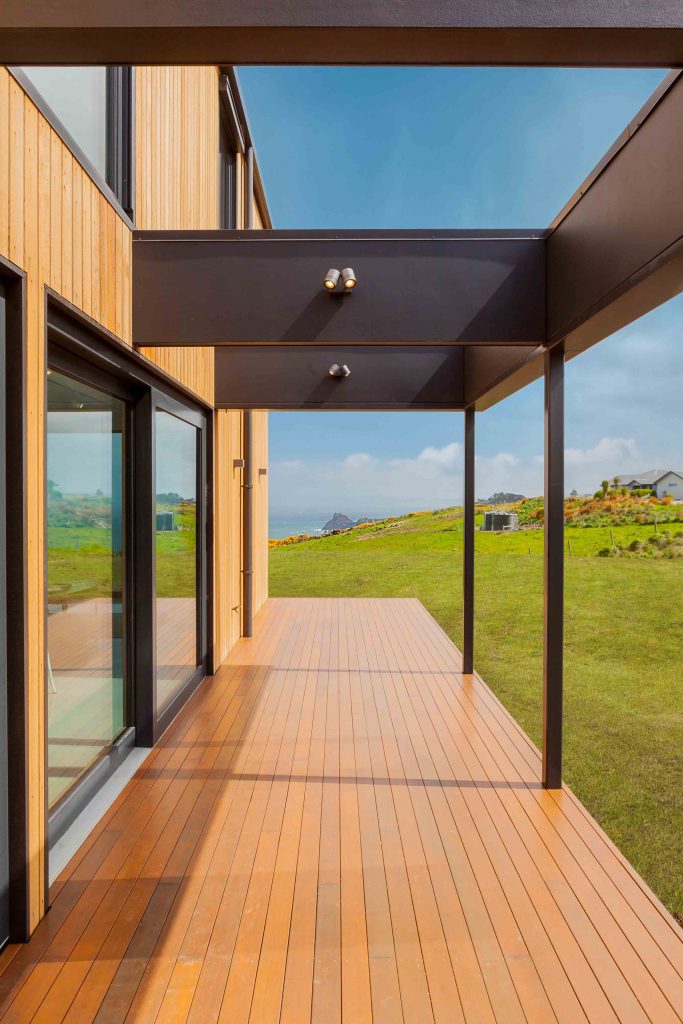
If the Passive House energy efficiency standard were adopted at scale in New Zealand, it would bring about a revolution in people’s health and comfort. It would also deliver significant benefits with regard to the environment in general and the climate in particular.
From tiny beginnings in 2011, when the first New Zealand Passive House was designed, this standard is gaining ground. At the beginning of 2019, there are 24 Certified Passive Houses that meet its exacting standards of energy efficiency and scores more built to (or near) the standard. All of these go far beyond the legal minimum of the New Zealand Building Code.
What is Passive House?
It’s a building that uses tiny amounts of energy for heating and cooling, so it’s very cheap to run. It’s very quiet inside and the temperature is comfortable and constant—everywhere in the house, all the time. The indoor air quality is outstanding thanks to high-level filtration; that’s good for everyone but especially for occupants with respiratory issues like asthma or who suffer from seasonal hay fever.
At a more technical level, Passive House is an open source standard for extremely energy efficient buildings. A certified Passive House uses no more than 15kW per square metre, per year to heat a building (and the same amount again for cooling, if required). That’s 81 % less energy than is used to heat a typical
The standard also sets an upper limit on air leakage (explained on page 34) and requires a comfortable indoor temperature (because freezing homes that are not heated at all also use very little energy!).
Passive House is a process as much as a standard. A Certified Passive House requires attention to detail and careful planning, from the initial design phase through every stage of construction. The quality of the build is independently verified by rigorous on-site testing.
As well as Passive House Classic, there are two other related classes:
Passive House Plus generates the same amount of renewable energy each year that the building uses. That’s total energy use, not just energy for heating and cooling. It also accounts for energy storage losses—it’s an honest
Passive House Premium generates as much renewable energy in a year that the building occupants use in their daily lives. It’s set at a level to make a fully renewable energy grid work for everyone.
Sweden is taking climate change seriously and has committed to completely eliminate CO2 emissions by 2050. The city of Växjö has funded two high-rise Passive House apartment buildings. They cost 5–10 % more to build than their conventional equivalent, quickly offset by their dramatically lower running costs. The EU has directed that all new buildings must be close to zero energy consumption by 2020.
