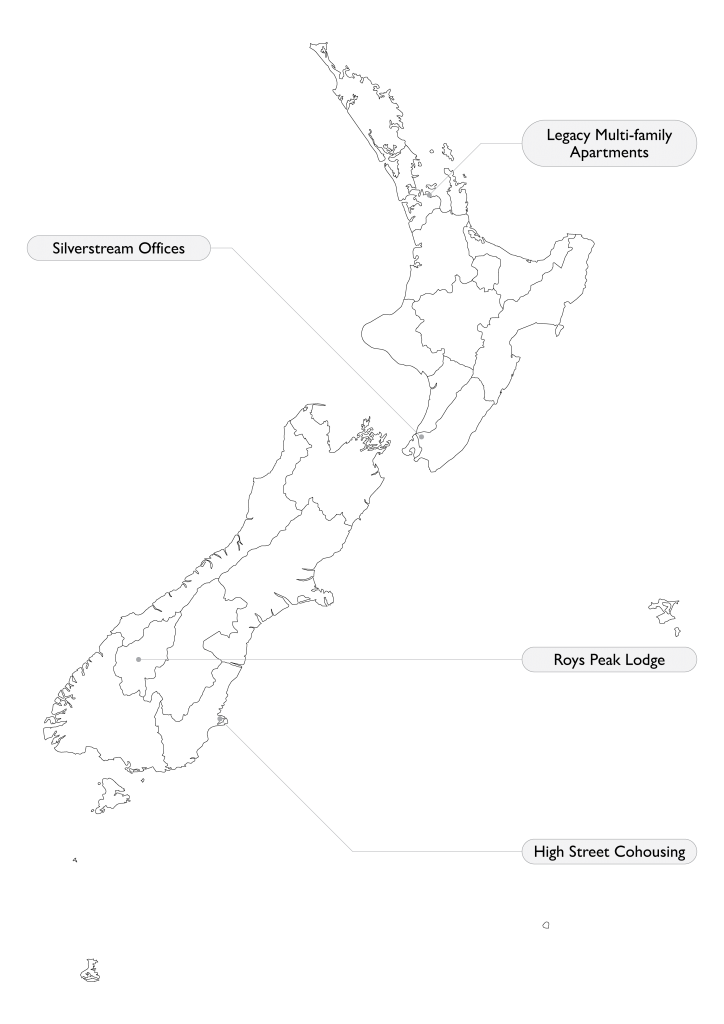
The next phase for Passive House in New Zealand
This year, 2019, could be a tipping point for building quality, health and performance in New Zealand. The pioneering phase for Passive House construction of
All the components are now in place
Design teams. As 2019 begins, there are 26 Certified Passive House architects, designers and consultants from Auckland to Dunedin. That’s a growth of 400 % in just six years.
Builders. Passive House certified builders have got their feet under them. Builders who have built their first couple of houses have the experience they need to confidently take on larger, more complex projects. Take Otago firm Stevenson & Williams Ltd: Master Builders since 1955, the firm has Legacy Multi-family Apartments pg 92 Silverstream Offices pg 94 High Street Cohousing pg 88 Roys Peak Lodge pg 90 84 85 successfully completed two Certified Passive House single-family dwellings in Dunedin and is now at work on a 24-unit cohousing complex (page 88).
Components. Back in 2011, the pioneering Passive House in Raglan (page 80) was plagued with delays because of the difficulties in sourcing key components like windows. All that has changed. If clients want European or locally made high-performance windows, there are options to choose between. More affordable New Zealand-made uPVC windows are now also available. Technological innovation continues at pace, with products morphing into systems that make construction faster and more resilient. Take Izodom’s approach to insulated concrete forms (ICF): it doesn’t just create highly insulated, durable walls but easily integrates with foundations and
Regulators. More planners and building inspectors in local government are familiar with Passive House methodology, recognise the quality of the build and its components and are supportive of its goals.
All that is needed now is a wider understanding of the importance of quantifiable energy efficiency, health and comfort in our built environment—and the will to build it.
Not just a house “Passive House” is a direct translation of the German word Passivhaus, where haus means “building”. In English, “Passive House” suggests a focus on residential homes, but this is misleading. Any type of building can and is being built to the Certified Passive House standard internationally: office buildings, kindergartens, supermarkets, apartment buildings, warehouses and factories.