the relative humidity (RH) is at 60%. The window joinery is aluminium with a thermal break
- With a fRSI of 0.3, it can reach 15°C at the surface with an outdoor temperature of 13°C.
- At 15°C the air near the surface will be at 80% RH, a point at which mould growth becomes likely.
The fRSI can be calculated for specific building assemblies and then by assessing that value against established criterion, we can calculate the likelihood of mould developing. If the risk is unacceptable, then the building designer needs to consider how to remove that risk. The map above of the older Passive House Institute PHPPv9 fRSI criteria is what is used currently by NZGBC Homestar V5.
fRSI values will be between one and zero (note that both 1.0 and 0.0 are impossible results) and the higher the number the better. It’s a constant, construction-specific value. It doesn’t change depending on the temperature difference between inside and outside a building.
fRSI is a starting point for evaluating mould risk. To thoroughly assess risk is a little more complicated: the materials, the amount of time at high relative humidity and the moisture storage capacity of the surface all need to be considered.
Putting fRSI to use
The very best way to assess building assembly moisture durability and resistance to mould growth is to simulate the heat and moisture transfer over time. This is hygrothermal modelling, done using software such as WUFI. The Sustainable Engineering Ltd team carry out this type of modelling but it is too time consuming for this sort of cross-climate exploration style of work.
A reasonable approach we recommend is to first calculate the fFSI value at the critical junctions using Flixo or THERM software and then compare the result to fRSI limits established for the appropriate climate zone. This is relatively quick. If the assembly or detail is marginal, then we recommend a more accurate check using WUFI, either one or two-dimensional versions.
This study uses a limit of 80% surface water activity as the critical moisture level to stay below. The 80% surface water activity limit is nearly the same as the 80% surface relative humidity (differing only by surface adsorption rates). This is not the same as the relative humidity in the whole building. It is the relative humidity of a parcel of air at the mixed whole building if it was brought down to the surface temperature without gaining or losing moisture content. 80% is commonly recommended as a limit to stay below on an internal surface to prevent mould growth in the absence of more detailed hygrothermal modelling.
Important qualifier: meeting a fRSI moisture criteria doesn’t mean the building assembly will not mould interstitially as the fRSI value is only valid for the internally exposed surface. Moisture inside the building assembly depends on convective air and moisture movement as well as storage and transmission (both vapour permeability and capillary) in the materials and can be quite complicated to assess.
New requirements, new insights
Passive House certification has fRSI requirements that vary according to the climate zone of the building. In the past, the requirements were deliberately conservative and based on experience in similar climates, mostly in Europe. The criteria was improved in version 10, which determines the required fRSI value by using a building and location-specific moisture balance calculated in PHPP 10. This is why the criteria now changes with ventilation rate.
In the past, the assumption was that fRSI would be more difficult to meet in colder climates and previous versions of Passive House certification criteria reflected this. In PHPP 9 and earlier, the fRSI values ranged from 0.55 in Auckland and north (easier to achieve) to 0.65 elsewhere. However when a climate and building specific moisture balance is calculated, ie in PHPP 10, the opposite is shown to be true: fRSI requirements are easier to achieve as you go south as the colder climates have less moisture in the air and more drying potential when the outside air is heated up to 20°C.
The moisture balance is calculated in PHPP10 based on a number of inputs:
- climate location
- altitude above/below the site
- ventilation rate
- internal temperature
- internal floor area per person (which sets the internal moisture generation rate).
Why ventilation is so important
For any specific instance, where location, internal heating temperature and occupant area per person are fixed, ventilation is left as the only variable. Ventilation is crucial: meeting fRSI values relies heavily on continuous ventilation. Without this, the internal RH and thus the required fRSI would be a lot higher for any specific situation because low or inadequate ventilation means internal moisture levels rise and with it the risk of mould. In the modelling work we’ve been doing, we assumed continuous ventilation running all the time at the specified rate. Either a balanced mechanical ventilation system with heat recovery (not moisture recovery) or an extract ventilation system at the same rate would yield the same results.