In addition, EnerPHit is a standard for retrofitting existing buildings to the Passive House standard.
In New Zealand’s largely temperate climates, Passive Houses typically need no heating for almost all the year. For brief periods in winter, heating (for the entire house) may be provided by a radiant panel in a bathroom or a
Some Passive House owners have installed small heat pumps, given their efficiency and capacity to cool in summer as well as heat in winter as required. Heat pumps are so energy efficient that the cost to heat an entire 100 m2 house would be scarcely more than the energy used by a late-model fridge.
The case studies in the following section vividly illustrate how little active heating and cooling is required.
Other than that, Passive House is not prescriptive. A house may be any size or style, and use a range of different techniques and materials. The client’s requirements and the designer’s preferences can all be accommodated, as the following case studies demonstrate.
There are multiple ways to achieve the required performance, which builds in flexibility. For instance, increasing floor and ceiling insulation could compensate for large, south-facing windows that open out onto a spectacular view or the private side of a small site. Or, opting for top-end glazing could allow for simpler details when insulating a concrete slab.
Collaborating not competing
Passive House can work seamlessly with considerations such as choice of site, enabling ageing in place, healthy building materials or prefabrication. Passive House gets vital, universal fundamentals right: extraordinary energy efficiency and human comfort and health. On top of that, different projects, designers and clients can specify other requirements that are important to them (for instance, see the iDEAL home on page 46) and may use rating systems like Homestar (for residences) and Green Star (for commercial buildings).
What’s the difference between Passive House and Certified Passive House?
All genuine Passive Houses are designed to meet the performance targets
outlined in the standard. A Certified Passive House has been independently verified: it’s a mark of assurance and quality. It confirms that the building as been constructed well: the actual performance should equal the theoretical performance predicted in the design phase and all Passive House targets have been met.
Certification provides peace of mind for all involved. The client knows they have got what they paid for. The designer knows their work was correct. And the construction team know their job was well done.
Certification may bring a premium when it comes to resale of the building, as it happening overseas (in California, sales of single-family homes with third party certification are averaging 9% more).
Note that Passive House is not a trademark so anyone can use it—although The Fair Trading Act prohibits false or misleading claims.
How is that possible?
The short answer is: because they are designed that way. Buildings should be designed for function, not only aesthetics. The early developers of the Passive House standard cared about how buildings performed: what they were like to live or work in, and how little energy they could take to run. These concerns drove the development of the technology and shaped the performance targets.
What’s “air change”?
Air changes per hour (ACH) is a measure of how many times an hour the entire volume of air within a house is replaced. For the sake of definition, it is expressed as ACHn 50, air changes per hour at 50 pascals. That is a measure of air pressure, equivalent to a moderately windy day*.
Myth No. 1: Passive Houses are for cold climates, it’s overkill for New Zealand.
You might still hear this from some factions within the building industry but it’s rooted in a lack of understanding of what Passive House is. It’s true that Passive House (or Passivhaus, in German) was developed in Europe’s much colder climates. But the standard is used successfully around the world, including in temperate climates more like ours, such as California, Vancouver and south-east Australia. Passive House sets a performance standard—it doesn’t dictate what is required to reach that. So it’s easier and cheaper to build a Passive House in New Zealand compared to say, Bavaria, where winter temperatures can plunge to -15°C. Less insulation will be required, perhaps double-glazing instead of triple. Even within New Zealand, it is simpler to reach the performance target in Northland compared to Queenstown. The designer or architect adjusts the design to take into account the local climate. (That’s why accurate regional climate zones are so important to efficient and accurate Passive House design—see page 6.) A New Zealand homeowner gets all the benefits of a Passive House, at a cost and complexity that scales to suit the conditions.
Myth No. 2: Passive solar is just as good, without the fancy price-tag
Don’t confuse Passive House with passive solar, an approach that relies on a north-facing orientation, concentrating glazing on the sunny side and storing energy in high-mass materials. It’s not feasible in many circumstances, for instance if building medium density housing on small lots where aspect is not ideal, or if the million-dollar views are to the south. Passive solar exponents talk about achieving comfortable average temperatures, but that average can conceal significant and uncomfortable variations in indoor temperature. Passive solar thinking and design has improved since its origins in the 1970s but there is no standard, no independent verification and no way to accurately predict how a building will perform beforeit is built. A Certified Passive House uses passive solar gain if it is available but crucially, can calculate the effect of that energy at the design stage and include it in the performance modelling.
