“Better than new”: refurbs an opportunity to lift standards Wellington
Click to view the pdf case study: Book House-CaseStudy#01
A dilapidated Art Deco apartment block in central Wellington is resurrected, thanks to a committed new owner and expert advice.
Sophisticated hygrothermic modelling clearly identified the way to approach the project. That insight saved money in the long-run and delivered a healthy, durable building: one that performs better than a modern building built to minimum Code requirements.
Book House was built of poured concrete in the 1940s, a three-storey walk-up apartment block with shops in a part-basement opening onto Plimmers Steps. In the 1970s, it was converted to professional rooms and another storey unsympathetically plonked on top.
When it was sold in 2007—having been already re-converted back to apartments—it appeared Book House’s days were numbered. Australian developers planned to bowl it and build a 21-storey apartment block on the site. But that project foundered, and five years later the building was sold off in poor condition with only two tenants remaining.
A Wellington buyer stepped in to restore the building and hold it as a long-term investment. An experienced property investor with a diverse portfolio, the new owner likes older buildings and values their heritage appeal.
The rebuild was a daunting prospect. The interior was dilapidated; some ceiling and walls were black with mould, plumbing leaked and paint was sloughing off. Outside, concrete cancer was spreading.
But today, Book House’s former tenants would scarcely recognise the place. The client wanted “A-grade” apartments, says John Ercolano of Workspace Architects, and that needed more than repairs and a coat of paint.
“This retrofit might seem like an interior-only job, but it is really a new building in old clothes. Retrofits are harder than new buildings and have more potential for issues.” — Jason Quinn
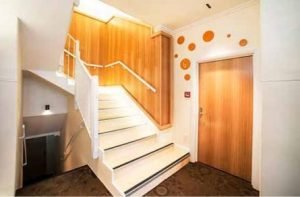
The walls and roof were insulated, ventilation installed and double-glazed, thermally-broken windows fitted. The interior was completely refitted, right down to wall linings and floors; and the floor plan was modernised.
The fully tiled bathrooms boast a high level of finish. Decorative motifs are carried through from the stairwells and lobby to lampshades and feature wallpaper in the apartments, unifying the design theme.
Happily, Book House was solidly built and sat at 80 % NBS before work even began. It is now fully 100 % NBS, without requiring major strengthening work. That’s not the case with many of Wellington’s older masonry buildings, says John Ercolano.
The issues: controlling water, air, vapour, heat
The cosmetic work is immediately appealing to a prospective tenant, but it’s really just the icing on the cake. The cake is good because of the ingredients that made it and key among these are the building enclosure layers. These need to control the flow of water, air, water vapour and heat—in about that order of importance.
Water is the easiest of the control layers to explain to clients; shedding bulk water is also the single most important task a building must perform. Fully 80 per cent of problems that lead to building failure and lawsuits in the US for instance, are caused just by rain: by it getting in where it shouldn’t, and then having no way to drain or dry out. It was the failure of the water control layer that caused New Zealand’s leaky building crisis in the ‘90s.
Adding to the complexity, this building’s original water control layer was not well designed. Some of the weaknesses are typical of art deco style buildings: a flat roof, undersized drainage, lack of eaves and no-drip edges. Given all this, controlling water penetration was critical to the refit’s success.
Controlling air leaks was also key because moist air carries with it a great deal of water. In the case of Book House, its poured concrete walls are the air control layer.
“There’s a valuable takeaway from the Book House example that applies more generally. New Zealand buildings are too often cold, damp and unhealthy. Retrofitting old stock for the sake of people’s health is important. But buildings are complicated and just adding insulation risks making older buildings perform worse than before. You can easily end up with a building that leaks a bit less heat but which is damp and mouldy, even when those problems didn’t exist prior to the refit. It is crucial to understand moisture and heat transfer and how added levels of insulation will affect a building’s drying capacity.” — Jason Quinn
To perform properly, this function needed to be recognised and respected, with junctions, interfaces and penetrations properly sealed. The weak points in this building were windows and doors in the concrete walls; and the added top storey, which had timber-framed walls meeting the original concrete structure and an equally difficult junction with the roof.