I can’t emphasise enough how important adequate ventilation is to keeping relative humidity at acceptable levels indoors in the winter. However, it does have a cost as it increases heating demand. This is why we see instances of tenants blocking trickle vents or disabling extract fans. They create draughts, they make the home colder and this will be particularly evident if heating is inadequate or non-existent.
Occupancy levels also have an impact on fRSI values and these vary significantly across New Zealand homes. In the floor plans we reviewed in our research project, the smallest useful floor area-per-person was 14.4m2/person in a four bedroom home. Bespoke architecturally-designed homes typically see useful floor area-per-person numbers of about 50m2/person: that’s a huge range and obviously has big implications for indoor moisture as typically the ventilation rate is set by building internal floor area (or volume) rather than occupancy.
Findings
After reviewing the interaction between variables, we determined that it was easiest to understand the results for ventilation rate per person (NZBC G4 requires 7.5L/s per person) and 20°C for indoor temperature (which is set now by the MBIE BfCC operational carbon guidance). We are then able to tabulate the required fRSI in each NZ climate zone (assuming we are at the weather station altitude) as only a function of ventilation rate.
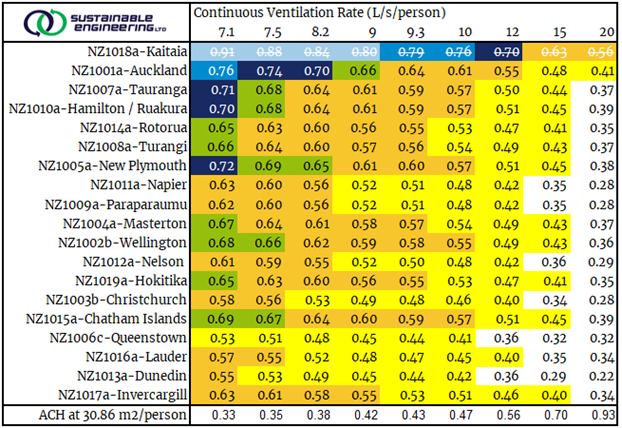
Table 1: fRSI required to stay below a surface water activity of 80% (80%RH on the surface) for different ventilation rates and assuming the location is at the weather station altitude. Cell shading colours are set to match the required fRSI from the old PHI climate zone figure. The bottom row is the ACH for the home if it has ~31m2/person of usable floor area.
Do note these fRSI calculations assume an indoor temperature of 20°C. We know many New Zealand homes are not heated or are seriously underheated. In such cases, a home may meet fRSI requirements as measured at design stage but still be at serious risk of mould developing. The lower the temperature, the higher the relative humidity, the greater the risk of mould—and other impacts on human health and wellbeing.
North of Auckland is a special case
Also note the strikethrough in Table 1 for Kaitaia fRSI requirements. This impractically high fRSI shows that ventilation and heating is insufficient for this climate and these homes need active dehumidification in the winter rather than better constructions with higher fRSI.
Limits of the study
It’s important to note the limitations built into our study.
- fRSI requirements address surface temperature on the interior surface of the building and tell us little of interstitial condensation or mould risk.
- This moisture balance is for the coldest month of the year, (a projected next coldest month from a linear fit of the coldest months in the climate file). This means that surfaces that experience seasonal or potentially even diurnal temperature swings (like concrete floors and walls) and that are exposed to warm, moist air in the summer months may experience higher surface water activity than is projected by this fRSI index and moisture balance.
- The internal heating temperature is assumed to be 20°C throughout the study. We examined lower temperatures such as 18° or 16°C and these result in theoretically impossible fRSI requirements. This points out the need for heating in winter months as mould prevention via ventilation alone is insufficient, no matter how much ventilation is provided.
- The results depend heavily on the occupancy of the home. If a lower occupancy is used for design the fRSI is reduced. There is a risk design teams may manipulate occupancy rates to create artificially low fRSI numbers that are easier to achieve.