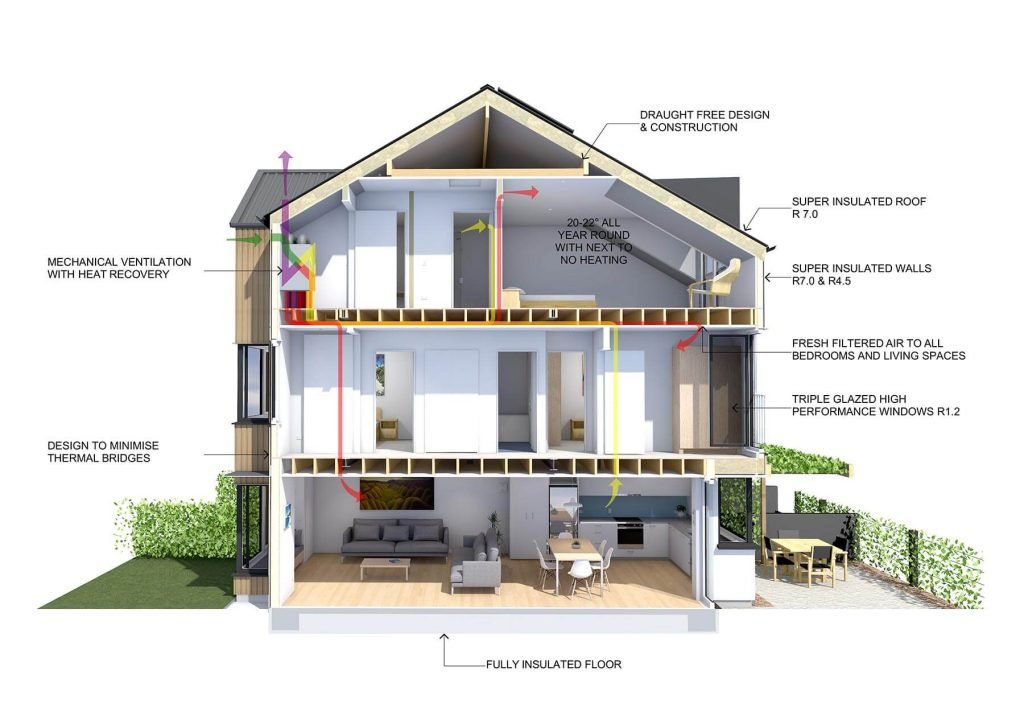
Any particular project can meet the standard by using the following elements, combined in different ways to suit the circumstances (the particular climate zone, aspect and other site opportunities or constraints, client preferences etc).
Excellent insulation
Floors, walls and ceilings are all carefully and thoroughly insulated to prevent heat loss. The amount of insulation varies, mostly to do with the climate. For instance, in
Even the very best windows conduct more heat than walls. Double-glazing is called for in a Certified Passive House in all parts of New Zealand, with triple- glazing sometimes needed because of climate or building shape.
Glazing performance can be improved using coatings and fills—low-E coating and argon fill are the most common but there are other specialist treatments available.
The joinery is the other consideration. Cheap double-glazed windows sit in thermally conductive aluminium frames. Heat will readily leak through the frames and the difference in inside and outside temperature will cause condensation to build
Thermal bridge-free zone
There are no weak links in a Certified Passive House. Joinery doesn’t leak heat and neither do any other junctions or components. In conventional construction, thermal bridging happens where the foundation meets the walls, the walls meet the ceiling and roof and where steel columns are used. Details are used in Passive House design to eliminate all such points that allow for heat to escape (or penetrate, in a hot climate).
Building envelope
The whole building interior is encased in an uninterrupted air control layer—also called an airtightness layer. Attention to detail on the part of construction teams is needed to make sure this layer is installed correctly.
This innovation plays a crucial part in ensuring Passive Houses need so little energy to heat. It prevents the loss of heat and draughts; the high levels of insulation can then stabilise the internal temperature. It also prevents moisture damage to the building structure and is key to building durability.