Tip – Make a specific person responsible for ensuring the air control layer is planned, installed, and inspected or tested.
Vapour control is much harder to explain—it’s the movement of moisture through the building materials themselves—but it’s crucial to building durability. “Seals don’t”, is the wry observation among industry professionals: in some way, at some point, the water and air control layers will be compromised and some amount of moisture will penetrate into the building structure. What happens next is key: does it have an opportunity to drain or to evaporate before it can cause damage?
In the case of solid masonry walls, they dry on the outside first when the sun shines on them. That warmth then drives a lot of moisture from the outside to the inside of the wall. Cold interior walls are bad news, because as building science consultant Jason Quinn always says, “Cold spots equal mould spots”.
He modelled the vapour drive through the walls using a WUFI® hygrothermic analysis—this simulates coupled heat and moisture transfer through materials.
Solid data was important because upgrading a building enclosure with insulation typically makes moisture problems worse not better. Drying potential is reduced as less heat is being driven through the assemblies. Stopping or reducing the heat leakage is good for internal temperatures and occupant comfort, but that escaping heat was increasing the
When insulation is added, wall performance has to increase.
drying capacity of the building mass. When insulation is added, wall performance has to increase.
The initial design called for wall insulation to be fitted to the interior, in the cavity behind the new wallboard linings. However, the WUFI® analysis showed that insulating the interior of the concrete block walls with fibreglass batts would create an extremely high risk of mould developing on the back of the insulation.
WUFI® calculates the vapour and liquid transport in materials, providing a visualisation of the moisture flow through materials and the means to assess if a building assembly is likely to fail. “I prefer to prototype in computer models instead of my client’s building,” says Jason Quinn.
The fibreglass is vapour permeable. In winter, when indoor temperatures are higher than outside, heat and moisture move outward through the wall lining and the batts. Once they reach the concrete wall, which is colder, moisture condenses and is trapped between the batt and the external wall. That’s a recipe for mould, hidden behind the wall lining.
Rigid insulation, like EPS foam, controls the vapour flow, preventing the rise of moisture between the insulation and concrete. Use of these products on the wall interiors wouldn’t have had the same risk of producing mould. But the interior concrete walls and mid-floors would have acted as thermal bridges, wicking cold into the heart of the building. (See Fig. 1)
When internal insulation is fitted, the mid- floors act as thermal bridges that conduct cold into the building. This creates cold spots in the wall, a high-risk factor for the development of mould.
Fig. 1 shows the difference between heat conduction in the case of external insulation (left) compared to internal insulation (right). Temperature factor (fRsi) is a constant, construction-specific value that is independent of any temperature difference between indoors and outdoors. It is calculated using two- or three- dimensional heat transfer simulation software.
The Passive House Institute (PHI) considers a fRsi of 0.65 to be needed to prevent the development of mould in this building’s specific climate.This value is current international good practice worldwide, says Jason Quinn. Applying external insulation to Book House easily exceeds this requirement.
Insulating the roof also required a new approach. Insulating the interior of the roof would have created similar issues as insulating the interior of the walls. The original 1940s roof was a timber roof with a very low pitch. The addition of the top storey created a hybrid roof line of concrete and timber. Accessing the timber roof over the old concrete slab roof was near impossible.
Solutions
For all these challenges, there were solutions. For the wall insulation, EPS-foam insulation panels (60 mm StoTherm) were fitted on the exterior of the walls, then 10 mm of S70 plaster applied. This makes for insulation twice as effective because all junctions are covered; there’s also no risk of mould developing inside.
The external option was more expensive because its installation required scaffolding. The decision was made easier when the extent of concrete spalling became known. Scaffolding was going to be required on all sides of the building anyway in order to remediate the damage to the structure and repaint the exterior. This made the best alternative an easy one to choose.
“It’s not as hard as you think — or necessarily as expensive—to do a refit properly.”
