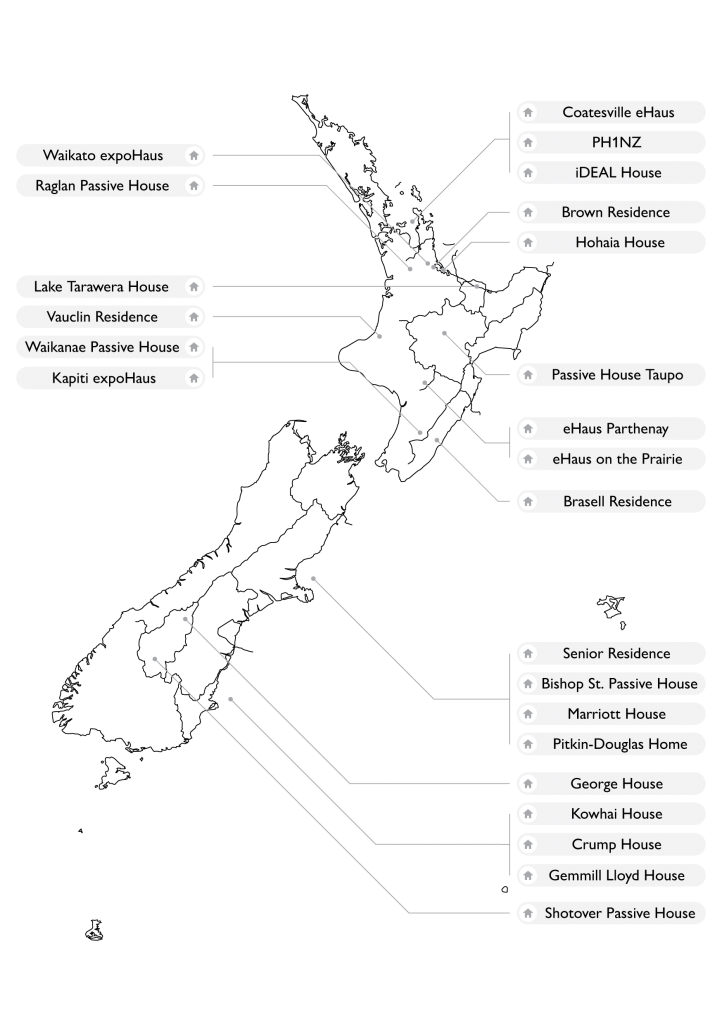
New Zealand’s first certified Passive Houses
Meet the first 24 family homes whose outstanding design and build quality has earned them Passive House certification. They range from Auckland to Wanaka, from award-winning, luxury residences to more affordable, modestly-sized family homes. There is diversity in their appearance and the materials used in their construction.
Their owners’ motivation for choosing a Passive House varied. All are alike in valuing their experience of living in a Passive House: the indoor air quality, the optimum indoor temperature, the peace and quiet, the tiny energy bills. This is good for those who live in these exemplary homes—and good for the planet
Those involved in bringing each of these houses to fruition believed in the value of certification. Each house has been independently verified to perform to the standards established in the design phase: the teams that built them got them right. Energy modelling means that performance can be accurately predicted during the design phase. Then blower door testing of the house once built confirms the quality of the design and construction.
Six years on from those pioneering builds, the environment has changed enormously. As you’ll see detailed in the following stories, key components like windows are easier to
These 24 houses are the apex of a much more widespread change.
The legend that follows is worth your attention. Passive House metrics use terms that may be unfamiliar. They are simply and clearly explained below. Once you understand these terms, the metrics listed below each case study will show you at a glance where a house excelled and the challenges it faced in being certified.
Links to Case Studies:
- Kowhai House – Dunedin
- Brown Residence – Cambridge
- Gemmill Lloyd House – Dunedin
- Senior Residence – Christchurch
- Pitkin – Douglas Home – Christchurch
- iDEAL House – Auckland
- Hohaia House – Hamilton
- eHaus Parthenay – Whanganui
- Waikato expoHaus – Hamilton
- Shotover Passive House – Queenstown
- Lake Tarawera House – Rotorua
- Waikanae Passive House – Waikanae
- Bishop Street Passive House – Christchurch
- Kapiti expoHaus – Kapiti
- Passive House Taupo – Taupo
- Coatesville eHaus – Auckland
- George House – Queenstown
- Crump House – Dunedin
- Vauclin Residence – New Plymouth
- Marriott House – Christchurch
- Brasell Residence –
Waiarapa - eHaus on the Prairie – Whanganui
- Raglan Passive House – Waikato
- PH1NZ – Auckland
Legend
Heating Demand: This is the amount of heat required to keep the home within the acceptable, comfortable temperature range, expressed as the amount of kilowatt hours per square metre per year. (This is approximately 5–30% of the heating demand of a modern house built only to the Building Code minimum.)
Heating Load: The power used by a heater of sufficient size to maintain the comfortable temperature on the coldest days. (Note the heating load is expressed in watts, 1/1000th of a kW. A 200 m² Passive House can typically rely on a single 2kW heater—the size of an average portable fan heater or oil-filled column heater.)
Frequency of Overheating: A certified Passive House must not overheat—defined as 25°C or above—for more than 10% of the time.
TFA: Treated floor area is a measure of the useful floor area inside the conditioned area of the home. It excludes stairways and wall thickness (both exterior and interior).
Form Factor: A ratio arrived at by dividing the total external surface area of the thermal envelope by the treated floor area. A multi-storey building will have a lower form factor than a single-storey dwelling. A simple shape like a square or rectangle will also have a lower form factor than a more complex shape. The lower the number, the less insulation needed in the same climate.
Air leakage: A crucial measure of building quality and major benefit of Passive House certification. Measured via a blower door test done toward the end of construction and verifies that the building will perform as modelled. It can be used as a proxy measure of the quality of building construction. A Certified Passive House must come in under 0.6 air changes per hour (ACH) at 50Pa (ameasure of air pressure, equivalent to a moderately windy day). A well-built conventional house constructed to Building Code minimums is typically 3.0 ACHn 50, five times leakier.
PER demand: Primary Energy Renewable demand measures total energy usage in the house (not just energy for heating and cooling) and includes (a) the power lost to the grid as power is carried from the power station to the home, (b) storage losses (as if the grid were fully renewable) and (c) losses in converting non-renewable fuels to electricity. Excess solar power generated in summer needs to be stored for winter use. PER demand is expressed on a per square metre basis per year. To calculate it for a specific house, multiple the PER demand by the building’s TFA. A certified Passive House must be below specified maximums, which depend on the degree to which power consumed comes from renewable sources generated on site.
PE demand: Primary Energy demand has been superseded by PER demand but you’ll see it referenced in older case studies and it can still be used on new buildings as well. It measures total energy usage in the house (not just energy for heating and cooling) and includes the power lost to the grid as electricity is carried from the power station to the home and the losses in converting non-renewable fuels to electricity. Buildings are required to be below 120 kWh/m2 /year if they certify using PE demand.
RE generation: measures the total amount of renewable energy generated onsite. This threshold is relevant to Passive House Plus and Passive House Premium builds.