Mechanical ventilation with heat exchange
Fresh air is good and Passive Houses ensure it. Clean air is provided through a small and extremely quiet continuous mechanical ventilation system. Incoming air is filtered of dust, pollen and particulate pollution. A clever heat-exchange system recovers about 90% of the heat in the stale air being expelled and uses it to warm the incoming air. This prevents any sensation of draught.
It’s important to understand that ordinary homes currently being built to the Building Code minimums are also much more
What’s it like to live in a Passive House?
Very, very pleasant.
The temperature is always comfortable, no matter what it’s like outside. (You may need to check the weather forecast or stick your head out the door to tell if you need a warm jersey when you’re going outside.)
The air inside will be fresh, clean and a comfortable temperature, even with the windows closed. It will be quiet and peaceful: you can close out the noise from neighbours or traffic.
And your power bills to achieve this level of comfort? They will be tiny, as illustrated in the case studies that follow.
Myth No. 3: You can’t open the windows in a Passive House—and who wants to live in a sealed box?
Of all misguided objections to Passive Houses, this is the stupidest. Of course you can open the windows! Some of the beautiful homes featured in the following section boast magnificent lift-slide doors that open up a whole wall of the house.
If you want the fabled indoor-outdoor flow, to keep an eye on the kids, or the sound of birdsong or ocean to drift through the house, go right ahead and throw open your windows.
But if you have neighbours who mow their lawns at 8am on Sunday, come home late at 2am or like to argue loudly at any time or day or night—or you live on a busy road with constant traffic noise—you might well appreciate how quiet your Certified Passive House is with the windows closed. Double (or triple)–glazing offers significant acoustic as well as thermal insulation.
The point is, you don’t have to open windows and doors in order to ventilate your home, because your home is doing it for you: constantly providing fresh, filtered air at the same temperature. That way you’ll never feel a draught and you’re not paying to heat (or cool) air that is escaping outside. Your indoor air quality will be outstanding, no matter what is happening outside.
You want indoor outdoor flow? How about 26 an opening more than 8 metres wide?
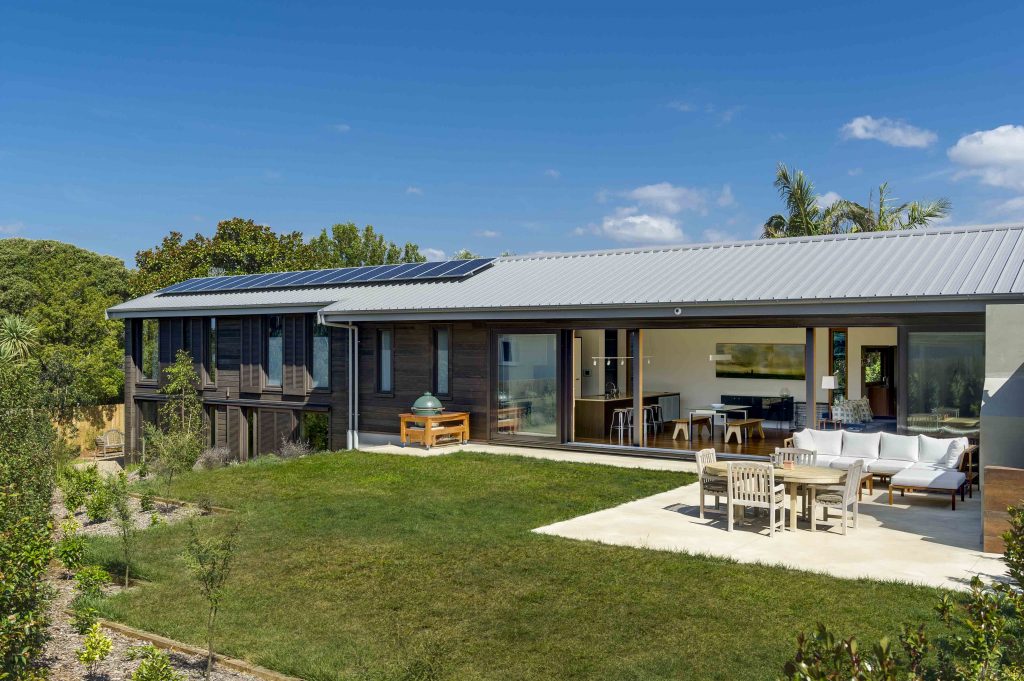
The first clients specifying Passive House in New Zealand were mostly people who had lived overseas and were used to far better standards of comfort and efficiency than even newly built New Zealand homes offered.