Jason Quinn
The balconies were much improved from a performance point of view. Insulation was fitted to the exterior and soffit and proper drainage installed.
The roof was repaired and air-tighted to the walls. Rigid PIR insulation was installed over the top of the existing roof membrane and a new TPO membrane added to produce a high- performing roof, considerably beyond Code minimums.
What we learned
Looking back after five years, Jason Quinn reflects on the advice he would give today on a similar project.
“In an ideal world the balconies would have been thermally broken, so that their junction wasn’t conducting heat out of the building,” he says. However, that would have required cutting them off and totally reconstructing them. The design team at the time considered the cost outweighed the modest performance benefit.
Installing the new roof highlighted the critical need for contractors and suppliers to understand the importance of airtightness, the characteristics of specific products and the implications of piercing air tightness membranes. The industry can expect contractors’ knowledge to continue to improve. “In the meantime, vigilant oversight by project managers and/or architects is called for, just as was provided in the case of Book House,” Jason Quinn says.
The building would have benefitted from a modern mechanical ventilation heat recovery (MVHR) system. At the time, the HVAC consultant focused on keeping ‘first costs’ down and a less expensive alternative was presented to the client.“I would now push harder to make the case for MVHR to the client,” he says. “Up to eight litres of moisture every
day is produced inside a home by an average New Zealand family; potentially much more. For the sake of the building and the people living in it, that has to be removed—and in a way that is acceptable to the occupants. Some fans are extremely noisy, and it’s not uncommon for people to disable them or not turn them on.”
Continuous mechanical ventilation with heat recovery would have delivered better performance and occupant comfort. These systems are very quiet and efficient and operate continuously to extract air from kitchens and bathrooms and deliver fresh air to living spaces and bedrooms.
The heat from air being extracted can be recovered and used to pre-heat incoming fresh air so there is no experience of draughts. (In hot climates where air-conditioning is in use, the same principle is used to cool incoming air.)
Various levels of sophisticated filters can also be installed, making indoor environments managed in this way highly suitable for people with allergies or in locations with poor outdoor air quality.
MVHR could have been installed on a per-apartment basis or as a centralised system. As in 2019, when this case study was prepared, this could have been achieved for approximately $6000 plus installation per apartment.”
The timber windows were all replaced with new, double- glazed units. The thermally-broken frames were made in New Zealand from uPVC; the glass has low-e coating and argon fill. This improved the insulation value of the glazing by 150 %. This was particularly important on the added top floor, which has extensive glazing. The new windows, as per the original design, are set back into the block walls and provide ventilation in accordance with the Building Code. Insulation was returned to the window frames (see Fig. 2), meaning no thermal bridges and no risk of mould.
Section of typical window head and sill showing the external insulation wrapping into the opening (no internal insulation).This creates concrete walls and window surroundings that are warm and dry, everywhere.
The rigid EPS insulation panels can be cut to any shape and the architects put this to good use. Additional fa ade elements were constructed from blocks of foam and these serve to accentuate the Art Deco appearance and unify the original structure with the top floor addition. Three new apartments were created on the previously open plan top floor, substantially adding to the property’s yield.
The only compromises are very minor thermal bridging where the walls connect to the uninsulated slab on grade (the suspended concrete slab was insulated), the ventilation and some minor thermal bridging it was deemed uneconomic to fix.
Wellington City Council mandates a certain volume of mechanical ventilation be supplied to each bedroom in apartment buildings within the CBD. This was achieved by installing fans to the exterior in bedroom walls that bring in fresh air from outside. To counter the draughts created in Wellington’s cold winters, small electric resistance heaters were fitted to pre-warm the incoming air. Extractor fans were also fitted over hobs in kitchens and in bathrooms.
With a complete, modern exterior insulation system and new joinery, this building now performs as well as any brand new building built in Europe. The chosen solution is best practice from the point of view of building durability, performance and comfort.
Project Team
Architects: Workspace Architects www.workspacearchitects.co.nz
Consultant Sustainable Engineering www.sustainableengineering.co.nz