But this stage of early adoption is over. The Passive House Institute of New Zealand (PHINZ), a charitable trust, is actively educating and informing New Zealanders. At the beginning of 2019, there are 26 certified Passive House designers or consultants. Passive Houses have been built and successfully certified from Wanaka to Auckland. They include luxury, bespoke, million- dollar homes through to affordable family homes with a modest footprint.
Excellent designs can be entrusted to building firms that are quickly amassing experience in constructing Passive House details. There are now 33 Certified Passive House Tradespersons in New Zealand, trained in the specifics of building Passive Houses.
Underpinning Passive House design is the analysis done in energy modelling software called the Passive House Planning Package (universally referred to as PHPP). Courses are offered in New Zealand each year that teach its use to architects and designers;
Remember the old saying, “measure twice, cut once”? That’s what designers can do, thanks to PHPP, testing iterations of their design until it reaches certification standards.
Passive Houses have been built in 40 countries around the world, in climates zones as varied as the tropics and Antarctica. The very first Passive House was finished in 1991 in Germany. Nearly 30 years on, it continues to perform as it was modelled.
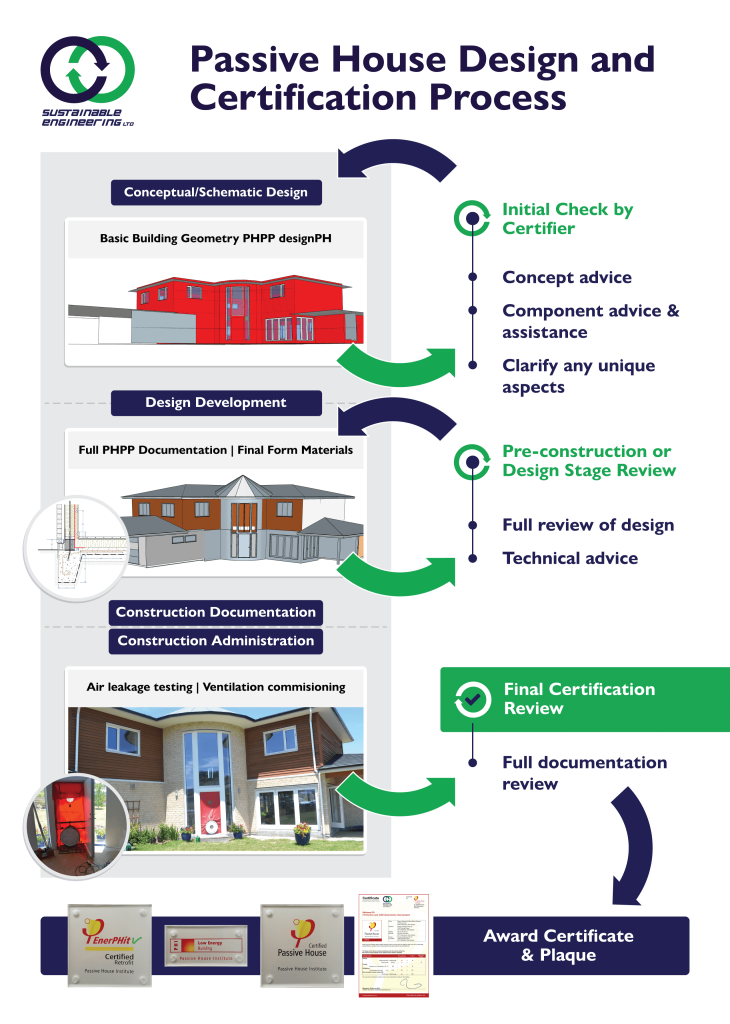
Independently certified
Certifying a Passive House provides an independent guarantee that a new build will perform to the standard. The actual certification costs are not expensive, a mere half a per cent or less of an average new build.
It happens in two phases that parallel the building design process. The certifier will first review the
During construction, a blower-door test is performed on site—once the air control layer is in place but before any internal finishing. If there should be any issues with air leakage, the problem can be most readily tracked down and fixed at this stage of construction, before wall linings are fixed.
Secondly, once construction is complete a final blower door test is required. This provides scientific verification that the project meets the air changes per hour (ACH) standard. This serves as a check on the quality of construction.
Further, photographs are submitted to the certifier that
Internationally, independent verification is shown to increase resale value and it is very likely this will happen in New Zealand.
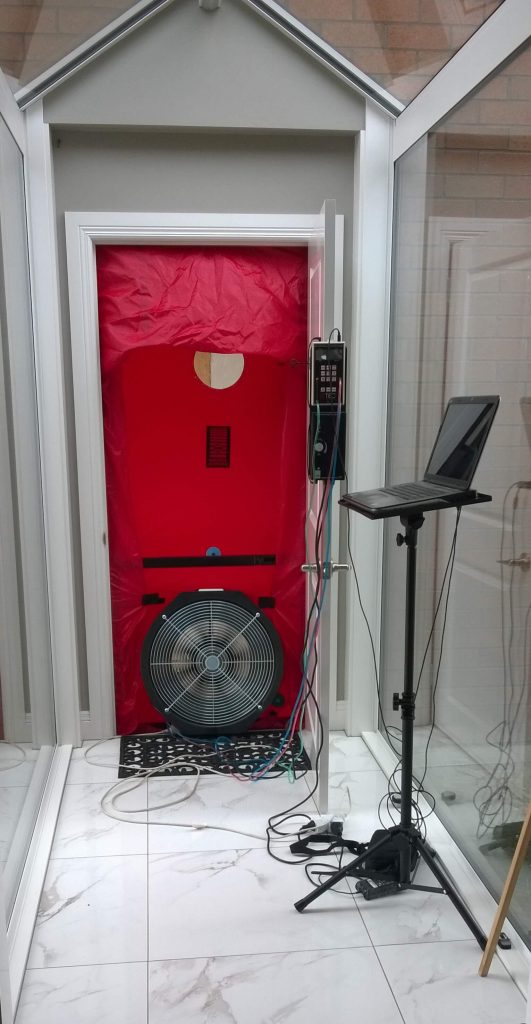
This is used to pressurize a building and measure how much air leaks out.
Creating Resilience On a systems level, constructing new buildings and deeply retrofitting current buildings to the Passive House standard has the potential to dramatically contribute to carbon reduction targets. Buildings account for 40 % of energy use in developed nations. (In New Zealand, buildings are only 20 %—only because of our high agricultural emissions, which are an anomaly for a developed economy.)
At an individual, community and city level, building to Passive House standards will increase resilience to freak weather events and steadily rising average temperatures.
We urgently need resilient buildings and other infrastructure that can keep functioning despite freak weather events. Climate change is making itself felt by more extremes in weather: highs, lows, storms, droughts.
It is possible to build Passive Houses for outrageously hot climates like Australia and the Middle East. It is being done already and it needs to happen on a hugely increased scale. A Certified Passive House in Queensland or NSW—whether a home, apartment block, factory or office—would be an energy miser, ensuring occupants stay comfortable while still using an absolute minimum of energy. That means human comfort and safety, plus vastly reduced demand on the grid (and by extension, the planet).
In climates where energy is needed to cool, not heat, renewable energy makes even more sense. The peak demands on the grid (and stand-alone generation systems) occur during the day when the sun is shining, exactly when photovoltaic generation is also peaking.
If developed nations are to reach emissions reductions necessary to slow climate change, we must slash the energy required to run buildings, both residential and commercial. Passive House can do this.
Australian grid overwhelmed during heatwaves
South-eastern Australia has suffered prolonged heatwaves during the past two summers and maximum temperatures records have been smashed. In 2018, temperatures topped 45°C in NSW, Queensland, Victoria and South Australia, earning Australia the dubious title of “hottest place on earth”. The effects have been far-reaching and serious—deadly, even. Such heat reduces the capacity of transmission wires to carry electricity even as demand for electricity soars due to the use of air-conditioning units. Wholesale power prices soared to an unprecedented $AUD14 per kW/hr during peak demand periods in 2017, compared to a more typical $AUD 0.10 per kW/hr. The price spiked again in 2018, despite expansions to the grid’s capacity. Rolling blackouts and planned outages occurred along the eastern seaboard in the 2016-2017 summer, as all systems strained under the load.Image Credit:
First Photo: Gemmel House – PHINZ
Second Photo: High Street Cohousing Cross Section – Architype
Third Photo: House with Double Lift Slide – Ecowindows